Abstract
This comprehensive article delves into the current state of Lithium Iron Phosphate battery (LFP battery) technology, focusing on its production processes, market trends, industry challenges, and future directions. LFP battery have emerged as a dominant force in the electric vehicle and energy storage sectors due to their inherent safety, long cycle life, and cost-effectiveness. This study examines the various production methods, market dynamics, and strategic recommendations to navigate the evolving landscape of LFP battery technology.
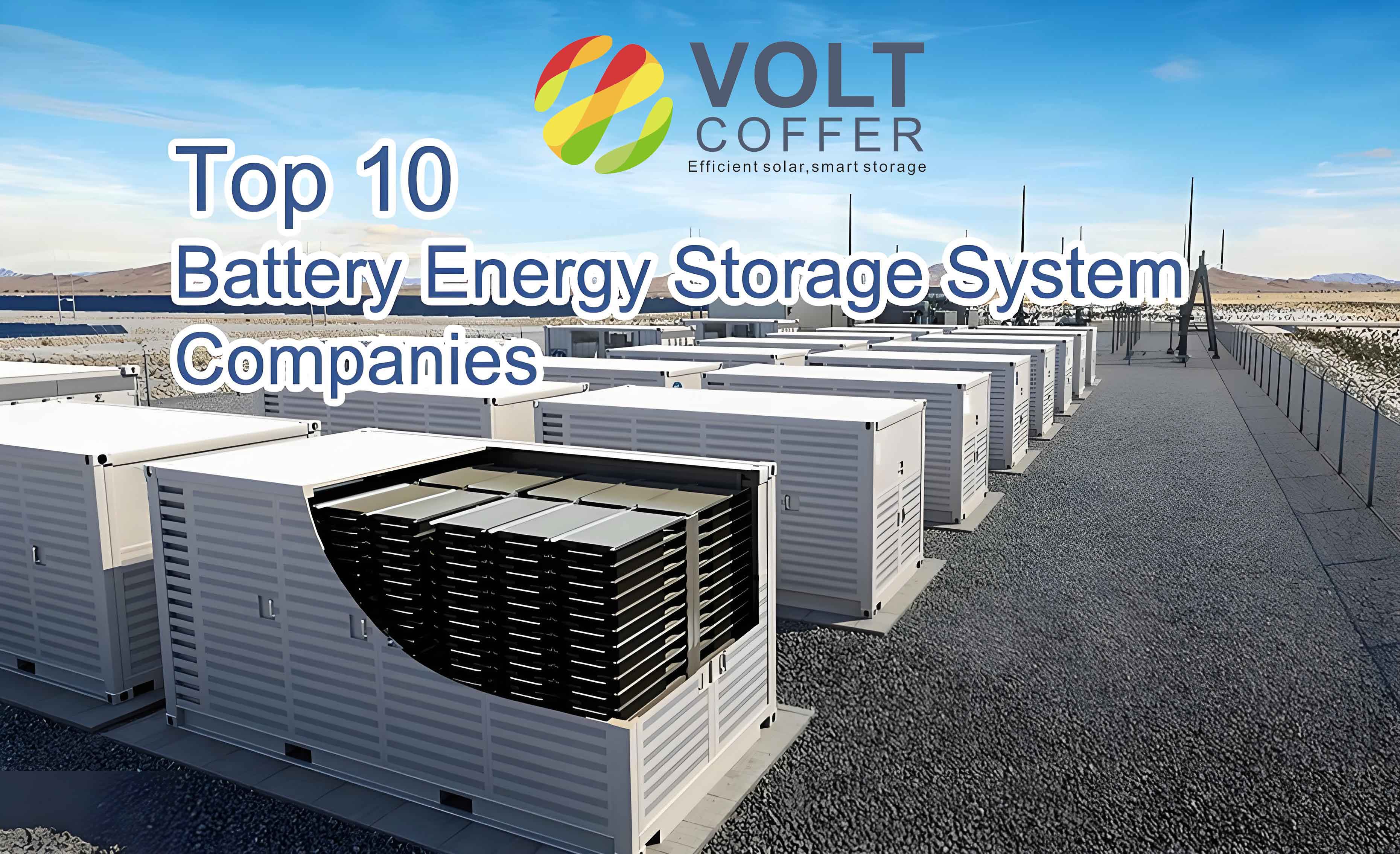
1. Introduction
The transition towards a greener, low-carbon future has significantly accelerated the demand for energy storage solutions, particularly Lithium Iron Phosphate (LFP) batteries. These batteries have gained widespread popularity due to their inherent advantages over other lithium-ion battery chemistries, including improved safety, lower cost, and excellent cycle stability. This section introduces the key concepts surrounding LFP battery technology and outlines the structure of the article.
