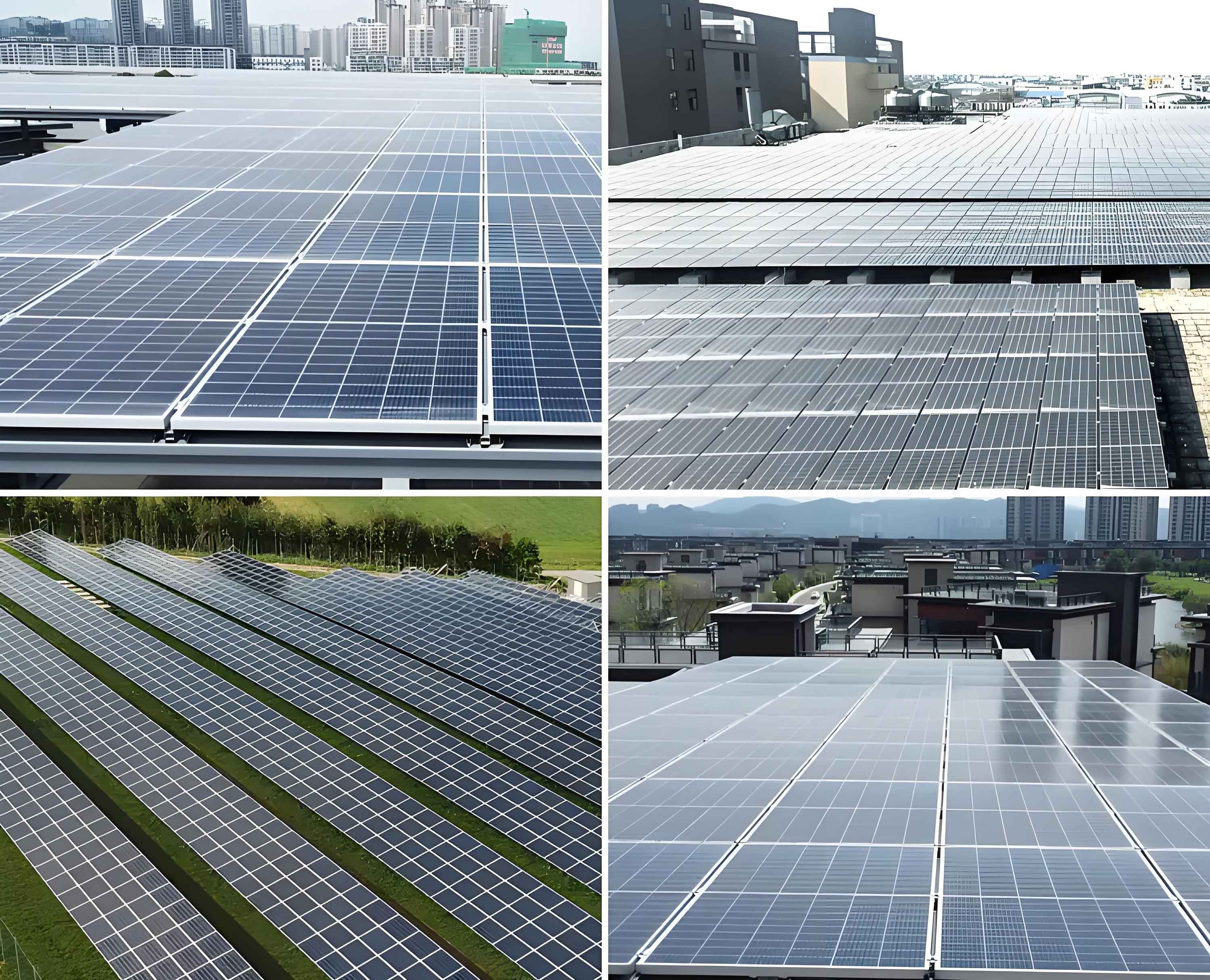
1. Introduction
Solar energy is a clean and renewable energy source, and solar panel play a crucial role in converting solar energy into electricity. However, with the large-scale installation and long-term use of solar panel, a large number of waste solar panel will be generated in the future. The recycling of waste solar panel is of great significance for resource conservation and environmental protection. This article focuses on the recycling of waste crystalline silicon solar panel using the DMPU coupled pyrolysis method.
