Abstract
This study focuses on the thermal runaway characteristics and gas generation behavior of 100Ah lithium iron phosphate battery(LiFePO4) pouch cells. By triggering thermal runaway through side heating, we systematically analyzed the thermal runaway characteristics and gas evolution patterns at different states of charge (SOCs) of 40%, 60%, 80%, and 100% using characterization tools such as Industrial Computer Tomography (CT), Scanning Electron Microscopy (SEM), and Gas Chromatography (GC). The results show that the overheating trigger of battery thermal runaway can be subdivided into four stages: increased overheating temperature, by-product reaction gas expansion, separator shrinkage and cracking with smoke emission, and thermal runaway caused by severe temperature rise and gas production. Further calculation of heat generation energy revealed that at 100%, 80%, 60%, and 40% SOC, the peak heat generation rates reached 140.34 kW, 115.44 kW, 14.76 kW, and 3.91 kW, respectively. At 100% SOC, the energy released is equivalent to 104.63 grams of TNT, with a destructive radius of 5.90 meters, representing a nearly 64.3% increase in hazard compared to 40% SOC. Characterization of battery materials post-thermal runaway indicated that lithium iron phosphate battery(LiFePO4) cathode material transformed from a block shape to aggregated irregular spheres, and the graphite anode structure changed from layered to aggregated spherical particles due to accentuated internal side reactions. Comparison of gas evolution characteristics showed that with increased SOC, the amount of H2 produced by the battery increased, while CO2 decreased. The explosion risk of the gases produced at various SOC levels is higher than that of common hydrocarbon gases, with the explosion upper limit first decreasing and then increasing. The results of this study provide a theoretical basis and practical guidance for the safety design of follow-up energy storage systems.
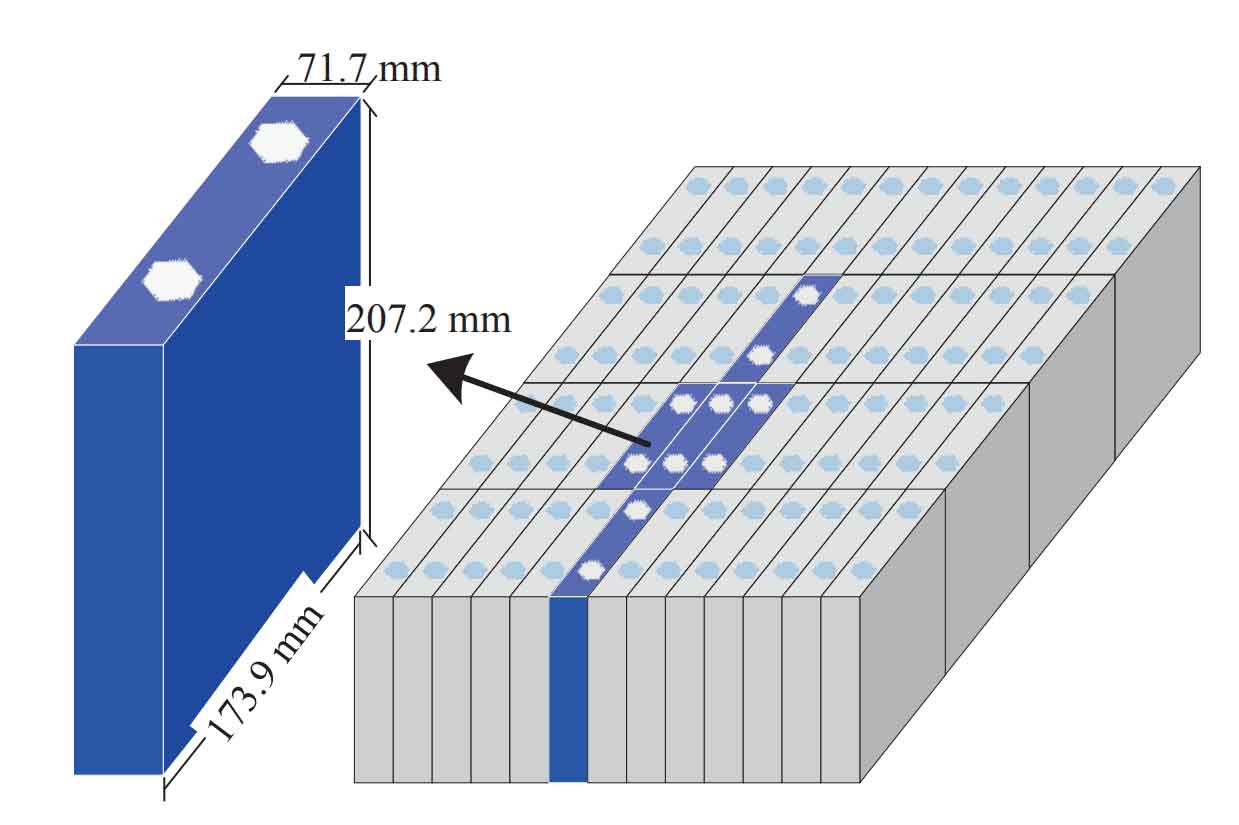
1. Introduction
In the context of global carbon neutrality and carbon peaking, the new energy sector is facing tremendous development opportunities. Lithium-ion batteries (LIBs) have become the core energy storage technology in consumer electronics, energy storage power stations, new energy vehicles, and aerospace due to their unique advantages such as small size, high power, high energy density, and long cycle life . However, LIBs face the risk of thermal runaway (TR) under extreme operating conditions, such as overcharging, discharging, extreme temperature environments, or internal short circuits. This not only affects battery performance but can also lead to fires and explosions . Therefore, in-depth research on the thermal runaway characteristics of LIBs is crucial for improving battery safety and promoting the healthy development of the new energy industry.