1.1 Overview of Lithium Iron Phosphate Batteries
Lithium Iron Phosphate battery (LFP battery) belong to the family of lithium-ion batteries, utilizing an olivine-structured cathode material. Introduced in 1996 by Goodenough et al. (Goodenough et al., 1997), LFP battery have gained significant traction due to their high thermal stability, long cycle life, and environmental friendliness.
1.2 Structure of the Article
This article is structured as follows:
- Section 2: Production Processes of LFP Battery outlines the primary methods used to produce LFP cathode materials, including solid-state and liquid-phase synthesis routes.
- Section 3: Market Dynamics and Trends analyzes the current market status, growth drivers, and forecasts for LFP battery.
- Section 4: Challenges Facing the LFP Battery Industry identifies the key challenges, including raw material supply, trade barriers, and technological advancements.
- Section 5: Strategic Recommendations provides recommendations for navigating the evolving LFP battery landscape, including supply chain management, international expansion, and research and development priorities.
- Section 6: Conclusion summarizes the key findings and highlights future directions for LFP battery technology.
2. Production Processes of LFP Battery
The production of LFP battery cathode materials involves various synthesis methods, each with its unique advantages and disadvantages. The two primary categories are solid-state and liquid-phase synthesis routes.
2.1 Solid-State Synthesis
Solid-state synthesis is the most established and widely used method for LFP battery production. It involves mixing iron, phosphorus, and lithium precursors, followed by high-temperature sintering to form the final product. This method is cost-effective and suitable for large-scale production, but it may result in inhomogeneous particle distributions and poor electrochemical performance (Wang et al., 2018).
Table 1: Advantages and Disadvantages of Solid-State Synthesis
Advantages | Disadvantages |
---|---|
Simple equipment and processes | Inhomogeneous particle distributions |
Cost-effective for large-scale | High sintering temperatures required |
production | Poor electrochemical performance |
Environmentally friendly | Limited control over particle morphology |
2.2 Liquid-Phase Synthesis
Liquid-phase synthesis methods, such as sol-gel, hydrothermal, and coprecipitation, offer better control over particle size, morphology, and composition. These methods involve dissolving the precursors in a solvent, followed by precipitation, drying, and calcination to form the LFP powder. While these methods yield superior electrochemical performance, they are more complex and costly (Wang et al., 2019).
Table 2: Advantages and Disadvantages of Liquid-Phase Synthesis
Advantages | Disadvantages |
---|---|
Better control over particle size and | Complex and costly processes |
morphology | Long synthesis times |
Improved electrochemical performance | Solvent recovery and disposal |
Enhanced material homogeneity | Potential for contamination |
3. Market Dynamics and Trends
The LFP battery market has experienced rapid growth, driven by increasing demand from the electric vehicle (EV) and energy storage sectors. This section analyzes the current market status, growth drivers, and forecasts.
3.1 Current Market Status
The global LFP battery market has seen significant expansion in recent years, driven by technological advancements, cost reductions, and increased awareness of sustainability issues. In 2023, the market for LFP battery surpassed that of Nickel-Manganese-Cobalt (NMC) batteries in terms of new energy vehicle installations .
3.2 Growth Drivers
Several factors have contributed to the growth of the LFP battery market:
- Increasing EV Penetration: Growing concerns about air pollution and climate change have led to increased demand for EVs, which rely heavily on LFP battery for their power sources.
- Cost-Effectiveness: Compared to other lithium-ion battery chemistries, LFP battery offer lower production costs, making them an attractive option for cost-sensitive applications.
- Improved Performance: Recent technological advancements have significantly enhanced the energy density, charging speed, and cycle life of LFP battery.
3.3 Market Forecasts
Market forecasts indicate continued growth for the LFP battery market, driven by increasing demand from the EV and energy storage sectors. By 2030, the global LFP battery market is projected to reach over USD 100 billion, with a compound annual growth rate (CAGR) of approximately 30% .
