Abstract
The recycling of spent lithium iron phosphate battery (LiFePO4 battery) has garnered significant attention from researchers due to their widespread applications in energy storage systems and electric vehicles. Compared to traditional hydrometallurgy and pyrometallurgy techniques aimed at extracting valuable metals, direct regeneration of cathode materials offers advantages such as lower energy consumption, shorter processes, and improved environmental friendliness. Given the stable olivine crystal structure and relatively low content of high-value metals in spent lithium iron phosphate battery (LiFePO4 battery), their direct regeneration is an economically viable option. This review article summarizes the current status of pretreatment methods, including mechanical, thermal, and chemical approaches, and highlights the latest advancements in lithium iron phosphate battery (LiFePO4 battery) regeneration techniques, such as high-temperature solid-phase regeneration, hydrothermal synthesis, and electrochemical methods. Furthermore, the challenges facing these regeneration techniques are discussed, along with recommendations for future research directions.
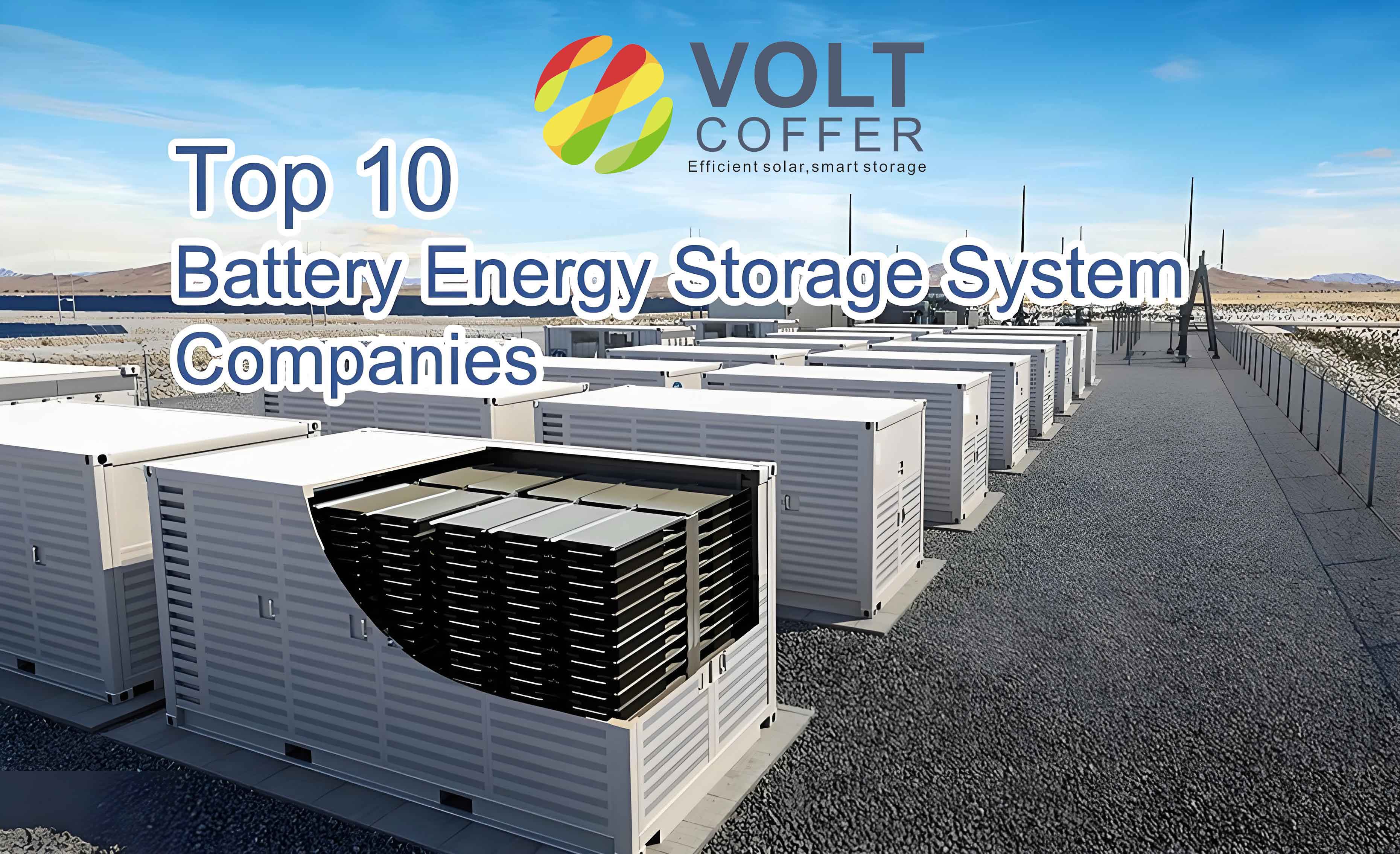
1. Introduction
Lithium iron phosphate battery (LiFePO4 battery) have gained popularity due to their high energy density, long cycle life, and excellent safety performance. However, with the increasing deployment of these batteries in various applications, a significant volume of spent lithium iron phosphate battery (LiFePO4 battery) is anticipated in the near future. The efficient recycling of these batteries is crucial not only for mitigating environmental concerns but also for recovering valuable resources and promoting a circular economy.
