Abstract
Lithium iron phosphate battery (LFP battery) have gained widespread adoption in electric vehicles (EVs) and energy storage systems due to their excellent cycling stability, high safety, and low cost. The continuous increase in their market presence has intensified the focus on recycling used LFP battery. However, challenges persist in the high-value recovery of LFP battery owing to their modest inherent value and technical barriers associated with comprehensive recycling methods. This comprehensive review summarizes the retirement and regeneration pathways of LFP battery, delves into the research progress in the pretreatment and resource recovery of LFP cathode waste, and identifies critical factors for industrializing the recycling of LFP cathode waste. Direct regeneration, which exhibits greater application potential, is still in its initial research phase, while indirect regeneration is suitable for materials with complex compositions or requiring high-value resource reserves. Furthermore, this paper outlines the development trends, challenges, and recommendations for the recycling of LFP battery, aiming to streamline the innovation pathway from fundamental research to industrialization and foster green development in related industries.
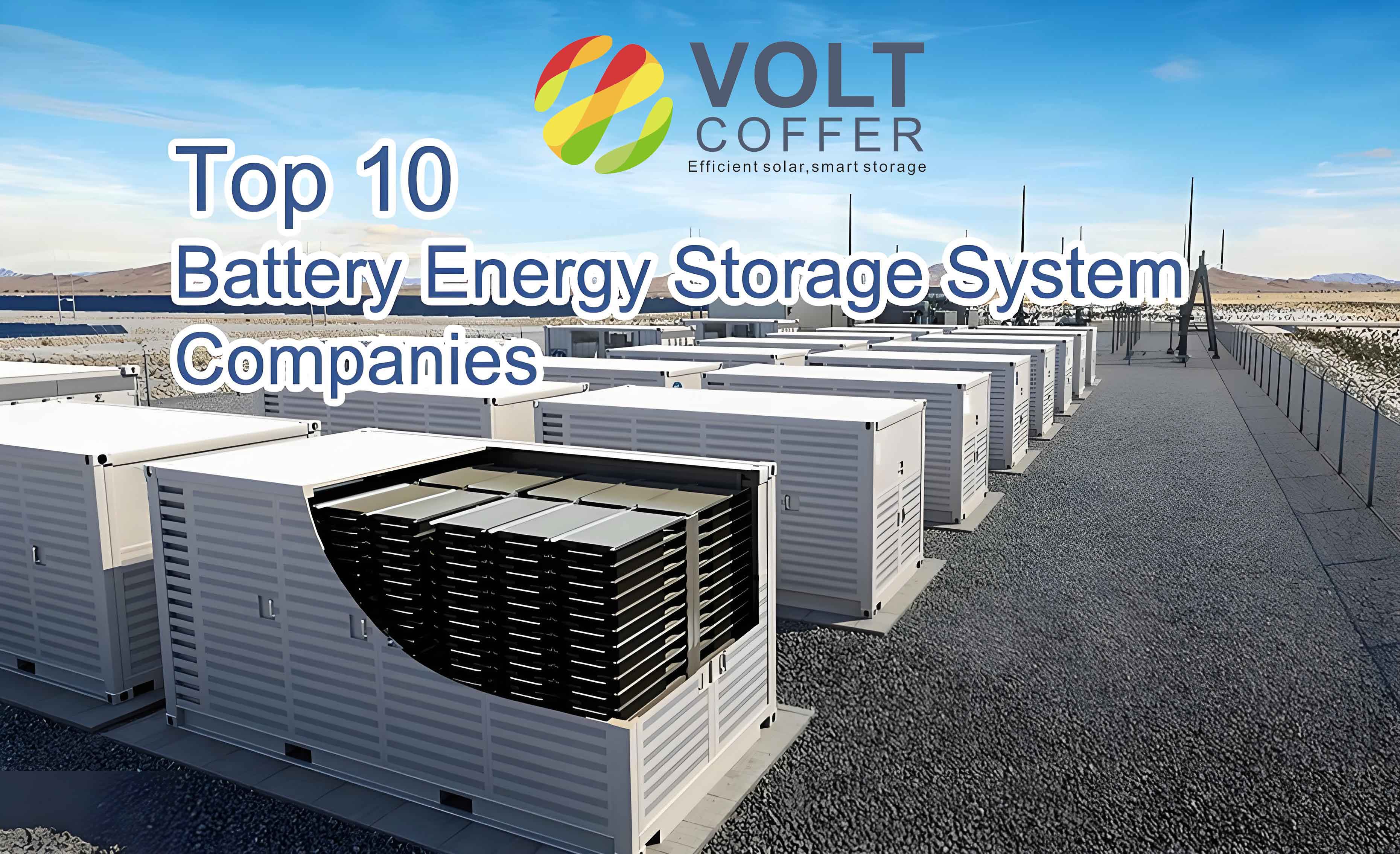
1. Introduction
The global transition towards electric mobility and renewable energy storage has spurred a surge in the demand for lithium-ion batteries (LIBs). Among various LIB chemistries, lithium iron phosphate (LiFePO4 or LFP) batteries stand out due to their stability, safety, and cost-effectiveness. However, with the impending retirement of the first wave of LFP battery installed a decade ago, recycling these batteries has become imperative to mitigate environmental pollution and conserve critical raw materials.
