Abstract:
The research of a distributed equalization charging system for series energy storage power supplies. By utilizing a four-cell direct equalization topology paired with bidirectional DC converters, the proposed system achieves efficient equalization within any individual cell or group, as well as across different groups. This parallel equalization approach significantly enhances the equalization speed of long-string battery packs. The distributed structure also facilitates system scalability. The paper provides a comprehensive analysis of the system’s operational principles, mathematical modeling, simulation validation, and experimental verification.
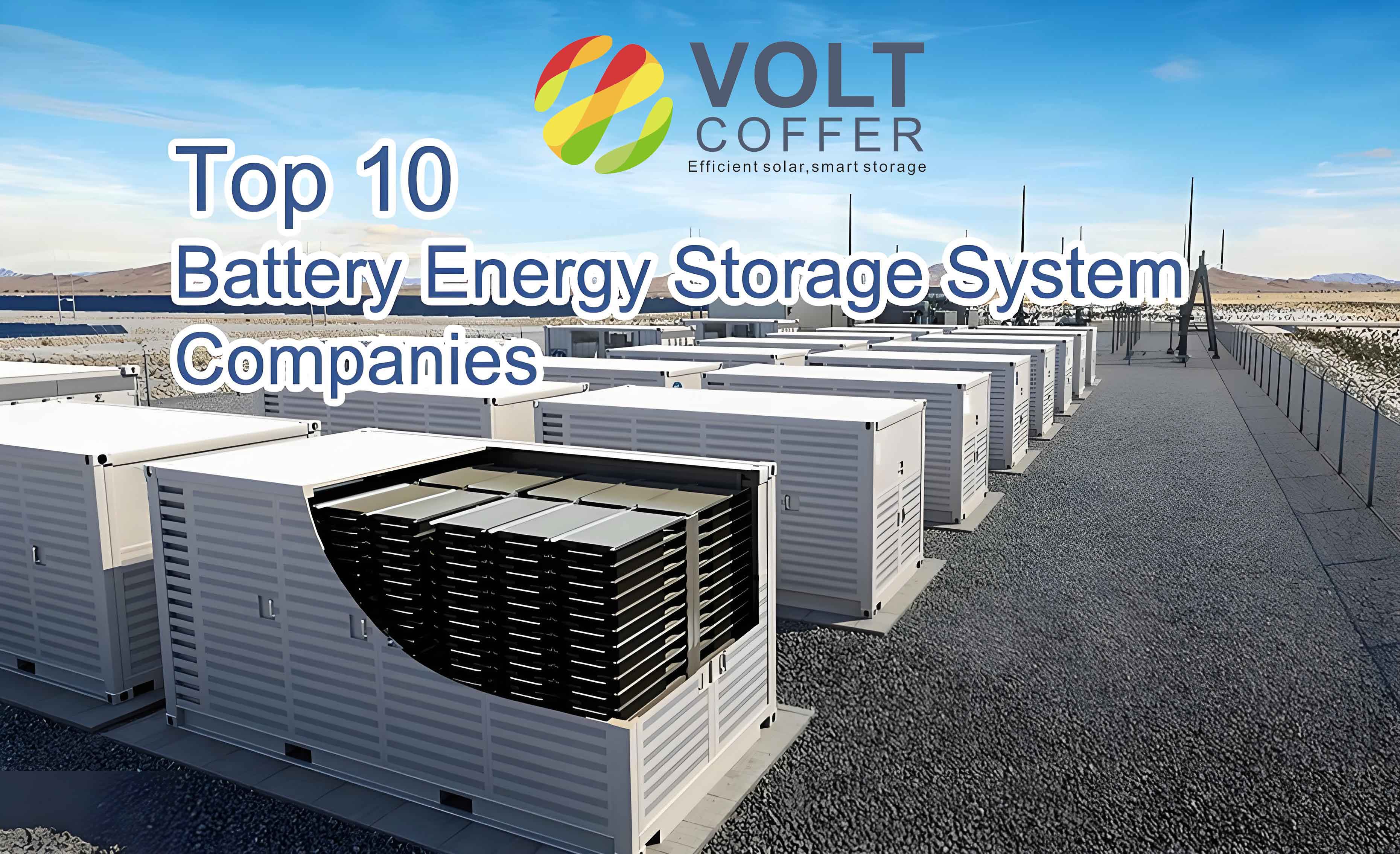
Keywords: Energy storage; Distributed charging; Equalization strategy; Cross-group equalization
1. Introduction
Energy storage power supplies play a crucial role in various applications, ranging from renewable energy integration to backup power systems. However, long-string series connections of energy storage cells are often necessary to achieve the desired voltage levels. Due to manufacturing variances and differences in aging, self-discharge rates, working conditions, and environments, cell inconsistencies become prominent over time. These inconsistencies can lead to overcharging and over-discharging, drastically reducing battery performance. This paper presents a distributed equalization charging system designed to address these challenges.
Table 1: Overview of Research Areas
Research Area | Brief Description |
---|---|
Lower-level Cell Topology | Topologies for equalizing energy between individual cells |
Distributed Charging System | Structure and benefits of distributed charging systems |
Equalization Control Strategy | Methods for controlling and optimizing the equalization process |
2. Distributed Equalization Charging System for Series Energy Storage Power Supply
2.1 Introduction
The distributed equalization charging system consists of multiple paralleled charging modules with series-connected outputs, forming a two-tier system. Each module contains a bidirectional DC converter and a four-cell equalizer. This configuration allows for charging, discharging, and local self-equalization within cells, as well as cross-group equalization between cells in different groups.