Unlike traditional hydrometallurgical and pyrometallurgical approaches focused on metal extraction, direct regeneration of cathode materials aims to restore the electrochemical performance of spent lithium iron phosphate battery (LiFePO4 battery) by replenishing active lithium ions and repairing structural defects. This review provides a comprehensive overview of the latest research developments in this field.
2. Pretreatment Methods for Spent LiFePO4 Cathode Materials
The pretreatment of spent lithium iron phosphate battery (LiFePO4 battery) cathode materials is essential to remove impurities such as binders, conductive agents, and current collectors, thereby improving the quality of the active material for subsequent regeneration processes. The primary pretreatment methods include mechanical, chemical, and thermal approaches.
2.1 Mechanical Methods
Mechanical methods involve the use of crushing, grinding, sieving, and other physical techniques to separate valuable components from the spent electrodes. While these methods can achieve large-scale separation, precise segregation of active materials from binders and other impurities remains challenging.
Table 1: Examples of Mechanical Pretreatment Methods
Method | Description | Advantages | Disadvantages |
---|---|---|---|
Crushing and Grinding | The electrodes are crushed and ground to reduce particle size. | Simple and scalable | Imprecise separation of components |
Sieving | The crushed materials are sieved to separate coarse and fine particles. | Efficient removal of large impurities | Difficulty in separating fine particles |
Ultrasonic Washing | Ultrasound is used to enhance the separation of active materials. | Effective for fine particle separation | High energy consumption |
2.2 Chemical Methods
Chemical methods utilize solvents or reagents to dissolve or react with specific components in the spent electrodes. For instance, NaOH solution is commonly used to dissolve aluminum foils, while organic solvents like N-methyl-2-pyrrolidone (NMP) can dissolve polyvinylidene fluoride (PVDF) binders.
Table 2: Examples of Chemical Pretreatment Methods
Solvent/Reagent | Target Component | Reaction Mechanism | Advantages | Disadvantages |
---|---|---|---|---|
NaOH | Aluminum foil | Al reacts with NaOH to form sodium aluminate | Efficient removal of Al | Additional washing steps required |
NMP | PVDF binder | Dissolves PVDF, separating it from active materials | Precise separation | Costly and potentially hazardous |
2.3 Thermal Methods
Thermal methods involve heating the spent electrodes to remove organic binders and electrolytes. High temperatures facilitate the decomposition of these components, leaving behind the active lithium iron phosphate battery (LiFePO4 battery) material. However, this approach can also lead to the oxidation of Fe²⁺ to Fe³⁺, which may necessitate additional reduction steps during regeneration.
Table 3: Examples of Thermal Pretreatment Conditions
Atmosphere | Temperature (°C) | Duration (h) | Advantages | Disadvantages |
---|---|---|---|---|
Nitrogen | 400–600 | 1–3 | Minimizes oxidation of Fe²⁺ | Potential formation of toxic byproducts |
Air | 450–650 | 1–2 | Removes carbon and oxidizes Fe²⁺ to Fe³⁺ | Additional reduction steps may be required |
3. Regeneration Techniques for Spent LiFePO4 Cathode Materials
3.1 High-Temperature Solid-Phase Regeneration
High-temperature solid-phase regeneration involves mixing the pretreated lithium iron phosphate battery (LiFePO4 battery) powder with additional lithium, iron, and phosphorus sources, followed by high-temperature sintering in an inert atmosphere. This approach aims to replenish lost lithium ions and repair structural defects.