Recent studies on the thermal runaway characteristics of LIBs have been conducted from multiple dimensions, including trigger methods, test conditions, and battery materials. Zhu et al. compared the overheating behavior of 25Ah LFP pouch and prismatic batteries and found that the packaging form primarily affects thermal runaway through the mechanical properties of the packaging material. The pressure relief valve of the prismatic battery effectively delays thermal runaway. Wang et al. studied the thermal runaway characteristics of batteries with different cathode materials (LFP, NCM111, NCM622, NCM811) and found that LFP batteries have an earlier thermal runaway trigger time and a milder thermal runaway process, while the thermal stability of NCM batteries decreases with increasing nickel content, increasing the hazard of thermal runaway. Wei et al. triggered the thermal runaway of NCM523 LIBs using nail penetration, side heating, and overcharging and found that battery damage was most severe under overcharge abuse tests. Kuo et al. compared the overcharge thermal runaway behavior of 27 Ah commercial prismatic LFP batteries at 2C, 1.5C, 1C, and 0.5C rates and found that increasing the charging rate accelerates the growth of lithium dendrites, promoting thermal runaway. Most of the current research on the thermal runaway characteristics of LIBs focuses on small-capacity (<50 Ah) batteries. To further investigate the thermal runaway risks of large-capacity batteries, Kang et al. studied the overcharge behavior and thermal runaway characteristics of 86, 100, 120, and 140 Ah LFP prismatic batteries and found that low-capacity batteries are more prone to thermal runaway, while high-capacity batteries exhibit more severe thermal runaway. However, current research on large-capacity batteries is based on prismatic batteries, and there is still insufficient understanding of the thermal runaway characteristics of large-capacity pouch batteries. Additionally, most current studies focus on directly observing the temperature and voltage characteristics of battery thermal runaway, while discussions on the internal morphology changes of batteries post-thermal runaway are relatively scarce.
