For achieving the comprehensive utilization of solar energy, photothermal and optoelectronic, although the current technology for utilizing electricity is very mature, there are still issues such as low energy distribution density and occupying a large amount of area, and the energy obtained is related to the four seasons, day and night, cloudy and sunny weather conditions, etc. At present, there are two problems that must be solved for the utilization of thermal energy: firstly, the heat generated by direct photoelectric systems is not concentrated enough, and only low-temperature thermal energy can be obtained, which has limited utilization value. To increase the temperature and utilization value of thermal energy, the most effective method is to use concentrated light; Secondly, it is to solve the problem of how to deliver thermal energy to the user’s home.
1. Working principle of traditional solar concentrators
The function of a solar concentrator is to gather scattered sunlight. Then make use of it. There are two forms of solar concentrators, as shown in Figures 1 and 2. Figure 1 is a reflection type, which uses a parabolic reflector to gather light. Reflective solar concentrators can be divided into point focusing and line focusing; Figure 2 is a transmission type that uses a convex lens to concentrate light rays. Spot solar concentrators are further divided into point focusing and line focusing.
The convex lens is used for linear focusing, and the focal spot formed by the lens is a straight line. By adopting a flat structure with Fresnel lenses, the weight of convex lenses is reduced. On this basis, this article has improved the classic Fresnel lens by changing from radial cutting to axial cutting, solving the problem of uneven tooth profile. This reduces the number of stripes and makes the surface smoother, with a more reasonable structure and higher efficiency.
Due to manufacturing issues, there will be rounded corners at the connection of each stripe, which prevents the light from focusing and reduces efficiency. By reducing the number of stripes, process defects can be effectively solved, thereby improving efficiency. To avoid the focus shift caused by changing the convex lens to a flat form, this article only adjusted the diameter of the arc.
2. Comparative analysis of focusing systems
Firstly, it is necessary to select a point shaped spot focusing system and a circular line shaped spot focusing system. The dot shaped spot has a high focusing factor, with a focusing factor of over 500 times and high photoelectric conversion efficiency. But the accompanying problems are the expensive price and high cooling system requirements of the gallium arsenide solar cells used. When the solar cell heats up severely, it may burn out the gallium arsenide solar cell. Secondly, photocells also have relatively high requirements for focusing quality. The uneven intensity of spot light can also cause damage to gallium arsenide solar cells, making operation and maintenance difficult. However, the focusing factor of the linear spot focusing system is not high, and ordinary monocrystalline silicon solar cells can meet the requirements. When the focusing intensity is below 20 times, the photoelectric efficiency will not be significantly affected. At the same time, due to the low concentration intensity, the uniformity of the light spot is not required, and the requirements for the cooling system are also relatively low. Generally, gravity heating can be naturally circulated, and operation and maintenance are relatively simple. Therefore, linear spot is selected in this article.
Secondly, whether to use reflection focusing or transmission focusing as the focusing form. Currently, most line focusing methods use reflective focusing. However, whether using parabolic or Fresnel shapes, reflective focusing has a relatively dispersed structure. It is difficult to maintain a fixed shape for a long time, especially in strong wind environments, and it is even more difficult to install on a biaxial oriented platform. In addition, as the solar cell is located between the sun and the reflector, the shadow of the solar cell will fall on the reflector. To avoid this situation, the focal length of the reflector cannot be too small, which invisibly increases the external dimensions of the equipment and increases the difficulty of structural design. At the same time, focusing with a transparent mirror also has its drawbacks, as light passing through the mirror will cause half wave loss. Although using an anti reflective film may increase costs, it can reduce light loss. At the same time, a closed space can be formed between the focusing lens and the photocell, which can reduce heat loss, facilitate heat collection, and improve the thermal efficiency of the device. In terms of structure, it is also more compact, sturdy, and has better overall integrity compared to reflective focusing. Taking all factors into consideration, this article adopts a linear spot lens for focusing.
3. Design of irregular cylindrical flat lens
Irregular cylindrical flat lens is a type of cylindrical lens with linear light spots, consisting of several bar shaped cylindrical surfaces of different widths and radii that are spliced together and installed on a sufficiently strong base plate to form a flat lens. The processing technology of cylindrical flat lenses varies depending on the material used. For pure white glass, the main method is to use rollers for rolling, which produces products with good quality and high efficiency. However, nowadays glass factories use float production, and the cost of roller manufacturing and machine shift is relatively high, which is not suitable for trial production products. If organic glass or PC board (polycarbonate) is used for processing, there are many processing methods, such as extrusion, injection molding, rolling, carving, etc.
Extrusion processing is a commonly used process in plastic processing, characterized by high production efficiency, guaranteed product quality, and suitability for large-scale production. Its disadvantage is that it requires the opening of extrusion molds, and each production requires cleaning and maintenance of the molds, which will generate a certain amount of waste, so the cost is also relatively high; Mold injection processing is suitable for large-scale processing of small parts. For large-area sheet materials such as cylindrical lenses, it is difficult to open the mold; Secondly, it is difficult to control the deformation after molding. Rolling processing is also applied in the plastic industry, especially for PC sheet rolling, where the process requirements are relatively high. Before rolling, the material should be degassed and the temperature should be maintained at around 120-150 ℃ for 6 hours. If the humidity is too high, bubbles may appear inside the plastic. At 180 ℃, plastic enters a high elastic state, and at this point, the material will return to its pre rolling state after passing through the rolling mill. Carving is a good choice for manufacturing plastic products. Low investment and flexible processing.
