Renewable energy plays an important role in energy conservation, emission reduction, and environmental pollution reduction. As a clean energy technology, solar thermal power generation is considered a promising power generation technology with broad application prospects. Equipping energy storage systems in solar thermal power plants can achieve longer and more flexible operating modes, improving energy utilization efficiency. The thermal storage performance of concrete sensible heat energy storage system and packed bed energy storage system were analyzed separately. For different energy storage systems, due to differences in operating mode, geometric structure, and thermal storage medium, their energy storage capacity and cost will also be different. Therefore, it is necessary to compare the energy storage costs of different energy storage systems. For the sensible latent heat combined packed bed energy storage system, the impact of sensible heat density on the energy storage cost of the system was analyzed. Meanwhile, the optimal sensible heat proportion is determined based on the energy storage system cost, energy storage system efficiency, and energy storage system rate under different sensible heat volume ratios. Because factors such as different material compositions, material prices, and energy storage have an impact on the unit energy storage system cost, sensitivity analysis is needed to identify the main factors and analyze their impact trends on economic indicators.
Based on liquid sensible heat storage, solid sensible heat storage, and phase change latent heat storage technologies, analyze the cost composition of dual tank molten salt energy storage systems, concrete energy storage systems, and phase change packed bed energy storage systems. Dual tank molten salt energy storage uses liquid molten salt as the heat storage medium, concrete energy storage uses high-temperature concrete as the heat storage medium, and phase change packed bed energy storage mainly uses encapsulated phase change materials as the heat storage medium. Due to differences in energy storage media and structural forms, there are also differences in investment costs and energy storage system costs.
1. Dual tank molten salt energy storage system
Dual tank molten salt energy storage is currently the most widely used commercial energy storage system in solar thermal power plants. The system consists of multiple parts, including foundation, tank body, molten salt fluid, and insulation layer. In order to reduce heat loss, insulation materials are arranged on the foundation and walls of the storage tank to reduce heat loss.
The dual tank molten salt energy storage system includes a hot tank and a cold tank. The hot tank is made of stainless steel material, while the cold tank is made of carbon steel material. During the heat storage process, the low-temperature molten salt in the cold tank is heated by the collector, and the heated high-temperature molten salt flows into the hot tank, where energy is stored in the form of high-temperature molten salt. The stored heat can ensure continued power generation in the absence of sunlight, and the amount of molten salt in the system is roughly equivalent to the capacity of a tank. Table 1 shows the main design parameters of the dual tank molten salt energy storage system. The temperatures of the low-temperature and high-temperature molten salt fluids are 300 ℃ and 600 ℃, respectively. The system efficiency is mainly determined by the constant molten salt outflow temperature.
Parameters | Size |
Can body height (𝐻𝑡) | 14 m |
Can body diameter (𝐷𝑡) | 6.60 m |
Tank thickness | 0.05 m |
Thickness of insulation layer material | 0.50 m |
Thermal conductivity of insulation layer | 0.039 W/(m · K) |
Heat transfer fluid (HTF) | 60% NaNO3&40% KNO3 |
Working temperature range | 300 ℃ -600 ℃ |
Based on the above cost structure, the cost of a dual tank molten salt energy storage system mainly includes costs related to the tank body, molten salt fluid costs, installation costs, and certain indirect costs. Indirect costs generally refer to the expenses of electrical, instrumentation, valves, and accessories associated with energy storage systems, calculated at 10% of the combined basic cost and material cost (tank, molten salt, and insulation materials). The expression for system cost is as follows:

Among them, total is the total cost of the energy storage system, $; ank is the cost related to the tank body, $; ℎ f is the cost of molten salt fluid, $; , is the indirect cost of the energy storage system, $; , install is the installation cost of the energy storage system. Because two tank bodies are used, all other costs related to the tank body, except for the tank body itself, need to be multiplied by 2.
The costs related to the tank mainly include the cost of the tank itself, the cost of the basic platform, and the cost of insulation materials. Their calculation formula is:

