Introduction
The development of solid-state battery represents a transformative leap in energy storage technology, offering enhanced safety, higher energy density, and improved cycle life compared to conventional lithium-ion batteries. A critical component enabling this advancement is the solid electrolyte, with sulfide-based materials emerging as a leading candidate due to their high room-temperature ionic conductivity (>10⁻³ S·cm⁻¹) and mechanical flexibility. Traditional synthesis methods such as solid-state sintering and ball milling, while effective, suffer from high energy consumption, prolonged processing times, and limited control over particle morphology. In contrast, liquid-phase synthesis has gained prominence for its scalability, reduced synthesis temperatures, and precise control over electrolyte microstructure. This article explores the progress in liquid-phase synthesis of sulfide solid electrolytes, their structural and ionic transport mechanisms, solvent effects, and applications in solid-state battery.
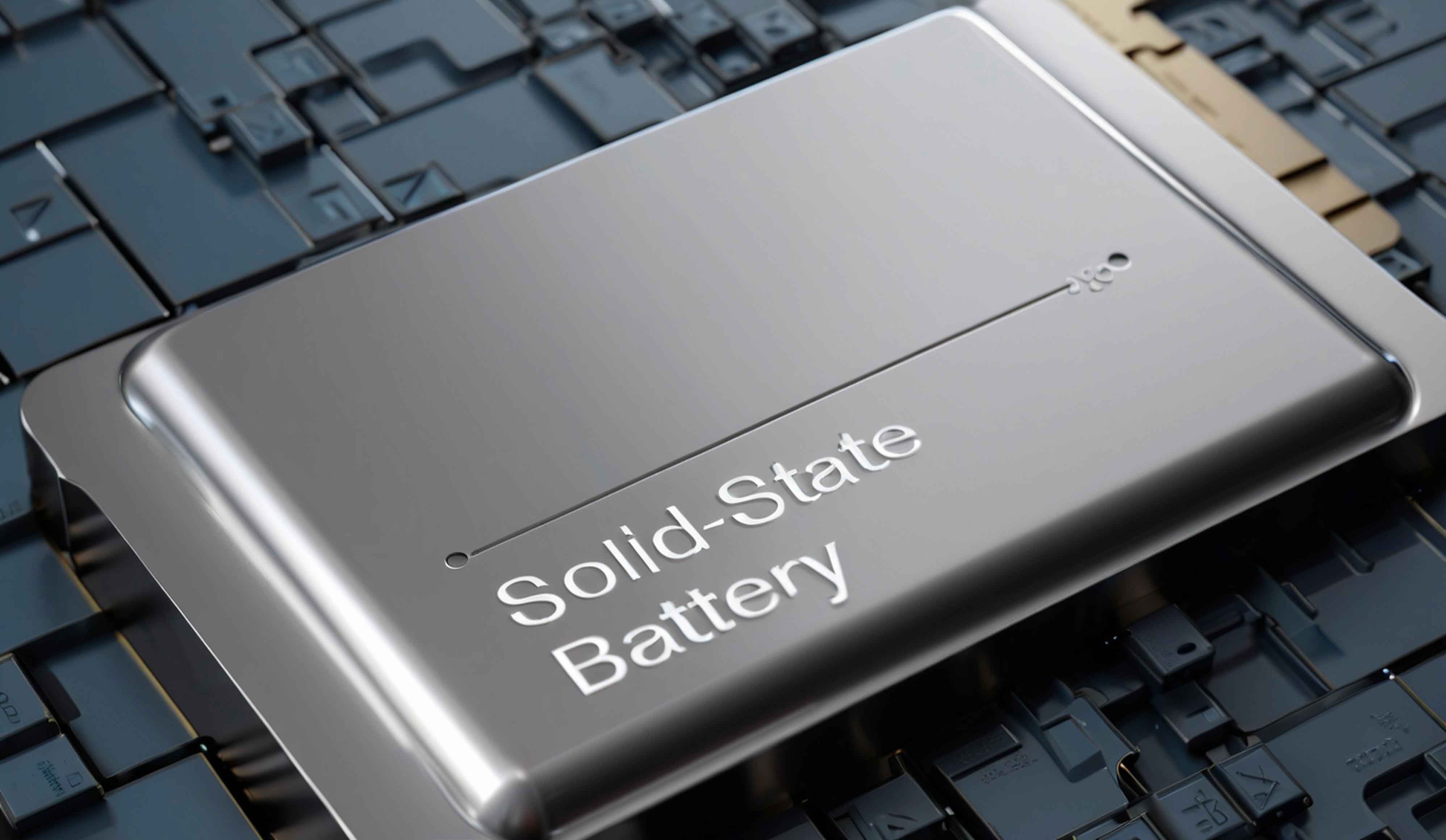
Crystal Structures and Ionic Transport Mechanisms
Sulfide solid electrolytes are categorized into binary (e.g., Li₂S-P₂S₅), ternary (e.g., Li₁₀GeP₂S₁₂), and argyrodite-type (e.g., Li₆PS₅X, X = Cl, Br, I) systems. Their ionic conductivity arises from unique crystal frameworks that facilitate Li⁺ migration.
1. Li₂S-P₂S₅ Binary Systems
