As a researcher deeply immersed in the field of energy storage technologies, I have witnessed the transformative potential of solid-state batteries (SSBs) in addressing the critical limitations of conventional lithium-ion batteries (LIBs). This article synthesizes recent breakthroughs, persistent challenges, and future trajectories in solid-state battery electrolyte development, emphasizing material innovation, interfacial engineering, and scalable manufacturing. Through rigorous analysis, comparative tables, and theoretical models, I aim to elucidate the path toward realizing SSBs with energy densities exceeding 500 Wh/kg and costs below $100/kWh by 2030.
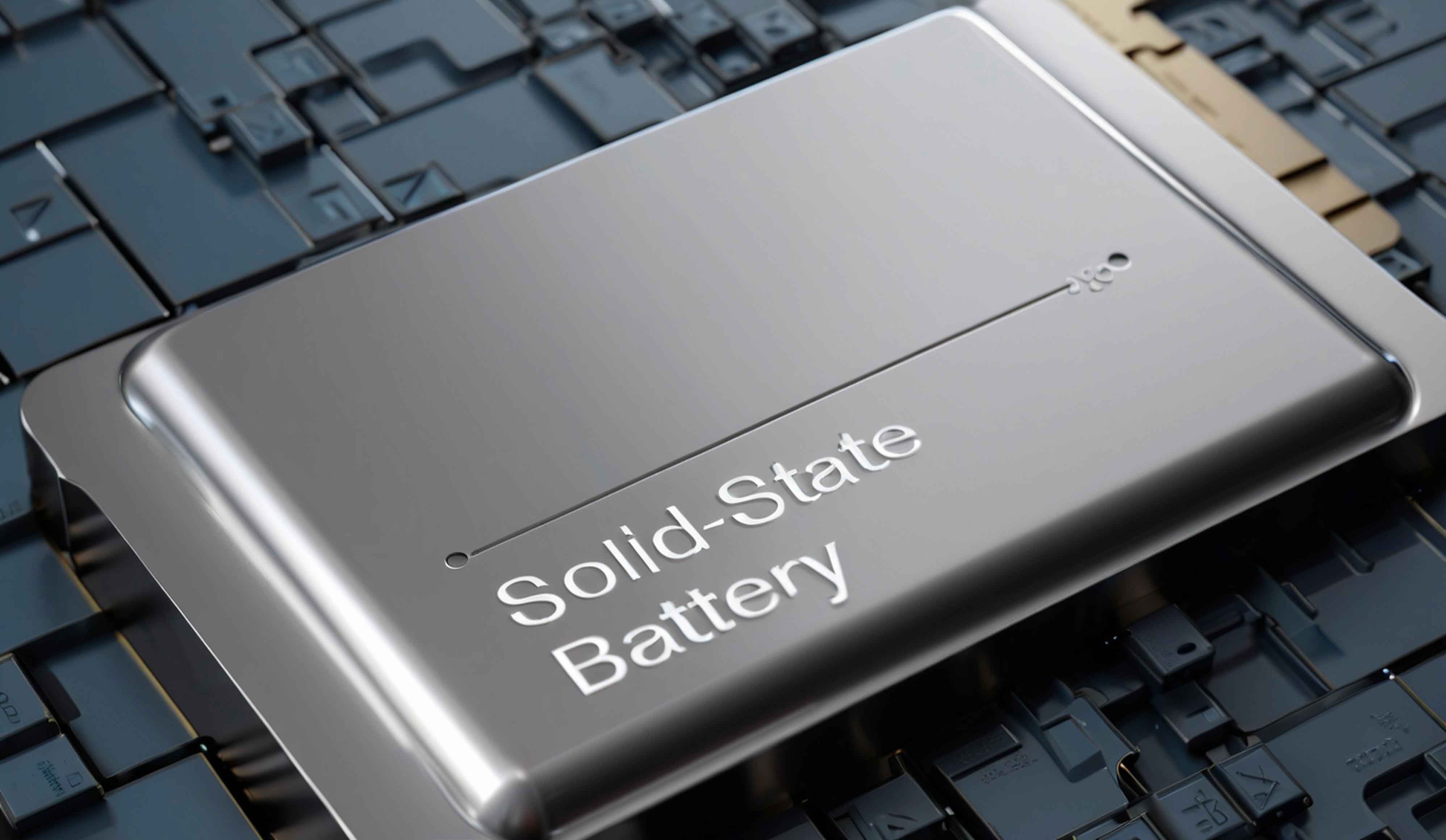
1. The Imperative for Solid-State Battery Electrolytes
1.1 Limitations of Conventional Lithium-Ion Batteries
Despite their dominance in portable electronics and electric vehicles (EVs), LIBs face intrinsic limitations:
- Energy Density Ceiling: Graphite anodes (372 mAh/g) and liquid electrolytes restrict energy densities to ~300 Wh/kg, far below the 500+ Wh/kg required for next-gen EVs.