Table 4: Examples of High-Temperature Solid-Phase Regeneration Studies
Reference | Lithium Source | Temperature (°C) | Atmosphere | Electrochemical Performance |
---|---|---|---|---|
Sun et al. | Li₂CO₃ | 350 followed by 650 | H₂/Ar | 1C discharge capacity: 137 mAh/g |
Liang et al. | Li₂CO₃, Fe, P salts | 650 | N₂ | 1C discharge capacity: 139 mAh/g |
Liu et al. | V₂O₅, LiH₂PO₄ | 700 | Ar | 1C discharge capacity after 200 cycles: 134.3 mAh/g |
3.2 Hydrothermal Synthesis
Hydrothermal synthesis utilizes high-pressure and high-temperature aqueous solutions to dissolve and recrystallize the spent lithium iron phosphate battery (LiFePO4 battery). This method offers precise control over the nucleation and crystal growth processes, leading to improved material morphology and performance.
Table 5: Examples of Hydrothermal Synthesis Studies
Reference | Lithium Source | Temperature (°C) | Duration (h) | Electrochemical Performance |
---|---|---|---|---|
Wang et al. | Li₃PO₄, FeSO₄·7H₂O | 140–200 | 6 | 0.1C discharge capacity: up to 148.0 mAh/g |
Jing et al. | Li₂SO₄·H₂O, N₂H₄ | 200 | 3 | 0.2C discharge capacity: 146.2 mAh/g |
Yang et al. | Na₂SO₃, Li₂SO₄ | 200 | – | 0.1C discharge capacity: 145.1 mAh/g |
3.3 Electrochemical Regeneration
Electrochemical regeneration harnesses an external electric field to facilitate lithium ion intercalation into the spent lithium iron phosphate battery (LiFePO4 battery) lattice. This method avoids the use of chemical reagents, making it environmentally friendly but technically challenging to scale up.
Table 6: Example of Electrochemical Regeneration Studies
Reference | Experimental Setup | Electrochemical Performance |
---|---|---|
Yang et al. | Lithium metal as counter electrode, CV cycling | 0.1C discharge capacity: 133 mAh/g (regenerated) vs. 114 mAh/g (spent) |
4. Challenges and Recommendations
4.1 Challenges
- Imprecise Material Separation: Commercial battery recycling processes often fail to precisely separate active materials from impurities, affecting the quality of the regenerated cathode.
- Structural Damage Assessment: Rapid and accurate assessment of the structural integrity of spent lithium iron phosphate battery (LiFePO4 battery) materials is crucial for determining the feasibility of regeneration.
- Scaling Up: Most studies focus on laboratory-scale experiments, and the technical challenges associated with scaling up these processes remain unresolved.
4.2 Recommendations
- Develop Advanced Separation Techniques: Improve the efficiency and precision of material separation using advanced technologies such as density-based separation and machine learning algorithms.
- Structural Characterization Tools: Develop non-destructive characterization techniques to assess the structural integrity of spent lithium iron phosphate battery (LiFePO4 battery) materials rapidly and accurately.
- Process Optimization and Automation: Optimize regeneration processes for large-scale applications and automate key steps to enhance productivity and reproducibility.
5. Conclusion
The direct regeneration of spent lithium iron phosphate battery (LiFePO4 battery) cathode materials offers a promising solution for recycling lithium-ion batteries. High-temperature solid-phase regeneration, hydrothermal synthesis, and electrochemical methods have demonstrated significant potential in restoring the electrochemical performance of spent cathodes. However, challenges related to material separation, structural damage assessment, and process scalability need to be addressed for the widespread adoption of these technologies. Future research should focus on developing advanced separation techniques, improving structural characterization methods, and optimizing large-scale regeneration processes.