Abstract
This article delves into the mechanism of lithium recovery from spent lithium iron battery (LiFePO4 battery) through mechanochemical solid-phase oxidation. Three distinct methods—oxidation leaching, mechanical activation combined with oxidation leaching, and mechanical solid-phase oxidation followed by water leaching—are evaluated and compared. The optimal conditions for each method are established, with a focus on the efficiency and selectivity of lithium extraction. The results reveal that the mechanical solid-phase oxidation method achieves the highest lithium leaching rate of 98.26% (wt. %), outperforming the other two approaches. The recovered lithium is precipitated as high-purity Li3PO4, while the remaining filter residue comprises FePO4 suitable for recycling. The reaction mechanism is elucidated through X-ray diffraction (XRD) and X-ray photoelectron spectroscopy (XPS) analyses, highlighting the role of mechanical force in facilitating the oxidation and lithium release processes.
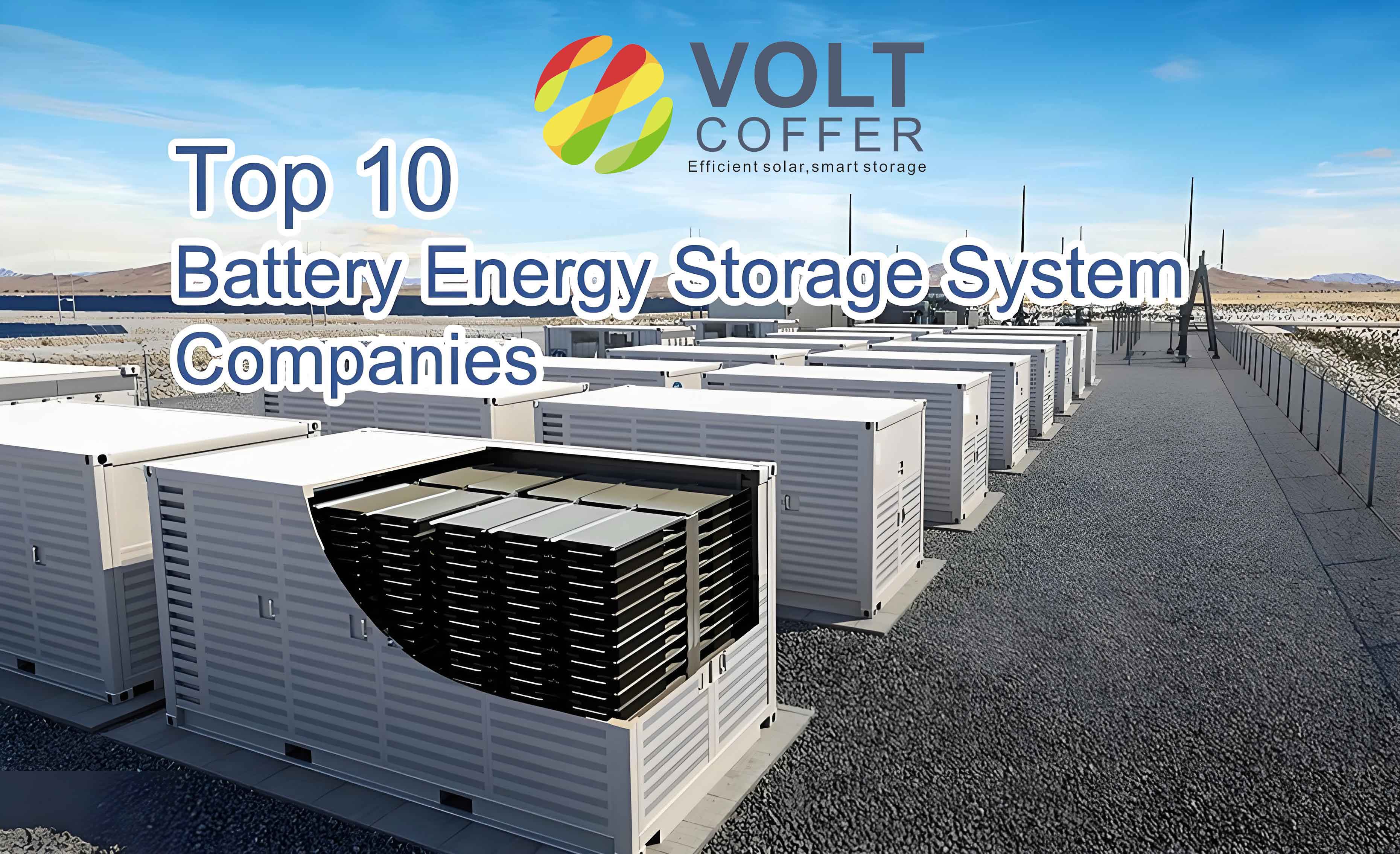
Introduction
lithium iron battery (LiFePO4 battery) have gained significant attention in recent years due to their high energy density, long cycle life, and excellent safety profile. As a result, they are widely used in electric vehicles (EVs) and stationary energy storage systems. However, the rapid growth in lithium iron battery (LiFePO4 battery) usage has led to a surge in the generation of spent batteries, posing environmental and economic challenges. Recycling these batteries is essential to mitigate the potential environmental hazards associated with heavy metals and toxic electrolytes, while also recovering valuable materials such as lithium, iron, and phosphorus.
Currently, two primary methods are employed for recycling spent lithium iron battery (LiFePO4 battery): direct regeneration and hydrometallurgical processes. Direct regeneration, while straightforward, often yields materials with inferior performance. Direct regeneration, while straightforward, often yields materials with inferior performance due to structural degradation during cycling. Conversely, hydrometallurgical methods, which involve chemical leaching and precipitation, are more effective. Conversely, hydrometallurgical methods, which involve chemical leaching and precipitation, are more effective in recovering high-purity metals but can consume significant amounts of chemicals and generate secondary pollutants.