1.1 Background of Solar Panel Recycling
The rapid development of the photovoltaic industry has led to an increasing number of installed solar panel. As these solar panel reach the end of their useful lives, proper recycling becomes essential. In China, for example, it is expected to usher in a peak period of photovoltaic module retirement around 2030, with a large amount of recyclable materials and potential economic benefits. The main components of a solar panel include the aluminum frame, glass, EVA (ethylene-vinyl acetate), and silicon cells. Among them, the silicon cells are of high value and it is crucial to recycle them intact for economic and environmental reasons.
1.2 Existing Recycling Methods and Their Limitations
- Thermal decomposition method: This method utilizes the property that EVA softens and decomposes at high temperatures. For example, Zhang et al. conducted pyrolysis of EVA in a tube furnace under certain conditions, achieving a high mass loss rate of EVA. However, it has problems such as easy fragmentation of silicon cells and residual organic matter on the cell surface.
- Mechanical disassembly method: By using mechanical equipment to break the solar panel, different layers can be separated. Azeumo et al. used sodium polytungstate for metal sorting. Although this method has a relatively low cost and can handle large quantities of components, it produces fine powder with complex components that are difficult to separate, resulting in a decline in economic benefits and causing environmental pollution such as dust and noise.
- Chemical dissolution method: Through physical or chemical reactions during solvent immersion, EVA can be removed or metal on the cell surface can be etched. Pagnanelli et al. used cyclohexane to remove the encapsulant. Traditional chemical reagents like toluene and trichloroethylene can separate photovoltaic components but are harmful to humans and the environment.
2. DMPU Coupled Pyrolysis Method
2.1 Principle of DMPU Coupled Pyrolysis
DMPU (N,N – dimethylpropenylurea) is a novel green solvent with strong solubility and stability, and low toxicity and carcinogenicity. In the recycling process, DMPU is first used to pretreat the solar panel. It causes the EVA to swell, allowing the gases generated during EVA decomposition to be discharged laterally, preventing the silicon cells from being damaged due to excessive longitudinal pressure. Then, the pyrolysis method is used to completely decompose the remaining EVA, separating the components of the solar panel.
2.2 Experimental Materials and Equipment
- Materials: Artificialally cut solar panel with a mass of 3.5 – 7g and an area of 4 – 9cm² were used. The solar panel was provided by Hunan Frontier Technology Co., Ltd. DMPU reagent was from MACKLIN.
- Equipment: A thermostatic magnetic stirrer (DF – 101S, Qiuzuo Technology) was used for heating DMPU, and dimethyl silicone oil (XIAMETER – 200, Dow Corning) was used as a heat transfer medium. A high – temperature reaction furnace (KF1200, Nanjing Boyuntong) was used for pyrolysis, and a Fourier transform infrared spectrometer (Vertex 70) was used for analysis.
2.3 Experimental Methods
- DMPU pretreatment: A certain amount of DMPU was weighed and placed in a beaker, preheated in an oil bath. After reaching the specified temperature, the solar panel was added. After a certain heating time, the panel was taken out, photographed, and washed with anhydrous ethanol.
- Pyrolysis process: The DMPU – treated solar panel was placed in a crucible and put into a high – temperature reaction furnace. The temperature and holding time were set, and after pyrolysis, the crucible was taken out and cooled to room temperature. The integrity of the silicon cells was photographed and recorded.
