Abstract
To improve the kinetic performance of lithium iron phosphate (LFP) battery systems and support the development of long-cycle batteries for energy storage applications, this paper investigates various cathode conductive agents for LFP batteries. Five schemes incorporating conductive carbon black (SP), carbon nanotubes (CNTs), graphene (GN), and binary composites of SP&CNTs and SP&GN are evaluated. The results demonstrate that composite binary conductive agents outperform single agents, with the 0.5% SP + 1.0% CNTs combination showing optimal cycling performance due to its high electronic and ionic conductivities.
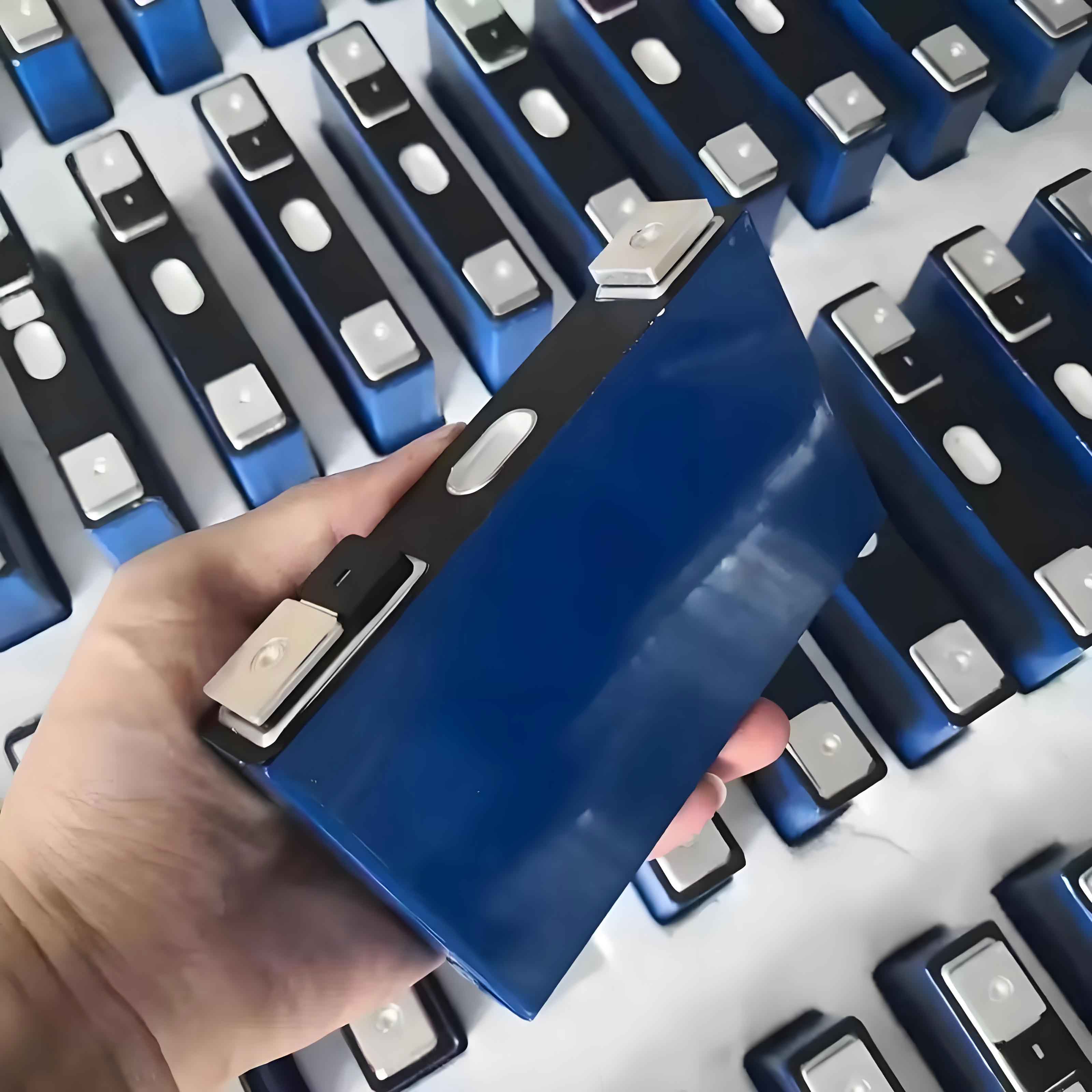
Introduction
The global push towards carbon neutrality has fueled the demand for efficient energy storage solutions. Among various energy storage technologies, electrochemical storage, particularly lithium-ion batteries (LIBs), stands out due to its high energy density, long cycle life, low self-discharge, and efficient energy conversion. Lithium iron phosphate (LFP) batteries, renowned for their safety, low cost, and environmental friendliness, dominate the emerging energy storage market. However, the inherent low electronic conductivity (10^-10 to 10^-9 S/cm) and slow ion diffusion rate (1.8 × 10^-14 cm²/s) of LFP pose challenges for high-performance applications. Conductive agents play a crucial role in addressing these limitations.
This study explores various conductive agents, including SP, CNTs, GN, and their binary combinations, to identify the optimal formulation for LFP cathodes. The study assesses the impact of these agents on battery processing, electrode thickness stability, rate capability, low-temperature performance, self-discharge, and cycling stability.
Materials and Methods
2.1 Materials
- Conductive Carbon Black (SP): SUPER P from Imerys Graphite & Carbon
- Carbon Nanotubes (CNTs): N-methyl-2-pyrrolidone (NMP) soluble product from Qingdao Haoxin New Energy Technology Co., Ltd.