To address these issues, mechanochemical solid-phase oxidation emerges as a promising alternative. This technique harnesses the energy of mechanical forces to induce chemical reactions, allowing for metal recovery under ambient conditions with minimal chemical consumption. This article comprehensively examines the mechanochemical solid-phase oxidation of spent lithium iron battery (LiFePO4 battery),. This article comprehensively examines the mechanochemical solid-phase oxidation of spent lithium iron battery (LiFePO4 battery), emphasizing the reaction mechanism and optimization of processing parameters.
Materials and Methods
1. Experimental Materials
Spent lithium iron battery (LiFePO4 battery) cathode powder was obtained from Qingdao Beichen Advanced Recycling Technology Co., Ltd. The powder was pre-processed to remove impurities and analyzed for its elemental composition using inductively coupled plasma mass spectrometry (ICP-MS). The main reagents used in this study were potassium persulfate (K2S2O8), potassium phosphate (K3PO4), nitric acid (HNO3), hydrofluoric acid (HF), and hydrogen peroxide (H2O2), all of which were of analytical grade and purchased from Aladdin Reagent Co., Ltd.
2. Pretreatment and Leaching Experiments
Three different treatment methods were evaluated:
- Oxidation Leaching: The cathode powder was mixed with K2S2O8 and agitated in deionized water at room temperature.
- Mechanical Activation Combined with Oxidation Leaching: The cathode powder was ball-milled with K2S2O8 before agitation in deionized water.
- Mechanical Solid-Phase Oxidation Followed by Water Leaching: The cathode powder was co-milled with K2S2O8 under mechanical activation conditions, followed by agitation in deionized water.
The leachates were filtered, and the filter residues were washed and dried at 50°C. The lithium and iron content in the filtrates was determined using ICP-MS. The recovered lithium was precipitated as Li3PO4 by adding K3PO4, and its purity was verified through acid digestion and ICP-MS analysis.