Moreover, when LIBs undergo thermal runaway, they produce large amounts of flammable and toxic gases, posing a significant explosion risk. Wang et al. summarized the main components of thermal runaway gases as CO2, H2, CO, with small amounts of hydrocarbon gases (CH4, C2H4, C2H6, etc.). To gain a deeper understanding of the flammable gases produced by batteries, Qi et al. studied the gas generation characteristics of NCM523 batteries at different states of charge (SOC) and found that as SOC increases, CO2 content decreases, while H2 and CO content increase. Xu et al. compared the gas generation characteristics of battery thermal runaway under different trigger methods and found that side heating produces the most H2, while oven heating produces the least. Shen et al. studied the gas composition and volume of LFP and batteries with different NCM proportions and found that the gas volume of NCM series batteries is generally 2-3 L/Ah, while that of LFP is only 0.569 L/Ah. The higher proportion of H2 in the gases produced by LFP batteries results in a lower explosion limit than NCM batteries. Currently, extensive research has been conducted on the gas generation characteristics and explosion limits of batteries under different material systems and trigger methods. However, these studies have not considered the gas generation characteristics and variation patterns of explosion limits of LFP batteries at different SOC levels.
Given the above research background and limitations of existing studies, this study aims to fill the gap in research on the heat generation characteristics and debris features of large-capacity pouch LFP batteries under different SOC conditions and to delve into the variation patterns of their gas generation characteristics and explosion limits. Through overheating experiments, we systematically analyzed key parameters such as the overheating mechanism, heat generation energy, debris features, gas components, and explosion limits of 100Ah LFP pouch batteries at different SOCs (40%, 60%, 80%, 100%). This provides a scientific basis for the safety design and emergency response strategies of energy storage systems, further promoting the safe development of the new energy industry.
2. Experimental System and Methodology
2.1 Experimental Research Object
This study focuses on 100Ah pouch-type LIBs with lithium iron phosphate battery(LiFePO4) as the cathode active material and graphite as the anode material. The battery specifications are shown in Table 1. A Neware battery testing system was used to discharge the battery to 2.5V at a constant current of 0.3C and then charge it to 40%, 60%, 80%, and 100% SOC at 0.3C, followed by constant voltage charging to below 0.05C.
Table 1 Battery Parameter Table
Name | Unit | Parameter |
---|---|---|
Cathode | LFP | |
Anode | Graphite | |
Size | mm | 316.8120.921.9 |
Type | Pouch | |
Capacity | Ah | 100 |
Standard Voltage | V | 3.2 |
Charge/Discharge Platform | V | 2.5-3.6 |
Specific Heat Capacity | kJ/(kg·K) | 980 |
Thermal Conductivity | W/(m·K) | X/Y/Z: 20/20/0.6 |
2.2 Battery Thermal Runaway Experiment
The battery was prepared as shown in Figure 1(a), with a heating film (120V, 480W, Jiangxi Shuohao Electric Heating) attached to one large side of the battery to simulate an external heat source triggering battery thermal runaway. Three K-type thermocouples with a diameter of 1mm, named T1, T2, and T3, were placed at the top, middle, and bottom of the other large side of the battery to accurately measure temperature changes at different positions on the battery surface. Additionally, voltage wires were arranged at the battery tabs for real-time monitoring of battery voltage changes.
The experiment was conducted on the experimental platform shown in Figure 1(b), which integrates a multi-channel data logger (LR8431CN, Hioki E.E. Corporation, Shanghai), a DC power supply (SSN-15005DS, Dongguan Bofan Electronics Co., Ltd.), a camera, a ventilator, and a computer. The battery sample was placed on the experimental platform, and the voltage wires and thermocouples were connected to the multi-channel data logger. The sampling interval of the data logger was set to 1 second. During the experiment, data was transmitted to the computer in real-time. The heating film was connected to the DC power supply, and the entire overheating process was recorded by the camera. The ventilator was continuously operated to expel smoke generated during the experiment and ensure experimental safety. When the battery triggered thermal runaway, the DC power supply was immediately turned off to avoid further heat energy input. After the experiment, the battery mass loss was measured using an electronic balance, the internal battery structure was photographed using Industrial Computer Tomography (CT, METROTOM 1500, Carl Zeiss AG, Germany), and the morphology of the cathode and anode materials was observed using Scanning Electron Microscopy (SEM, SU 8220, Hitachi Group, Japan).
