Abstract
This comprehensive article presents a detailed approach for the high-value recycling of waste lithium iron battery (LiFePO4 battery) cathode materials. The method efficiently recovers Fe, P, and Li elements in the forms of FeSO4, FePO4, and Li3PO4, respectively. A unique five-step process, without the use of phosphoric acid or phosphates, achieves a high recovery yield of 93% for lithium as Li3PO4. This work contributes significantly to the circular economy of lithium-ion batteries and promotes environmentally friendly and sustainable practices.
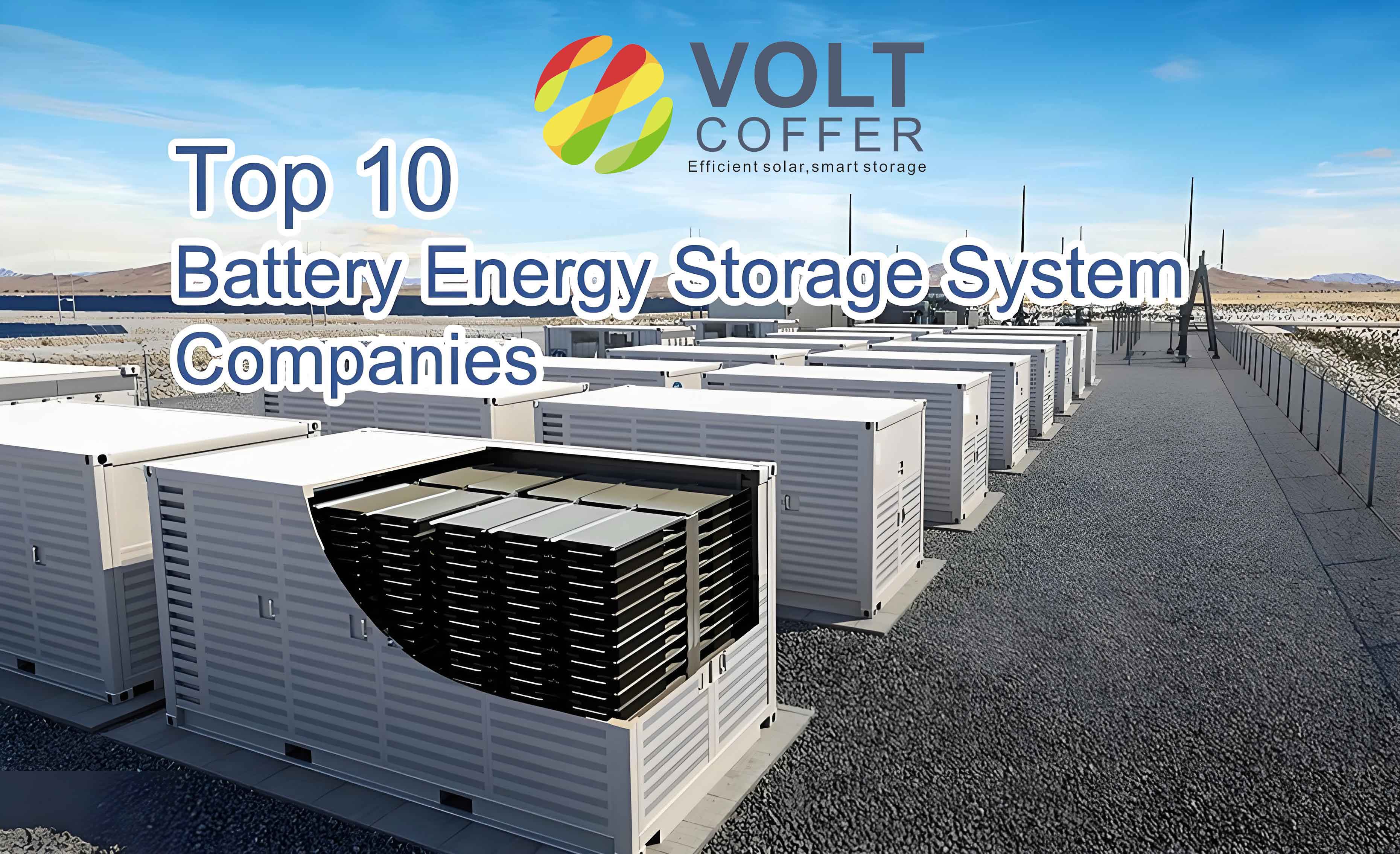
Introduction
lithium iron battery (LiFePO4 battery) batteries have gained significant popularity in recent years due to their eco-friendliness, abundant raw materials, low cost, high specific capacity, excellent cycle performance, and thermal stability. Since their first report in 1997 ,lithium iron battery (LiFePO4 battery) have been widely used in electric vehicles, energy storage systems, and other applications .