3. Results and Discussion
3.1 Influence of DMPU Pretreatment Conditions on Silicon Cell Integrity Rate and Backplate Removal Rate
- Influence on silicon cell integrity rate: Different DMPU treatment temperatures (160℃, 170℃, 180℃, 200℃) and treatment times (30min, 40min, 50min, 60min) were set. The results showed that when the solar panel was treated in DMPU at 200℃ and then pyrolyzed, the integrity rate of the silicon cells was the highest. At 200℃, the integrity rate of the silicon cells increased with the increase of the pretreatment time, reaching a maximum of 98%. When the treatment temperature was 170℃, the integrity rate was the lowest, with an average value of only 46%.
DMPU Treatment Temperature (℃) | Silicon Cell Integrity Rate (%) |
160 | – (severe fragmentation, not calculated) |
170 | 46 |
180 | 73 |
200 | 98 |
- Influence on backplate removal rate: The backplate used in the experiment was TPT material. The results showed that in the temperature range of 170 – 200℃, the backplate removal rate increased with the increase of temperature. At 200℃, the backplate removal rate reached 100% after 30min of treatment, which was the shortest time to completely remove the backplate.
DMPU Treatment Temperature (℃) | Backplate Removal Rate (%) |
170 | 26 (fluctuates, worst case) |
180 | 98 (after 40min, reaches 100%) |
200 | 100 (after 30min) |
3.2 Influence of Pyrolysis Conditions on Silicon Cell Integrity Rate
Different pyrolysis temperatures (450℃, 480℃, 510℃, 540℃) and pyrolysis times (45min, 60min, 75min, 90min) were set. When the temperature was 450℃, due to insufficient temperature and time, the layers of the solar panel could not be separated, and the integrity rate of the silicon cells was poor. At 480℃, the components could be separated, and the integrity rate first increased and then decreased. At 510℃ and 540℃, the average integrity rate was low. The optimal pyrolysis temperature was 480℃, and the optimal pyrolysis time was 60min, at which point the integrity rate of the silicon cells was the highest, reaching 97%.
Pyrolysis Temperature (℃) | Silicon Cell Integrity Rate (%) |
---|---|
450 | Poor |
480 | 97 (highest at 60min) |
510 | Low average |
540 | Low average |
3.3 Verification of the Feasibility of DMPU Cycle Coupled Pyrolysis Method
The integrity rate of silicon cells obtained by direct pyrolysis without DMPU treatment was compared with that obtained by DMPU pretreatment coupled with pyrolysis. The integrity rate of silicon cells obtained by direct pyrolysis was only 30.75%, while that obtained by DMPU pretreatment coupled with pyrolysis was at least 42% and could reach 97.52%, which was much higher than the blank control group. In addition, FTIR tests were carried out on DMPU used in 0 – 5 cycles, and the results showed that the characteristic bands and peak values in the absorption spectra of DMPU with different cycle numbers remained basically unchanged, indicating that DMPU can be recycled.
4. Energy Consumption and Carbon Emission Analysis
The energy consumption and carbon emission analysis of the practical application of DMPU coupled pyrolysis for the recovery of waste crystalline silicon solar panel was carried out. The results showed that compared with existing recycling methods, this method had significant energy – saving and emission reduction benefits. The specific data and comparison with other methods can be presented in a table for better visualization.
5. Conclusion
- DMPU is a novel green solvent with excellent properties for recycling waste crystalline silicon solar panel.
- The optimal recycling conditions for DMPU coupled pyrolysis are 200℃, 60min DMPU treatment followed by 480℃, 60min pyrolysis. Under these conditions, the integrity rate of silicon cells is the highest, and the backplate can be completely removed.
- The DMPU coupled pyrolysis method has significant advantages in terms of resource recovery, environmental protection, and energy conservation, providing a new and effective way for the recycling of waste solar panel.
In conclusion, the research on DMPU coupled pyrolysis for recycling waste crystalline silicon solar panel has important theoretical and practical significance, and it is expected to promote the development of the solar panel recycling industry.