4. Challenges Facing the LFP Battery Industry
Despite its significant market growth, the LFP battery industry faces several challenges, including raw material supply constraints, trade barriers, and technological advancements that threaten its market position.
4.1 Raw Material Supply Constraints
The production of LFP battery relies heavily on the availability of lithium, iron, and phosphorus. Fluctuations in the supply and price of these raw materials can significantly impact the cost and availability of LFP battery. In particular, the availability of high-purity lithium sources has become a major concern for manufacturers (Chen et al., 2021).
Table 3: Key Raw Materials for LFP Battery Production
Raw Material | Importance | Challenges |
---|---|---|
Lithium | Essential component | Limited global reserves |
of cathode material | Concentrated in a few countries | |
Iron | Primary metal source | Widely available but requires |
purification | ||
Phosphorus | Necessary for | Environmental concerns with |
cathode structure | mining and processing |
4.2 Trade Barriers
International trade policies have created significant challenges for LFP battery manufacturers. For example, the European Union’s (EU) proposed Battery Regulation aims to reduce the carbon footprint of batteries used in the region, favoring locally sourced materials and production processes (European Commission, 2021). Such regulations could hinder the global competitiveness of non-EU LFP battery manufacturers.
Table 4: Major Trade Barriers Facing LFP Battery Manufacturers
Barrier | Impact |
---|---|
Carbon footprint regulations | Increased production costs and complexity |
Tariffs and import restrictions | Reduced market access and profitability |
Local content requirements | Discourages foreign direct investment |
4.3 Technological Advancements
Advancements in alternative battery technologies pose a threat to the dominance of LFP battery. For instance, sodium-ion batteries offer a lower-cost alternative, especially if sodium resources become more readily available. Additionally, Lithium Nickel Manganese Cobalt Oxide (NMC) and Lithium Nickel Cobalt Aluminum Oxide (NCA) batteries continue to improve in energy density and performance, narrowing the gap with LFP battery (Dunn et al., 2011).
Table 5: Comparison of LFP with Alternative Battery Technologies
Technology | Energy Density (Wh/kg) | Cycle Life (Cycles) | Cost ($/kWh) |
---|---|---|---|
LFP | Moderate | High | Low-Medium |
Sodium-ion | Low | Moderate | Low |
NMC/NCA | High | Moderate | Medium-High |
5. Strategic Recommendations
To navigate the evolving LFP battery landscape, manufacturers must adopt strategic approaches that address the challenges outlined above. The following recommendations focus on supply chain management, international expansion, and research and development.
5.1 Strengthen Supply Chain Management
To mitigate raw material supply constraints, LFP battery manufacturers should prioritize supply chain diversification and vertical integration. This includes:
- Diversifying Raw Material Sources: Establishing partnerships with suppliers in various regions can help ensure a stable supply of lithium, iron, and phosphorus.
- Vertical Integration: Integrating upstream processes, such as lithium extraction and iron ore mining, can reduce dependence on external suppliers and control costs.
5.2 Expand International Footprint
To overcome trade barriers and tap into new markets, LFP battery manufacturers should consider international expansion. Strategies include:
- Establishing Local Production Facilities: Building manufacturing plants in key markets can reduce transportation costs and minimize the impact of trade regulations.
- Collaborating with Local Partners: Forming strategic partnerships with local companies can facilitate market entry and ensure compliance with local regulations.
5.3 Invest in Research and Development
Continued investment in research and development is crucial to maintaining LFP batteries’ competitiveness in the face of advancing technologies. Priorities include:
- Energy Density Enhancement: Developing new cathode materials and electrolytes that improve energy density can help LFP battery compete with NMC and NCA batteries.
- Fast-Charging Capabilities: Enhancing charging speeds can broaden LFP batteries’ applications, particularly in the EV sector.
- Recycling and Sustainability: Investing in recycling technologies can reduce raw material consumption, lower production costs, and enhance environmental sustainability.
6. Conclusion
Lithium Iron Phosphate battery (LFP battery) have emerged as a dominant force in the global battery market, driven by their safety, cost-effectiveness, and long cycle life. Despite significant market growth, the LFP battery industry faces challenges related to raw material supply, trade barriers, and technological advancements. To navigate these challenges and maintain competitiveness, manufacturers must adopt strategic approaches that prioritize supply chain management, international expansion, and research and development. By addressing these areas, the LFP battery industry can continue to thrive and contribute to the global transition towards a low-carbon future.