Among them, is the density of stainless steel material, kg/m ^ 3; s is the density of carbon steel material, kg/m ^ 3; is the radius of the tank body, m; is the thickness of the tank body, m; is the height of the tank body, m; ∗ is the unit price of stainless steel, $/kg; ∗ is the unit price of carbon steel, $/kg; ∗ t is the unit area cost of the basic platform, $/m ^ 2; ∗\ns is the unit price of insulation materials, $/m ^ 2.
The cost calculation of molten salt fluid is as follows:
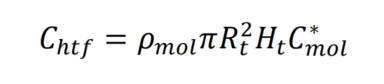
Among them, ol is the density of the molten salt fluid, kg/m ^ 3; ∗ ol is the unit mass cost of molten salt, $/kg.
The indirect cost calculation formula for the dual tank molten salt energy storage system is:

The installation cost of the dual tank molten salt energy storage system is calculated as follows:

The data used for cost calculation of the dual tank molten salt energy storage system is shown in Table 2.
Materials | Cost |
Molten salt ($/kg) | 0.717 |
Stainless steel ($/kg) | 5.430 |
Carbon steel ($/kg) | 2.500 |
Thermal insulation materials ($/m2) | 235 |
Basic Platform ($/m2) | 1210 |
2. High temperature concrete energy storage system
The concrete energy storage system module mainly consists of high-temperature concrete medium and heat transfer pipelines embedded in concrete. Pipelines are mainly used for conveying and distributing heat transfer fluids, while concrete is used for storing heat. At the same time, in order to increase the depth of heat transfer, fins are added to the outer surface of the pipeline. The outer surface of the concrete energy storage system module is equipped with insulation materials to reduce heat loss. The total cost of concrete energy storage system modules mainly includes two parts: direct cost and indirect cost. The direct costs mainly include the costs of concrete, stainless steel pipes, fins, concrete platforms, and insulation materials. Due to the use of air as the heat transfer fluid, the cost can be ignored. Indirect costs mainly include miscellaneous costs such as instruments, valves, and accessories.
The material cost of concrete thermal storage media is mainly calculated by mass, and the calculation formula is as follows:

In the formula, is the cost of concrete in the energy storage system module, $; is the diameter of the energy storage system module, m, and is the number of heat transfer pipelines in the module; ube is the diameter of the heat transfer pipeline, m; in is the number of fins on each pipeline; in is the thickness of the fins, m; ℎ in is the height of the fins, m; is the length of the thermal storage module, m; is the density of concrete, kg/m ^ 3; is the cost per unit mass of concrete, $/kg.
The cost calculation of heat transfer pipes and fins is as follows:

In the formula, ube is the cost of the heat transfer pipeline and fins, $; is the density of stainless steel, kg/m ^ 3; \n is the radius of the heat transfer pipeline, m; is the unit mass cost of stainless steel, $/kg.
A foundation platform is set at the bottom of the concrete module. The foundation platform is 230 mm thick concrete. There is a 400 mm thick foam glass insulation board on the platform. The energy storage system module is placed on the foam glass insulation board. The cost calculation for the basic platform and external insulation materials of the concrete energy storage system module is as follows:

In the formula, od represents the cost of the energy storage system module foundation platform and insulation materials, $; is the length of the concrete heat storage module, m; is the unit price of foam glass thermal insulation board, $/m ^ 3; \ns is the unit price of external insulation materials, $/m ^ 2.
The indirect cost of the energy storage system module is 10% of the total cost of concrete, pipes and fins, as well as the cost of the basic platform and insulation materials of the energy storage system module, namely:

The installation cost of concrete energy storage system is calculated based on 20% of the total material cost and indirect cost, as shown in the following equation:

The cost data of each material in the cost calculation of the concrete energy storage system module are shown in Table 3. Based on the data in the table, the energy storage cost under certain energy storage conditions can be calculated.
Material | Cost |
Concrete ($/kg) | 0.100 |
Stainless steel ($/kg) | 5.430 |
External insulation material ($/m^2) | 235 |
Foam glass insulation board ($/m^3) | 356 |
3. Filling bed energy storage system
(1) Phase change packed bed energy storage system
The phase change packed bed energy storage system uses encapsulated phase change materials as the heat storage medium and molten salt as the heat transfer fluid. The encapsulated phase change material particles are stacked in the tank, and there are gaps between the particles. The gaps are filled with molten salt, which flows and exchanges heat from the gaps. The total cost of phase change packed bed energy storage system can be divided into direct cost and indirect cost. The direct costs mainly include the cost of thermal storage media, the cost of tank containers, and the cost of phase change material packaging. Indirect costs mainly include the cost of supporting pipelines, valves, and accessories, generally calculated as a certain percentage of direct costs.
The cost of energy storage media in direct costs mainly includes the cost of phase change materials and the cost of molten salt fluids. The calculation method is as follows:

Among them, is the cost of the energy storage medium, $; cm is the density of phase change materials, kg/m ^ 3
; is the porosity of the unit in the packed bed energy storage system,%; ′ cm is the unit mass cost of phase change materials, $/kg; ol is the density of the molten salt fluid, kg/m ^ 3; ol is the unit mass cost of molten salt, $/kg.
From the bottom up, the tank foundation consists of a concrete platform, insulated concrete slab, insulation materials, and insulated refractory bricks. The cost of tank containers mainly includes the cost of stainless steel tanks, the cost of basic platforms, and the cost of external insulation materials. The main calculation methods are as follows:

The packaging cost of phase change materials is usually calculated using the unit mass packaging material cost, expressed by the following formula:

Among them, nc is the unit mass packaging cost of phase change materials, $/kg; cm is the radius of the phase change material, m; ′ nc is the unit cost per kilogram of phase change material encapsulated in a capsule with a radius of 0.005m, $/kg. The packaging cost of phase change materials increases with the increase of radius, as larger radii require higher heat treatment and processing costs. At the same time, due to the buoyancy effect, natural convection will occur inside the phase change material after melting in a larger packaging space, which requires a higher thickness of the packaging material.
The indirect cost of the phase change packed bed energy storage system is calculated at 10% of the total cost of the energy storage medium, tank container, and packaging. The installation cost of the energy storage system is calculated at 20% of the total cost of the energy storage medium, tank container, packaging, and indirect costs. The cost data of phase change materials and molten salts used in the cost calculation of phase change packed bed energy storage system are shown in Table 4.
Materials | Cost |
Low temperature PCM ($/kg) | 0.210 |
Medium temperature PCM ($/kg) | 0.270 |
High temperature PCM ($/kg) | 2.000 |
Unit mass packaging cost 𝐶* enc ($/kg) | 0.750 |
Molten salt ($/kg) | 0.717 |
Stainless steel ($/kg) | 5.430 |
Thermal insulation material ($/m ^ 2) | 235 |
Basic Platform ($/m ^ 2) | 1210 |
(2) Sensible latent heat packed bed energy storage system
Due to the relatively high cost of phase change materials, using concrete to partially replace the phase change materials in the unit of the phase change packed bed energy storage system is a way to reduce the cost of energy storage media. Solid filling materials are arranged in the middle of the tank, and high-temperature and low-temperature phase change materials are placed at the top and bottom of the tank, respectively, forming a packed bed energy storage system with a combination of sensible and latent heat. It has the same cost composition as the phase change packed bed energy storage system, but there are differences in the cost of energy storage media. The cost expression for energy storage media can be expressed as follows:

Among them, cm is the volume percentage of each layer of phase change material in the tank body.
At the same time, due to the reduction in the use of phase change materials, the corresponding packaging costs of phase change materials are also reduced, which also saves system investment costs. However, due to the relatively low energy density of solid filling materials, the energy storage density per unit volume of the energy storage system is reduced. Based on the different volume ratios of solid filling materials in the energy storage system, calculate the thermal storage performance of the energy storage unit and the cost of the energy storage system under different conditions, in order to select a more efficient combination.