The exponential growth of retired lithium-ion batteries (LIBs), particularly LiFePO4 batteries, over the next 3–5 years necessitates the development of advanced recycling technologies. Traditional methods face challenges such as low system integration, high energy loss, labor intensity, and environmental pollution. This study focuses on optimizing a high-throughput, integrated, intelligent charged crushing and pyrolysis system for retired LiFePO4 batteries, emphasizing efficiency, safety, and economic viability.
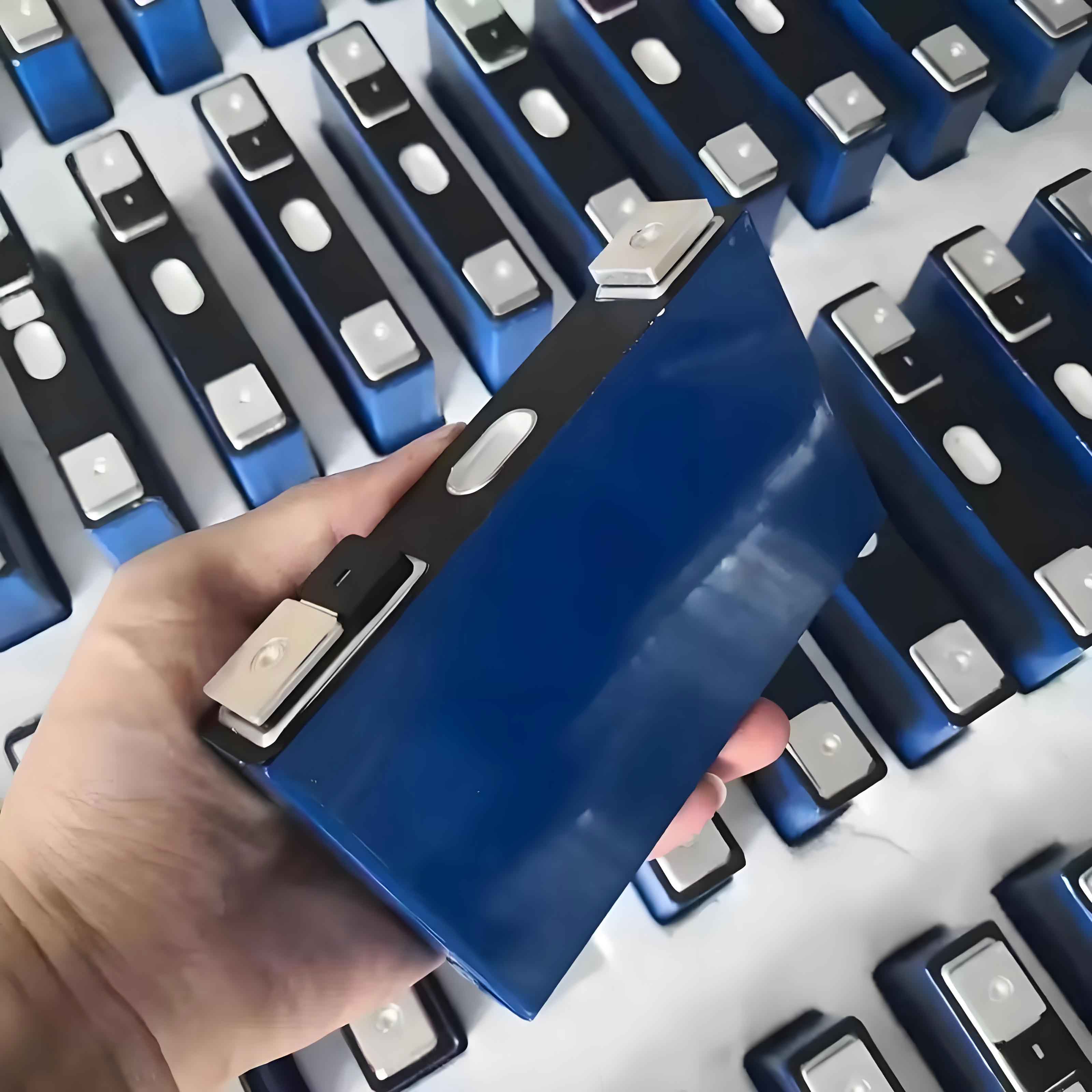
1. Introduction
The global shift toward electric vehicles (EVs) and renewable energy storage has led to a surge in LiFePO4 battery adoption due to their high safety, long cycle life, and cost-effectiveness. By 2023, China accounted for 64.8% of global EV sales, with LiFePO4 batteries dominating 72.6% of the domestic market. However, the 5–8-year lifespan of these batteries results in massive retirement volumes—35,000 tons in 2022, projected to reach 2.4 million tons by 2027. Recycling retired LiFePO4 batteries is critical for recovering valuable materials (e.g., copper, aluminum, lithium) and mitigating environmental risks from toxic components like LiPF6 and PVDF.