This paper aims to provide a comprehensive overview of LFP battery recycling, encompassing fundamental research, technological advancements, and industrialization prospects. By analyzing the retirement and regeneration pathways, pretreatment and resource recovery techniques, and key factors for industrialization, this review offers insights into the current state and future directions of LFP battery recycling.
2. Retirement Pathways of LFP Battery
LFP battery typically have a service life of 5-8 years. Once they reach the end of their designed lifespan, they can either undergo second-life applications or be recycled for raw material recovery .
2.1 Second-life Applications
Second-life applications involve redeploying retired LFP battery with residual capacity (typically 20%-40% of their original capacity) in less demanding applications such as stationary energy storage, backup power, and grid support services. This approach extends battery life, delays final disposal, and reduces waste generation.
2.2 Recycling for Raw Material Recovery
Batteries with capacities below 20% are recycled to extract valuable metals like lithium, iron, and phosphorus. The recycling process involves pretreatment (discharge, disassembly, shredding, and separation) followed by resource recovery techniques.
3. Pretreatment of LFP Battery Waste
Pretreatment is crucial for efficient and safe resource recovery from retired LFP battery. It involves three primary methods: heat treatment, mechanical processing, and chemical treatment.
3.1 Heat Treatment
Heat treatment decomposes organic binders (e.g., polyvinylidene fluoride, PVDF) and weakens adhesive forces between cathode materials and current collectors. However, high temperatures can degrade LFP, necessitating protective atmospheres to maintain material integrity.
Table 1: Comparison of Heat Treatment Methods for LFP Battery Pretreatment
Method | Temperature Range (°C) | Atmosphere | Advantages | Disadvantages |
---|---|---|---|---|
Conventional Heat | 300-600 | Inert/Reducing Gas | Efficient removal of organic binders | Risk of LFP degradation |
Low-Temperature | 200-300 | Inert Gas | Reduced energy consumption, shorter duration | May not fully decompose organic binders |
Coupled Heat-Mech. | 250-350 | Inert Gas | Enhanced efficiency, shorter treatment time | Complex equipment requirements |
3.2 Mechanical Processing
Mechanical processing, including shredding, grinding, and sieving, physically separates battery components. While effective in size reduction, it may lead to material loss and incomplete impurity removal.
3.3 Chemical Treatment
Chemical treatment utilizes solvents or alkalis to dissolve organic binders, enabling cleaner separation of cathode materials from current collectors.
4. Resource Recovery Techniques
Resource recovery from pretreated LFP cathode waste can be achieved through direct regeneration or indirect regeneration techniques.
4.1 Direct Regeneration
- Solid phase remediation method: By high-temperature calcination of mixed lithium source and LFP waste, the lost lithium is replenished.
- Liquid phase repair method: repair LFP materials at lower temperatures using liquid lithium sources and reducing agents.
- Electrochemical repair method: Using electrical energy to drive lithium ions to embed into LFP materials, achieving component repair.