With the rapid expansion of the global electric vehicle market, a significant number of lithium-ion batteries are approaching the end of their service life. The first wave of lithium iron battery (LiFePO4 battery) retirements is imminent, leading to a surge in waste batteries requiring proper disposal and recycling. Improper handling of these batteries can pose serious environmental risks due to their toxic and corrosive components. Therefore, the development of efficient and sustainable recycling methods for lithium iron battery (LiFePO4 battery) is crucial.
Background and Motivation
Environmental and Economic Imperatives
The disposal of spent lithium-ion batteries has emerged as a global concern due to the presence of toxic heavy metals and organic solvents. Improper disposal practices can lead to soil and water contamination, posing significant risks to ecosystems and human health . In contrast, recycling these batteries not only mitigates environmental hazards but also creates new economic opportunities .
From an economic perspective, the recovery of valuable metals such as lithium, cobalt, nickel, and iron from spent batteries can significantly reduce raw material costs and enhance resource efficiency . The high value of these metals, particularly lithium, further underscores the need for efficient recycling processes .
Recycling Technologies
Existing recycling technologies for lithium-ion batteries can be broadly classified into three categories: cascading utilization, disassembly-separation recycling, and metallurgical recycling . Each approach has its unique advantages and limitations:
- Cascading Utilization: Involves reusing retired batteries in less demanding applications such as energy storage systems or low-speed electric vehicles .
- Disassembly-Separation Recycling: Entails physically dismantling batteries, separating components, and recovering valuable materials through sorting .
- Metallurgical Recycling: Focuses on chemically extracting metals from electrode materials using pyrometallurgical or hydrometallurgical methods .
Proposed Recycling Method
The recycling method introduced in this article focuses on the hydrometallurgical recovery of Fe, P, and Li from waste lithium iron battery (LiFePO4 battery) cathode materials. The process comprises five key steps, as illustrated, and does not use phosphoric acid or phosphates, differentiating it from traditional recycling processes.
Step 1: Acid Dissolution
The first step involves dissolving the waste lithium iron battery (LiFePO4 battery) cathode material in sulfuric acid. This step releases Fe2+, Li+, and H2PO4- ions into solution, facilitating their subsequent recovery. The choice of sulfuric acid as the leaching agent ensures low cost and environmental friendliness.
Step 2: Recrystallization of FeSO4
Over one-third of the Fe2+ ions are recrystallized as ferrous sulfate (FeSO4) by adjusting the solution conditions. This step efficiently removes a substantial portion of iron from the solution, simplifying subsequent precipitation steps.
Step 3: Precipitation of FePO4
The remaining Fe2+ ions in the solution are oxidized to Fe3+ using hydrogen peroxide and the pH is adjusted to 2.0–3.0 using sodium hydroxide. Under these conditions, Fe3+ ions react with PO43- ions to form FePO4 precipitates. These precipitates can be directly used for the solid-phase synthesis of lithium iron battery (LiFePO4 battery).
Step 4: Precipitation of Li3PO4
After separating the FePO4 precipitates, the pH of the filtrate is increased to 11.0, causing the precipitation of Li3PO4. This step efficiently recovers lithium in a stable and valuable form.
Step 5: Resynthesis of LiFePO4
The recovered FeSO4 and Li3PO4 are then used to synthesize lithium iron battery (LiFePO4 battery) through either solid-phase or hydrothermal methods. The resulting lithium iron battery (LiFePO4 battery) materials exhibit excellent electrochemical performance, suitable for reuse in lithium-ion batteries.
