The manufacturing of solar batteries involves meticulous processes to ensure high-quality products that meet the stringent demands of the renewable energy market. Quality control and testing standards are pivotal in achieving reliable, efficient, and long-lasting solar batteries. This article delves into the various quality control measures and testing standards employed in the manufacturing of solar batteries.
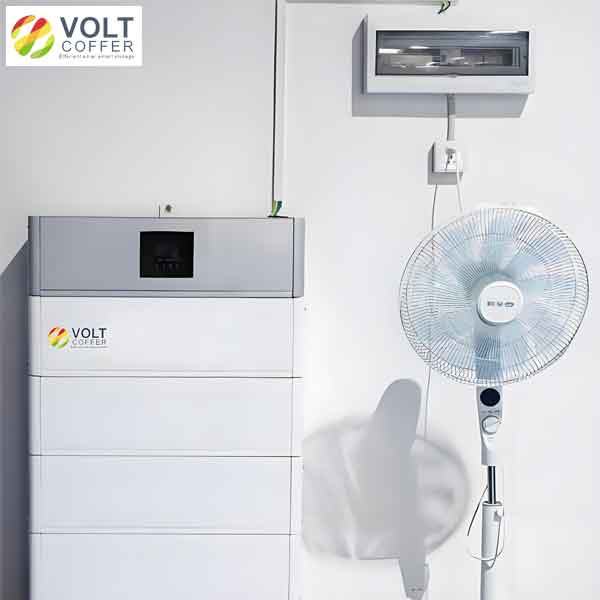
Introduction to Solar Battery Quality Control
Quality control in solar battery manufacturing is a comprehensive approach encompassing various stages, from raw material inspection to the final product evaluation. It aims to identify and mitigate defects, ensuring that every solar battery produced meets the specified performance criteria.
Raw Material Inspection
The quality of raw materials used in solar battery manufacturing directly impacts the final product’s performance. Key materials include lithium, cobalt, nickel, and other conductive materials. Inspection of these materials involves:
- Purity Assessment: Ensuring the raw materials meet the required purity levels.
- Consistency Check: Verifying the uniformity of materials across different batches.
- Supplier Evaluation: Assessing and approving suppliers based on their ability to provide high-quality materials consistently.
Table 1: Common Raw Materials and Their Quality Control Measures
Material | Quality Control Measure | Description |
---|---|---|
Lithium | Purity Testing | Ensuring high purity levels |
Cobalt | Consistency Check | Uniformity in chemical composition |
Nickel | Supplier Evaluation | Approval of reliable suppliers |
Conductive Materials | Electrical Conductivity Testing | Ensuring optimal conductivity |
Manufacturing Process Control
During the manufacturing process, various control measures are implemented to maintain high quality. These include:
- Process Standardization: Establishing standard operating procedures (SOPs) for each manufacturing step.
- In-Process Monitoring: Continuous monitoring of critical parameters such as temperature, pressure, and humidity.
- Defect Detection Systems: Utilizing automated systems to detect defects in real-time.
Testing Standards for Solar Batteries
Testing standards for solar batteries are crucial in determining their performance, safety, and longevity. These standards are set by international organizations such as the International Electrotechnical Commission (IEC) and the Institute of Electrical and Electronics Engineers (IEEE).
Performance Testing
Performance testing evaluates the efficiency, capacity, and overall functionality of solar batteries. Key performance tests include:
- Capacity Test: Measuring the battery’s ability to store and deliver electrical energy.
- Efficiency Test: Assessing the energy conversion efficiency of the battery.
- Cycle Life Test: Determining the number of charge-discharge cycles the battery can endure before significant degradation.
Table 2: Common Performance Tests and Their Objectives
Test Type | Objective |
---|---|
Capacity Test | Measure energy storage and delivery capability |
Efficiency Test | Assess energy conversion efficiency |
Cycle Life Test | Determine longevity through charge-discharge cycles |
Safety Testing
Safety testing is paramount to ensure that solar batteries operate without posing hazards to users or the environment. Common safety tests include:
- Thermal Stability Test: Evaluating the battery’s behavior under extreme temperature conditions.
- Short Circuit Test: Ensuring the battery can withstand short circuit conditions without catastrophic failure.
- Overcharge Test: Testing the battery’s response to overcharging scenarios.
Environmental Testing
Environmental testing assesses the solar battery’s performance under various environmental conditions, including:
- Temperature Cycling: Testing the battery’s resilience to temperature fluctuations.
- Humidity Exposure: Evaluating the battery’s performance in high humidity environments.
- Vibration Test: Ensuring the battery can withstand mechanical vibrations.
Quality Assurance Protocols
Quality assurance in solar battery manufacturing involves a systematic approach to ensure that all products meet the required standards. Key protocols include:
- Quality Audits: Regular audits of the manufacturing process to identify and address potential issues.
- Customer Feedback Integration: Using customer feedback to improve product quality continuously.
- Certification and Compliance: Ensuring products meet international standards and obtaining necessary certifications.
Conclusion
Quality control and testing standards are integral to the manufacturing of high-performance and reliable solar batteries. By implementing rigorous inspection processes, standardizing manufacturing procedures, and adhering to international testing standards, manufacturers can ensure that their solar batteries meet the demands of the renewable energy market. The continuous improvement of these processes is essential for the advancement of solar battery technology and the broader adoption of renewable energy solutions.