- Safety Risks: Dendrite formation in liquid electrolytes causes thermal runaway, with decomposition temperatures <200°C, leading to catastrophic failures.
- Temperature Sensitivity: Performance degrades significantly below -20°C or above 60°C, limiting applications in extreme environments.
1.2 Policy-Driven Momentum
Global initiatives underscore the urgency of SSB development:
- China’s “Dual Carbon” Policy: Targets 400 Wh/kg batteries by 2025, prioritizing SSB R&D.
- EU’s “Battery 2030+”: Allocates €3.2 billion to achieve 500 Wh/kg SSBs by 2030.
- U.S. DOE’s “Battery500 Consortium”: Funds $250 million to develop lithium-metal/SSE systems.
1.3 Advantages of Solid-State Electrolytes
Solid-state electrolytes (SSEs) offer paradigm-shifting benefits:
- Safety: Non-flammable SSEs (thermal stability >500°C) suppress dendrites via mechanical rigidity (shear modulus >5 GPa).
- Energy Density: Coupling lithium-metal anodes (3860 mAh/g) with high-voltage cathodes (e.g., NCM811) enables theoretical energy densities >900 Wh/kg.
- Environmental Robustness: Stable performance across -30°C to 150°C suits aerospace and grid storage.
2. Classification of Solid-State Electrolytes and Key Challenges
2.1 Inorganic Solid Electrolytes
Inorganic SSEs dominate due to high ionic conductivity (σLi+σLi+) and chemical stability. Key categories include oxides, sulfides, and halides.
Table 1: Comparative Analysis of Inorganic SSEs
Property | Oxide SSEs (e.g., LLZO) | Sulfide SSEs (e.g., Li10GeP2S12Li10GeP2S12) | Halide SSEs (e.g., Li3InCl6Li3InCl6) |
---|---|---|---|
σLi+σLi+ (S/cm) | 10−4−10−310−4−10−3 | >10−3>10−3 | >10−3>10−3 |
Thermal Stability (°C) | >800 | 300–500 | >400 |
Air Stability | Excellent | Poor (generates H2SH2S) | Poor (hygroscopic) |
Cost ($/kg) | 100–200 | 400–600 | 200–300 |
Key Challenge | Poor interfacial contact | Air sensitivity, high cost | Moisture degradation |
Oxide SSEs: NASICON-type (Li1+xAlxTi2−x(PO4)3Li1+xAlxTi2−x(PO4)3) and garnet-type (Li7La3Zr2O12Li7La3Zr2O12) materials suffer from high sintering temperatures (>1000°C) and interfacial impedance. Strategies like co-sintering and buffer layers (e.g., Li3PO4Li3PO4) reduce interfacial resistance (RintRint) from 120 Ω·cm² to 25 Ω·cm².
Sulfide SSEs: Despite ultrahigh σLi+σLi+, their air sensitivity necessitates inert-atmosphere processing. Doping with Sn or Br enhances stability, as shown in Li9.54Si1.74P1.44S11.7Cl0.3Li9.54Si1.74P1.44S11.7Cl0.3, achieving 48-hour air stability at <10% humidity.
Halide SSEs: Li3InCl6Li3InCl6 combines wide electrochemical windows (>5 V vs. Li/Li++) and σLi+=1.49×10−3σLi+=1.49×10−3 S/cm. However, moisture exposure degrades conductivity by 50% within 1 hour. Zn coatings mitigate Li-metal incompatibility, reducing interfacial impedance to 12 Ω·cm².