3. Mechanochemical Solid-Phase Oxidation Experiments
The cathode powder was mixed with varying amounts of K2S2O8 and ball-milled for different durations. The ball-milled samples were then leached in deionized water at room temperature. The effects of K2S2O8/LiFePO4 mass ratio and ball-milling time on lithium leaching efficiency were systematically investigated.
4. Characterization Methods
- ICP-MS: Used to determine the elemental composition of the cathode powder and filtrates.
- XRD: Employed to analyze the phase composition of the ball-milled samples and filter residues.
- XPS: Applied to study changes in the oxidation state of iron during the mechanochemical process.
- SEM: Utilized to observe the morphology of the precipitated Li3PO4 particles.
- Particle Size Analyzer: Used to measure the particle size distribution of the cathode powder before and after ball milling.
Results and Discussion
1. Lithium Extraction Efficiency
Table 1: Lithium Leaching Rates for Different Treatment Methods
Treatment Method | Lithium Leaching Rate (%) |
---|---|
Oxidation Leaching | 89.03 ± 1.25 |
Mechanical Activation + Oxidation Leaching | 92.36 ± 0.98 |
Mechanical Solid-Phase Oxidation + Water Leaching | 98.26 ± 0.67 |
As shown in Table 1, the mechanical solid-phase oxidation followed by water leaching method demonstrated the highest lithium leaching rate of 98.26% (wt. %), significantly outperforming the other two methods. This suggests that the combined effect of mechanical activation and solid-phase oxidation during ball milling significantly enhanced the lithium release process.
2. Effect of Processing Parameters
The influence of the K2S2O8/LiFePO4 mass ratio on the lithium leaching rate. An optimal mass ratio of 1.75/1 was identified, beyond which further increases in K2S2O8 did not significantly improve the leaching efficiency.
The effect of ball-milling time on lithium leaching. A maximum leaching rate of 98.26% was achieved after 20 minutes of milling, with minimal gains observed beyond this point.
3. Characterization of Products
The XRD patterns in Figure 3 confirm the high purity of the FePO4 filter residue (92.74% wt.) and Li3PO4 precipitate (98.67% wt.). The well-defined diffraction peaks indicate the preservation of the橄榄石-type structure in FePO4 and the high crystallinity of Li3PO4.
The SEM image in Figure 4 reveals the agglomerated, spherical morphology of the Li3PO4 precipitate with a rough surface, indicative of good particle dispersion and crystallinity.
4. Reaction Mechanism
Based on XRD and XPS analyses, the proposed reaction mechanism is outlined in Figure 5. During ball milling, mechanical forces induce a solid-phase oxidation reaction between K2S2O8 and LiFePO4. This reaction results in the release of Li+ ions and the oxidation of Fe2+ to Fe3+, forming LiKSO4 and FePO4, respectively. Subsequent water leaching efficiently extracts the released Li+ ions, which are then precipitated as Li3PO4.
The mechanical force acts as a driving force for the oxidation reaction, enabling the replacement of electrical force in the conventional charging process of lithium iron battery (LiFePO4 battery). This novel approach significantly enhances lithium extraction efficiency and selectivity.
Conclusion
This study comprehensively evaluates the mechanochemical solid-phase oxidation method for recovering lithium from spent lithium iron battery (LiFePO4 battery). The optimal conditions for maximum lithium extraction (98.26% wt.) were identified, with high selectivity and minimal chemical consumption. Characterization analyses confirmed the high purity of the recovered Li3PO4 and FePO4 products, suitable for reuse in battery manufacturing.
The proposed mechanism highlights the crucial role of mechanical force in facilitating the solid-phase oxidation and lithium release processes. This environmentally friendly and cost-effective approach offers significant potential for large-scale recycling of spent lithium iron battery (LiFePO4 battery), contributing to sustainable resource utilization and circular economy practices.