Experimental Details
Materials and Methods
Preparation of Waste Lithium Iron Battery (LiFePO4 battery)
The waste lithium iron battery (LiFePO4 battery) used in this study was obtained from retired lithium iron battery (LiFePO4 battery) electrodes. The electrodes were initially cleaned with an alkaline solution to remove impurities, followed by mechanical crushing and sieving to achieve a particle size of <10 μm. The powder was then heat-treated at 350°C for 2 hours in an inert atmosphere to decompose the PVDF binder, facilitating acid dissolution.
Table 1: Composition of LFP/C Waste Powder
Element | Li | Fe | P | C |
---|---|---|---|---|
Mass % | 3.93 | 30.06 | 16.35 | 8.22 |
Acid Dissolution and Recrystallization
Different concentrations of sulfuric acid (15% to 40% by mass) were used to dissolve the lithium iron battery (LiFePO4 battery) at temperatures of 30°C and 15°C. The resulting solutions were then subjected to recrystallization to precipitate FeSO4.
Synthesis of Lithium Iron Battery (LiFePO4 battery)
Two methods were employed to synthesize lithium iron battery (LiFePO4 battery) from the recovered materials:
- Solid-phase Method: Involves mixing FePO4, Li2CO3, and glucose, followed by ball milling, spray drying, and sintering in a nitrogen atmosphere.
- Hydrothermal Method: Utilizes FeSO4, Li3PO4, and water as precursors, which are mixed and reacted in a high-pressure reactor. The resulting product is then spray-dried and sintered to obtain lithium iron battery (LiFePO4 battery).
Characterization Techniques
Various analytical techniques were used to characterize the materials, including:
- X-ray Diffraction (XRD): For phase identification.
- Scanning Electron Microscopy (SEM): To observe microstructural features.
- Inductively Coupled Plasma Optical Emission Spectrometry (ICP-OES): For compositional analysis.
- Electrochemical Testing: To evaluate the performance of the recycled lithium iron battery (LiFePO4 battery) materials in lithium-ion batteries.
Results and Discussion
Recovery Yields
The recovery yields of Fe, P, and Li were investigated under various experimental conditions. The results showed that over 30% Fe recovery as FeSO4 consistently led to high Li3PO4 yields exceeding 90%, with an optimal yield of 93% achieved under specific conditions .
Characterization of Recovered Materials
XRD analysis confirmed the high purity of the recovered FeSO4 and Li3PO4 materials . The FeSO4 existed primarily as FeSO4·4H2O and FeSO4·7H2O, while Li3PO4 exhibited sharp diffraction peaks indicative of good crystallinity.
Electrochemical Performance
Electrochemical testing revealed that the recycled lithium iron battery (LiFePO4 battery) materials prepared by both solid-phase and hydrothermal methods exhibited excellent performance. In particular, the hydrothermally synthesized lithium iron battery (LiFePO4 battery) material showed better capacity and rate capability, likely due to its nanoscale particle size and morphology .
Comparison with Existing Methods
Compared to traditional recycling methods that rely on phosphoric acid or phosphates, the proposed method offers several advantages:
- Environmental Friendliness: The absence of phosphoric acid reduces the potential for environmental contamination.
- Cost-Effectiveness: Sulfuric acid is less expensive than phosphoric acid, lowering the overall recycling costs.
- High Recovery Yields: The method achieves high recovery yields for all target elements, particularly lithium.
Conclusion and Future Work
This study successfully demonstrated a novel hydrometallurgical approach for the high-value recycling of waste lithium iron battery (LiFePO4 battery) cathode materials. The method efficiently recovers Fe, P, and Li in useful forms, with lithium recovered as Li3PO4 achieving a yield of up to 93%. The recovered materials were used to synthesize lithium iron battery (LiFePO4 battery) through solid-phase and hydrothermal methods, with the latter exhibiting superior electrochemical performance.
Future work could focus on optimizing the recycling process to further improve recovery yields and reduce costs. Additionally, the scalability and commercial viability of the method should be thoroughly evaluated to facilitate its widespread adoption in the lithium-ion battery recycling industry.