2.2 Polymer and Composite Electrolytes
Polymer SSEs (e.g., PEO-LiTFSI) offer flexibility but suffer from low σLi+σLi+ (<10−4−4 S/cm at 25°C). Composite SSEs blend polymers with inorganic fillers (e.g., LLZO, Al2O3Al2O3) to enhance conductivity and mechanical strength:σcomposite=ϕfiller⋅σfiller+(1−ϕfiller)⋅σpolymerσcomposite=ϕfiller⋅σfiller+(1−ϕfiller)⋅σpolymer
where ϕfillerϕfiller is the volume fraction of filler. For example, SiO2@PEGSiO2@PEG-reinforced composites achieve σLi+=3.2×10−4σLi+=3.2×10−4 S/cm and 30% longer cycle life.
3. Critical Challenges and Mitigation Strategies
3.1 Enhancing Ionic Conductivity
Ionic transport in SSEs is hindered by grain-boundary resistance (oxides) or sluggish chain dynamics (polymers). Key advancements include:
- Doping: Mg-doped ZnO increases Li++ mobility by modulating bandgap energy (EgEg):Eg=Egundoped−α⋅xMgEg=Egundoped−α⋅xMgwhere αα is the bowing coefficient and xMgxMg is the dopant concentration.
- 3D-Printed Architectures: Porous LLZO scaffolds reduce Li++ diffusion paths by 40%, lowering RgrainRgrain.
3.2 Dendrite Suppression
Dendrite penetration remains a critical failure mode. Solutions include:
- Mechanical Blocking: High-modulus sulfides (G>6G>6 GPa) physically inhibit dendrites.
- Electrochemical Stabilization: Li3PO4Li3PO4-coated LLZO lowers electronic conductivity to 10−1010−10 S/cm, raising critical current density (JcritJcrit) to 2.5 mA/cm².
3.3 Interfacial Engineering
Solid-solid interfaces contribute >70% of total impedance. Innovations include:
- In Situ Polymerization: Liquid precursors (e.g., PEGDA) form conformal coatings, reducing RintRint by 60%.
- ALD Nanocoating: Sub-nm Al2O3Al2O3 layers on NCM811 cathodes enable stable cycling at 4.3 V.
3.4 Cost and Scalability
SSE manufacturing costs are prohibitive due to high-temperature sintering (oxides) or inert-atmosphere processing (sulfides). Breakthroughs include:
- Sn-Substituted Sulfides: Li8.5Sn0.5P1.5S11Br0.5Li8.5Sn0.5P1.5S11Br0.5 reduces raw material costs by 30%.
- Cold Sintering: LLZO films sintered at 800°C (vs. 1200°C) cut energy use by 50%.
4. Future Directions and Industry Outlook
4.1 Material Innovation
- Halide SSEs: Developing moisture-resistant variants (e.g., Li3YCl6Li3YCl6) with σLi+>10−2σLi+>10−2 S/cm.
- Low-Cost Sulfides: Scaling argyrodite synthesis via mechanochemical routes.
4.2 Process Optimization
- Dry Electrode Manufacturing: Eliminates solvent use, reducing energy consumption to <1 kWh/kg.
- Roll-to-Roll Production: Pilot lines (e.g., CATL) target 1 GWh/year capacity with 40% cost reduction.
4.3 System Integration
- Thermal Management: Phase-change materials (PCMs) maintain optimal operating temperatures.
- Standardized Testing: Protocols for JcritJcrit, RintRint, and cycle life under extreme conditions.
4.4 Market Projections
By 2030, SSBs are projected to achieve:
- Energy density: ≥500 Wh/kg
- Cost: <$100/kWh
- Cycle life: >1000 cycles
5. Conclusion
Solid-state batteries represent the vanguard of energy storage technology, poised to overcome the safety and energy density limitations of conventional LIBs. While challenges in ionic conductivity, interfacial stability, and scalable manufacturing persist, synergistic advances in material science, process engineering, and system design are accelerating commercialization. As global investments align with decarbonization goals, SSBs will catalyze the transition to high-performance EVs, resilient grids, and sustainable energy systems. The journey from lab-scale innovation to GWh-scale production demands relentless collaboration across academia, industry, and policymakers—a challenge I am committed to advancing in my research.