- Graphene (GN): NMP soluble product from Qingdao Haoxin New Energy Technology Co., Ltd.
- Active Material: Commercial LFP powder
- Binder: Polyvinylidene fluoride (PVDF)
- Solvent: N-methyl-2-pyrrolidone (NMP)
2.2 Electrode and Battery Preparation
Five schemes were designed to evaluate different conductive agent combinations, maintaining a constant total conductive agent loading of 1.5% by weight:
- 1.5% SP
- 0.5% SP + 1.0% CNTs
- 1.5% CNTs
- 0.5% SP + 1.0% GN
- 1.5% GN
The electrodes were prepared by mixing the active material, conductive agent, and PVDF binder in an NMP solvent to form a slurry. The slurry was coated onto an aluminum foil current collector, dried, and calendared to a target thickness and density. The cathodes were paired with graphite anodes to assemble 6.0 Ah pouch cells.
2.3 Characterization and Testing
- Thickness Measurement: Electrode thickness was measured before and after roll pressing, baking at 110°C for 24 hours, and after three charge-discharge cycles.
- Electrochemical Testing:
- EIS (Electrochemical Impedance Spectroscopy): Conducted using a Bio-Logic VMP3 workstation.
- Rate Capability and Discharge Tests: Performed on a Neware 5V6A battery tester at various C-rates and temperatures.
- Self-Discharge Tests: Cells were charged to full capacity and stored at 25°C or 45°C for 30 days before reassessing capacity.
- Cycling Stability: Cells were cycled at 0.5C between 2.5V and 3.65V for up to 500 cycles.
Results and Discussion
3.1 Electrode Thickness Stability
Table 1 summarizes the electrode thickness rebound rates after baking and cycling for the five schemes.
Scheme | Thickness Rebound Rate After Baking (%) | Thickness Rebound Rate After Cycling (%) |
---|---|---|
1.5% SP | 3.2 | 4.1 |
0.5% SP + 1.0% CNTs | 3.7 | 4.6 |
1.5% CNTs | 4.0 | 5.1 |
0.5% SP + 1.0% GN | 2.9 | 3.8 |
1.5% GN | 2.5 | 3.3 |
CNTs exhibit higher flexibility and resilience, leading to a higher thickness rebound rate after baking and cycling. In contrast, GN’s layered structure facilitates compaction, resulting in a lower rebound rate.
3.2 Electrochemical Impedance Spectroscopy (EIS)
EIS results ( Table 2) reveal the influence of conductive agents on battery resistance.
Scheme | RΩ (mΩ) | Rct (mΩ) | Rion (mΩ) |
---|---|---|---|
1.5% SP | 39.9 | 8.2 | 1.2 |
0.5% SP + 1.0% CNTs | 33.7 | 8.9 | 1.5 |
1.5% CNTs | 32.0 | 9.3 | 2.5 |
0.5% SP + 1.0% GN | 28.2 | 10.1 | 2.1 |
1.5% GN | 25.7 | 10.8 | 3.4 |
CNTs and GN effectively reduce ohmic resistance (RΩ), with GN exhibiting the lowest RΩ. However, GN’s layered structure may hinder Li-ion diffusion, resulting in a higher Rion.
3.3 Rate Capability and Low-Temperature Performance
Rate capability and low-temperature discharge tests evaluate the dynamic response of batteries under varying conditions.
The 0.5% SP + 1.0% CNTs scheme displays the highest discharge voltage platform and capacity retention, especially at high C-rates and low temperatures, attributed to its balanced electronic and ionic conductivities.
3.4 Self-Discharge and Cycling Stability
Self-discharge and cycling tests assess long-term performance.
The 0.5% SP + 1.0% CNTs scheme demonstrates superior cycling stability, with a 500-cycle capacity retention of 92.4%, attributed to CNTs’ ability to stabilize the electrode structure and facilitate efficient charge transfer.
Discussion
4.1 Conductive Agent Performance
- Single Conductive Agents:
- SP: Provides good Li-ion retention but limited electronic conductivity.
- CNTs: Enhances electronic conductivity but may increase ohmic resistance due to metal impurities.
- GN: High electronic conductivity but may hinder Li-ion diffusion due to layered structure.
- Binary Composites:
- SP&CNTs: Balances electronic and ionic conductivities, reducing local ion and electron accumulations.
- SP&GN: GN improves electronic conductivity, but GN’s structure complicates Li-ion diffusion.
4.2 Impact on Battery Performance
- Thickness Stability: CNTs’ resilience leads to higher thickness rebound, while GN’s layered structure aids compaction.
- EIS: CNTs and GN effectively reduce ohmic resistance, but GN increases Li-ion resistance.
- Rate Capability and Low-Temperature Performance: Balanced conductivities in the 0.5% SP + 1.0% CNTs scheme enhance performance across conditions.
- Self-Discharge and Cycling: CNTs stabilize the electrode structure, reducing capacity fade during cycling.
Conclusion
This study comprehensively evaluated various conductive agents for LFP battery cathodes. The 0.5% SP + 1.0% CNTs combination emerged as the optimal formulation, exhibiting superior rate capability, low-temperature performance, and cycling stability. The balanced electronic and ionic conductivities of this binary composite effectively mitigate capacity fade and polarization, making it well-suited for high-performance LFP batteries in energy storage applications.