2.2 Basic Structure of the Distributed Equalization Charging System
- Bidirectional DC Converter: Acts as the interface between the DC bus and the battery cells.
- Four-Cell Equalizer: Facilitates energy transfer between individual cells within a group.
- Unit Controller and Drive Circuit: Manages the operation of each converter and equalizer.
- Master Controller: Coordinates the operation of all units via CAN bus communication.
Table 2: Components of the Distributed Equalization Charging System
Component | Description |
---|---|
Bidirectional DC Converter | Interfaces DC bus with battery cells for charging and discharging |
Four-Cell Equalizer | Facilitates energy transfer between cells within a group |
Unit Controller | Manages operation of each converter and equalizer |
Drive Circuit | Provides gate signals to switches in the converter and equalizer |
Master Controller | Coordinates system operation via CAN bus communication |
2.3 Working Principles of the Distributed Equalization Charging System
2.3.1 Charging Equalization Mode
In this mode, the DC bus is connected to an external power source. Each conversion unit operates independently in buck mode. The controller monitors the state of charge (SOC) of each cell and adjusts the converter’s output voltage accordingly. If imbalances are detected, the four-cell equalizer is activated to ensure all cells are fully charged.
2.3.2 Intra-Group Equalization Mode
Intra-group equalization addresses imbalances within a cell group. It operates in either buck-boost or flyback mode, depending on whether the cells to be equalized are adjacent or non-adjacent.
Table 3: Intra-Group Equalization Modes
Mode | Adjacent Cells | Non-Adjacent Cells | Operational Principle |
---|---|---|---|
Buck-Boost | Yes | N/A | Direct energy transfer using coupled inductors |
Flyback | No | Yes | Energy stored in inductors and transferred through capacitive coupling |
2.3.3 Cross-Group Equalization Mode
Cross-group equalization facilitates energy transfer between cells in different groups. This mode employs voltage natural clamping to allow the converters to operate in boost mode during discharging.
3. Design of Magnetic Components and Converter Modeling
The design of magnetic components, such as transformers and inductors, is crucial for the system’s performance. This section outlines the design process and establishes small-signal models for the bidirectional DC converter in different operational modes.
3.1 Design of Magnetic Components
The design involves selecting appropriate materials, determining winding specifications, and verifying the design using simulations.
Table 4: Key Parameters for Magnetic Component Design
Parameter | Description |
---|---|
Core Material | Material chosen for transformer/inductor cores |
Winding Specifications | Number of turns, wire gauge, and insulation considerations |
Operating Frequency | Frequency at which the converter operates |
Maximum Flux Density | Limit to prevent saturation of transformer/inductor cores |
3.2 Converter Modeling and Control Loop Design
Small-signal models are developed for the bidirectional DC converter in buck and boost modes. These models are used to design control loops that ensure stable and efficient operation.
The control loops are designed using techniques such as Bode plot analysis to ensure stability and responsiveness.
Table 5: Control Loop Design Parameters
Parameter | Description |
---|---|
Feedback Loop | Configuration and components of the feedback loop |
Compensation Network | Circuit used to stabilize the control loop |
Gain and Phase Margin | Measures of stability and responsiveness |
4. Equalization Strategy Analysis
An effective equalization strategy is essential for maximizing the performance of the distributed equalization charging system. This section presents a strategy that balances efficiency and speed, particularly for complex imbalance scenarios.
4.1 Time-Slice Allocation for Parallel Discharging Equalization
This strategy involves allocating time slices for discharging, allowing parallel operation of multiple equalization paths. It reduces battery internal resistance losses and optimizes the equalization process.
4.2 Optimization of Equalization Schemes
Different optimization scenarios are analyzed to determine the optimal time-slice allocation based on battery resistance, initial imbalances, and target SOC.
Table 6: Optimization Scenarios
Scenario | Variables Considered |
---|---|
Initial Imbalance | Initial differences in SOC between cells |
Battery Resistance | Internal resistance of cells |
Target SOC | Desired state of charge after equalization |
5. Experimental Verification and Performance Evaluation
This section presents experimental results to validate the performance of the proposed distributed equalization charging system. The experiments demonstrate the system’s capability to handle charging, intra-group equalization, and cross-group equalization effectively.
5.1 Experimental Setup
The experimental setup includes the distributed equalization charging system, batteries, data acquisition equipment, and software for monitoring and control.
5.2 Experimental Results
The results showcase the system’s efficiency, speed, and adaptability to various imbalance scenarios. Key performance metrics, such as equalization time, energy efficiency, and battery temperature, are measured and analyzed.
Table 7: Experimental Results Summary
Performance Metric | Measured Value |
---|---|
Equalization Time | Time taken to achieve target SOC |
Energy Efficiency | Percentage of input energy successfully transferred to cells |
Battery Temperature | Temperature rise during operation |
Conclusion
This paper presents a comprehensive study of a distributed equalization charging system for series energy storage power supplies. The proposed system offers significant advantages in terms of speed, efficiency, and scalability.