2. Methodology
2.1 Puncture Discharge and Charged Breakage
Retired LiFePO4 batteries retain residual voltage (3.47 V on average), posing safety risks during recycling. We evaluated four discharge methods (Table 1):
Method | Process | Advantages | Disadvantages |
---|---|---|---|
Chemical Discharge | Immersion in salt solutions | Low cost | Corrosion, toxic byproducts |
Load Discharge | External resistor discharge | Environmentally friendly | Voltage rebound risk |
Physical Breakage | Mechanical crushing | Fast | High safety risks |
Puncture Discharge | Short-circuit via needle in N₂ | Safe, rapid, efficient | Residual charge on electrodes |
Puncture discharge was selected for its efficiency (95.15% discharge within 30 min) and safety. The voltage decay follows:Discharge Efficiency (%)=(1−VremainingVinitial)×100Discharge Efficiency (%)=(1−VinitialVremaining)×100
For a fully charged LiFePO4 battery (3.325 V), puncture discharge reduces voltage to 0.15 V within 30 min.
2.2 Thermal Decomposition and Material Recovery
The discharged LiFePO4 batteries undergo pyrolysis in a nitrogen atmosphere to decompose organic components (e.g., PVDF, electrolytes). Key parameters include:
- Temperature: 450°C (optimized via COMSOL simulations for uniform heat distribution).
- Gas flow: Controlled to ensure efficient removal of volatile compounds.
- Process time: ≤60 min for complete decomposition.
Post-pyrolysis, mechanical separation (crushing, sieving, magnetic sorting) yields:
- Copper (Cu): Purity = 99.4±0.2%99.4±0.2%
- Aluminum (Al): Purity = 99.16±0.3%99.16±0.3%
- Black powder: Contains LiFePO4 (2.4±0.4%2.4±0.4%), graphite (20±5%20±5%), and trace impurities (Cu: 0.32±0.13%0.32±0.13%, Al: 0.18±0.05%0.18±0.05%).
3. Results and Analysis
3.1 Discharge Performance
- Time vs. Voltage: Full discharge (0.015 V) achieved in 60 min with 99.6% efficiency.
- Energy Consumption: ≤1.2 kWh per ton of LiFePO4 batteries.
3.2 Material Recovery Efficiency
- Overall yield: 98.5% for Cu, Al, and black powder.
- Black powder composition:
Component | Content (%) |
---|---|
LiFePO4 | 2.4±0.42.4±0.4 |
Graphite | 20±520±5 |
Cu impurities | 0.32±0.130.32±0.13 |
Al impurities | 0.18±0.050.18±0.05 |
3.3 Economic Evaluation
The processing cost for retired LiFePO4 batteries is ≤1,500 CNY per ton, with revenue streams from:
- Copper: 99.4% purity, valued at ~65,000 CNY/ton.
- Aluminum: 99.16% purity, valued at ~18,000 CNY/ton.
- Black powder: Lithium recovery potential offsets costs.
The net profit margin exceeds 20%, making this method economically viable for large-scale adoption.
4. Environmental and Safety Considerations
Retired LiFePO4 batteries pose hazards if mishandled (Table 2):
Material | Hazard | Environmental Impact |
---|---|---|
LiFePO4 | Reacts with acids/bases | Phosphorus water contamination |
LiPF6 | Releases HF gas upon hydrolysis | Soil/water acidification |
Graphite | CO emissions during combustion | Air pollution |
PVDF | HF release at high temperatures | Fluoride pollution |
The proposed system mitigates risks via:
- Closed-loop N₂ environment: Prevents combustion and toxic gas release.
- Automated controls: Reduces human exposure to hazardous materials.
5. Conclusion
This study demonstrates that high-throughput integrated thermal decomposition equipment enables efficient, safe, and profitable recycling of retired LiFePO4 batteries. Key achievements include:
- 95.15% discharge efficiency within 30 minutes.
- 98.5% material recovery rate with high-purity outputs.
- ≤1,500 CNY/ton processing cost, ensuring economic feasibility.
Future work will focus on scaling the system and optimizing lithium extraction from black powder to enhance sustainability.