Table 2: Comparison of Direct Regeneration Techniques
Technique | Mechanism | Advantages | Disadvantages |
---|---|---|---|
Solid-phase | High-temperature calcination | Simple process, suitable for industrial scale | High energy consumption, risk of material degradation |
Liquid-phase | Chemical reduction at lower temp. | Efficient at lower temperatures, less energy consumption | Complex process control, potential for contamination |
Electrochemical | Electrically driven lithiation | Energy-efficient, minimal chemical consumption | Complex setup, limited scalability |
4.2 Indirect Regeneration
Indirect regeneration involves extracting valuable metals from LFP cathode waste and resynthesizing new cathode materials. Key steps include leaching, separation, and precipitation.
- Leaching: Utilizes acids or bases to dissolve LFP, releasing lithium, iron, and phosphorus.
- Separation: Purifies leachate to isolate metals for subsequent recovery.
- Precipitation: Recovers metals as compounds (e.g., Li2CO3, FePO4) for reuse.
Table 3: Comparison of Key Steps in Indirect Regeneration
Step | Process | Advantages | Disadvantages |
---|---|---|---|
Leaching | Acid/Base dissolution of LFP | High metal recovery rates | Complex wastewater treatment required |
Separation | Solvent extraction, ion exchange | Purifies metals for efficient recovery | Additional equipment and process steps |
Precipitation | Formation of metal compounds | Recovers metals in reusable forms | Potential for impurities in recovered products |
5. Industrialization of LFP Battery Recycling
Industrializing LFP battery recycling necessitates addressing safety, economics, and technical challenges. Key factors for successful industrialization include:
5.1 Safety
Ensuring safe handling and processing of toxic and flammable battery components is crucial. Compliance with strict safety regulations and the use of protective equipment minimize risks.
5.2 Economics
Economics drive the viability of recycling operations. Cost-effective processes, high recovery rates, and market demand for recovered materials are essential.
Table 4: Key Economic Factors in LFP Battery Recycling
Factor | Impact |
---|---|
Recovery Rates | Higher rates reduce material waste and costs |
Process Efficiency | Lowers energy and chemical consumption |
Market Demand | Drives investment and scales production |
Waste Management | Costly if not properly managed |
5.3 Technical Maturity
Well-established processes with high technical maturity facilitate industrialization. Ongoing research focuses on optimizing existing technologies and developing novel approaches.
6. Case Study: Short-range Recycling of LFP Cathode Waste
A case study on the short-range recycling of LFP cathode waste highlights the IPE-BRUNP technology developed by the research team. This technology involves selective separation of Li and FePO4, efficient metal recovery, and production of battery-grade Li2CO3 and FePO4.
The technology has been successfully commercialized in a 10,000-tonne/year recycling plant, demonstrating economic viability and environmental benefits.
7. Development Trends and Challenges
7.1 Development Trends
- Advanced Detection and Monitoring: Integrating AI, IoT, and machine learning enhances battery state estimation, facilitating efficient second-life applications and targeted recycling.
- Automated and Intelligent Disassembly: Smart technologies streamline battery disassembly, improving safety, efficiency, and recovery rates.
- Efficient Direct Regeneration: Innovations in direct regeneration promise lower energy consumption and higher process simplicity, driving industrial adoption.
7.2 Challenges
- Complex Feedstocks: Diverse battery designs and compositions complicate recycling processes, necessitating adaptable technologies.
- Metal Impurities: Efficient removal of impurities is critical but technically challenging, requiring complex processes.
- Rapid Technological Advancement: Fast-paced developments in cathode materials pose new recycling challenges.
8. Recommendations
- Standardize and Regulate: Develop comprehensive regulations and standards to ensure safe and efficient battery recycling.
- Foster Collaboration: Encourage collaboration among researchers, industry, and policymakers to accelerate technology development and adoption.
- Invest in Infrastructure: Build recycling infrastructure to support the growing demand for battery recycling services.
- Promote Awareness: Raise public awareness of the importance of battery recycling through education and outreach programs.
Conclusion
LFP battery recycling is crucial for sustainable energy storage solutions. Direct and indirect regeneration techniques offer varying degrees of applicability and efficiency, with direct regeneration showing greater potential for industrialization. Overcoming technical, economic, and safety challenges through research, collaboration, and infrastructure development will pave the way for a circular economy in LIB recycling.