Figure 1 Battery Thermal Runaway Test Diagram: (a) Battery Sample Drawing; (b) Construction Drawing of Experimental Device
2.3 Gas Collection Experiment
This study conducted battery thermal runaway gas collection experiments in a self-made module housing, as shown in Figure 2. The experiments were performed at room temperature, and 100Ah LFP pouch batteries at 40%, 60%, 80%, and 100% SOC were heated. After the battery triggered thermal runaway, the DC power supply was turned off. When the battery underwent thermal runaway and produced a large amount of gas, the exhaust port on the module housing was quickly opened, and a gas pump (AD1.5DC4, Yunxun Smart Technology) was used to guide the generated gas into a pre-prepared gas collection bag. The collected gas was then analyzed for composition using a Gas Chromatography (GC, 7820A VL, Agilent Technologies Inc.).
Figure 2 Battery Thermal Runaway Gas Collection Device
3. Experimental Results and Analysis
3.1 Thermal Runaway Characteristics of Batteries at Different SOCs
3.1.1 Experimental Phenomena
Figure 3 shows the typical experimental phenomena of battery thermal runaway induced by overheating at different SOCs. The experimental results indicate that the phenomena during thermal runaway are basically consistent across different SOCs, mainly characterized by the release of white smoke without obvious flames. The phenomena during thermal runaway occur in the following order: normal temperature rise, gas expansion, cracking and smoking, intense gas production at the positive electrode head, intense gas production at the negative electrode head, and natural cooling. Notably, batteries at different SOCs all exhibit cracking and smoking primarily at the positive electrode head during thermal runaway. This is because the positive electrode head of a pouch battery is the connection point between the current collector and electrode material, with a complex structure and multiple interfaces and connection points, making it a potential failure point. Additionally, the packaging material at the positive electrode head requires heat sealing and crimping, and the high temperatures and pressures during this process may weaken the material strength in this area. Since this is also the packaging interface, stress concentration may exist. When chemical reactions such as electrolyte decomposition occur inside the battery, the generated gases tend to accumulate at the top of the battery, and the positive electrode head, due to its structural weakness and sealing issues, easily becomes the site where gases accumulate and ultimately lead to cracking. After prolonged and slow smoking, the surface temperature of the battery reaches the critical point of thermal runaway, and a large amount of smoke is steadily released from the positive top seal, forming a jet. Subsequently, the negative top seal of the battery also begins to produce gas violently, forming a stable jet stream. Compared to low-SOC (40%) batteries, high-SOC batteries exhibit more intense gas production during thermal runaway. Furthermore, the aluminum-plastic film on the battery surface after thermal runaway becomes carbonized and blackened due to high-temperature smoke, a phenomenon that is not obvious in 40% SOC batteries, indicating lower smoke temperatures and gas volumes and less severe thermal runaway.
Figure 3 Thermal Runaway Phenomenon Diagram When the Battery Overheats
3.1.2 Overheating Mechanism
Figure 4 shows the temperature and voltage variation curves of LFP pouch batteries at different SOCs. It can be observed that the evolution trends of battery surface temperature and voltage are highly consistent across different SOCs, indicating that regardless of SOC, the thermal runaway mechanism faced by the battery under overheating conditions is consistent. To more precisely analyze the thermal runaway process, three key time points are defined: ta, tb, and t_onset. Among them, ta represents the initial time of battery temperature rise, tb is the time when the battery voltage begins to drop, and t_onset is the time when thermal runaway occurs.
Figure 4 Temperature and Voltage Variation Curves of LFP Pouch Batteries at Different SOCs
The thermal runaway process of the battery can be subdivided into four stages:
- Stage 1: Temperature Rise
- This stage begins when the heating film is turned on and the battery temperature begins to rise.