But the difficulty in the process lies in the surface treatment of the product. The surface polishing of organic glass is generally carried out using H-O flame polishing. For polycarbonate flame polishing, carbon particles may precipitate, and mechanical polishing is more time-consuming. Dichloromethane steam polishing can be used. The boiling point of dichloromethane is 40 ℃, which is easy to achieve in the process. However, dichloromethane is a toxic gas, and attention should be paid when using it.
Another process method was adopted for the surface treatment of polycarbonate boards. First, rough surface polishing is done manually, and then a transparent protective film is sprayed on top. By utilizing the self leveling properties of the protective film liquid, the rough surface is filled to obtain a smooth surface. This not only increases surface hardness, but also achieves polishing, in addition to increasing transparency. In summary, it is more appropriate to use precision carving during the experimental stage.
The top view and cross-sectional view of the spotlight lens made according to the above preparation method are shown in the figure 3.
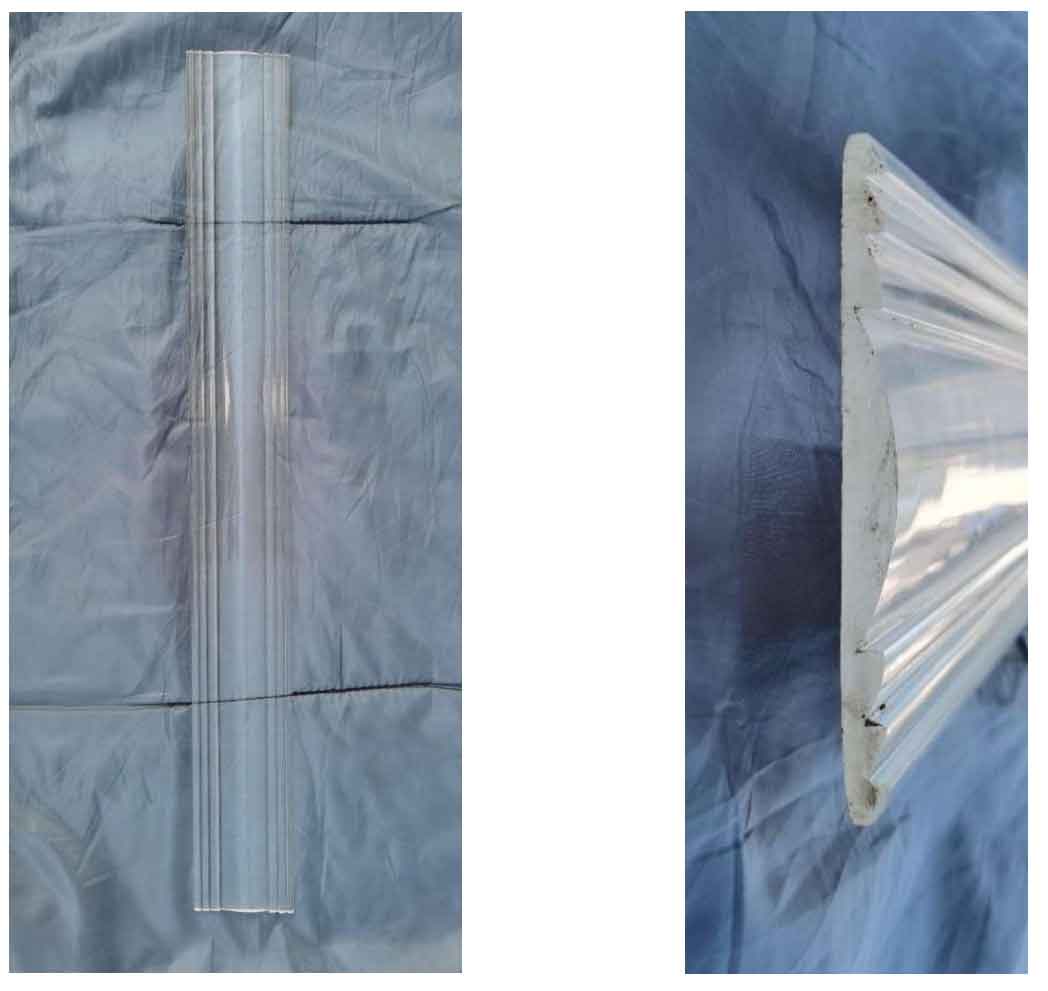
The performance comparison was conducted on four materials used for linear focusing flat lenses: white glass, ultra white glass, organic glass, and endurance plate (polycarbonate). The specific parameters are shown in the table. Among these four materials, ultra white glass has the highest visible light transmittance, with a transmittance of 92%; The endurance board is 88%, with the best impact resistance being the endurance board, which has an impact strength 250 times that of glass and a tensile strength of 170mPa. The other parameters are shown in the table.
Performance | Unit | Organic glass | PC board | PVC board | Fiberglass | Glass |
Density | g/cm | 1.2 | 1.2 | 1.3-1.5 | 1.4-1.6 | 2.5 |
Impact strength | Poor | Very good | General | General | Very poor | |
Continuous use temperature | ℃ | 90 | 120 | 75 | 100 | 240 |
Visible light head pass rate | % | 82 | 88 | 80 | 86 | 90 |
Translucency performance | Very good | Very good | Poor | Poor | Very good | |
UV transmittance | % | 40 | 0 | 0 | 20 | 80 |
Combustion performance | Flammable | Difficult to ignite | Flammable | Flammable | Non combustible |