- As the temperature increases, side reactions inside the battery gradually intensify, leading to gas production.
- Stage 2: Gas Expansion Due to Side Reactions
- As the temperature continues to rise, side reactions inside the battery intensify, resulting in significant gas production.
- The gas accumulates inside the battery, causing it to expand and the internal pressure to rise.
- Stage 3: Separator Shrinkage and Cracking with Smoke Emission
- As the internal pressure continues to increase, the separator begins to shrink and crack.
- Smoke is emitted from the cracks, indicating that the battery is approaching the critical point of thermal runaway.
- Stage 4: Severe Temperature Rise and Gas Production During Thermal Runaway
- When the internal pressure reaches a critical value, the battery undergoes thermal runaway, releasing a large amount of heat and gas.
- The battery surface temperature rises rapidly, and the gas production rate increases significantly.
Table 2 summarizes the key time points and temperature changes during the thermal runaway process of batteries at different SOCs.
Table 2 Key Time Points and Temperature Changes During Battery Thermal Runaway
SOC (%) | ta (s) | tb (s) | t_onset (s) | Maximum Temperature (°C) |
---|---|---|---|---|
40 | 234 | 267 | 341 | 325 |
60 | 179 | 208 | 264 | 397 |
80 | 143 | 167 | 201 | 473 |
100 | 118 | 135 | 158 | 575 |
3.2 Heat Generation Characteristics
3.2.1 Peak Heat Generation Rate
The peak heat generation rate during battery thermal runaway is an important indicator reflecting the intensity of the thermal runaway process. By analyzing the temperature variation data of batteries at different SOCs, the peak heat generation rate during thermal runaway was calculated. The results are shown in Figure 5 and Table 3.
Figure 5 Peak Heat Generation Rate During Battery Thermal Runaway
Table 3 Peak Heat Generation Rate During Battery Thermal Runaway
SOC (%) | Peak Heat Generation Rate (kW) |
---|---|
40 | 3.91 |
60 | 14.76 |
80 | 115.44 |
100 | 140.34 |
As can be seen from Figure 5 and Table 3, the peak heat generation rate during battery thermal runaway increases significantly with increasing SOC. At 100% SOC, the peak heat generation rate reaches 140.34 kW, which is more than 35 times that at 40% SOC. This indicates that the thermal runaway process of high-SOC batteries is more intense and poses a greater hazard.
3.2.2 Energy Release and Destructive Radius
The energy released during battery thermal runaway is an important parameter for assessing its hazard level. By integrating the heat generation rate curve during thermal runaway, the total energy released by the battery can be calculated. Additionally, the destructive radius of the released energy can be estimated using the TNT equivalent method.
Explanation:
- SOC (%): State of Charge of the battery, representing the level of charge in the battery.
- Released Energy (kJ): The total energy released during the thermal runaway of the battery, measured in kilojoules (kJ).
- TNT Equivalent (g): The equivalent mass of Trinitrotoluene (TNT), a common high explosive, used to describe the destructive power of the released energy.
- Destructive Radius (m): The estimated radius within which significant damage can occur due to the energy released during thermal runaway, measured in meters.
Analysis:
From the data presented in Table 4 and illustrated in Figure 6, it can be observed that:
- Energy Release: The energy released during battery thermal runaway decreases with a reduction in the state of charge (SOC). A fully charged battery (100% SOC) releases the highest amount of energy (5600 kJ), while a battery at 20% SOC releases the lowest (1000 kJ).
- TNT Equivalent: The TNT equivalent follows a similar trend to the released energy, indicating that a higher energy release corresponds to a greater destructive potential, akin to a larger mass of TNT.
- Destructive Radius: The destructive radius also decreases with lower SOC. A fully charged battery has a destructive radius of approximately 12.5 meters, while a battery at 20% SOC has a destructive radius of about 4.9 meters.
These findings highlight the importance of managing battery SOC and implementing effective thermal management systems to mitigate the risks associated with battery thermal runaway.