The Li₂S-P₂S₅ system forms structures dominated by PS₄³⁻, P₂S₇⁴⁻, and other anionic groups. For instance, Li₇P₃S₁₁ (70Li₂S-30P₂S₅) exhibits a 3D Li⁺ diffusion network with ionic conductivity up to 1.7 × 10⁻² S·cm⁻¹. The β-phase of Li₃PS₄ (75Li₂S-25P₂S₅) achieves 5.09 × 10⁻⁴ S·cm⁻¹ via zigzag LiS₆ octahedral chains.
2. Li₁₀GeP₂S₁₂ (LGPS)
LGPS adopts a tetragonal structure with interconnected (Ge/P)S₄ tetrahedra and LiS₆ octahedra, enabling rapid Li⁺ transport along the c-axis. Its ionic conductivity reaches 1.2 × 10⁻² S·cm⁻¹, rivaling liquid electrolytes.
3. Li₆PS₅X Argyrodites
Argyrodite-type electrolytes feature cubic frameworks where halogen (X⁻) substitution induces lattice disorder, enhancing Li⁺ mobility. For example, Li₆PS₅Cl achieves 1.3 × 10⁻³ S·cm⁻¹ through inter-cage Li⁺ hopping .
Table 1: Ionic Conductivity of Key Sulfide Electrolytes
Electrolyte | Composition | Ionic Conductivity (S·cm⁻¹) |
---|---|---|
Li₇P₃S₁₁ | 70Li₂S-30P₂S₅ | 1.7 × 10⁻² |
β-Li₃PS₄ | 75Li₂S-25P₂S₅ | 5.09 × 10⁻⁴ |
Li₁₀GeP₂S₁₂ | Li-Ge-P-S | 1.2 × 10⁻² |
Li₆PS₅Cl | Li-P-S-Cl | 1.3 × 10⁻³ |
Liquid-Phase Synthesis Strategies
Liquid-phase methods are classified into three types based on reagent solubility: suspension, solution, and mixed approaches.
1. Suspension-Type Synthesis
Insoluble precursors (e.g., Li₂S, P₂S₅) are dispersed in solvents like tetrahydrofuran (THF) or acetonitrile (ACN). Stirring promotes reactions such as:Li2S+P2S5→ACNLi3PS4⋅nACN→Δβ-Li3PS4Li2S+P2S5ACNLi3PS4⋅nACNΔβ-Li3PS4
Key advantages include nanoscale particle formation (<500 nm) and reduced sintering temperatures. However, residual solvents may introduce impurities.
2. Solution-Type Synthesis
Fully dissolved precursors enable atomic-level mixing. Ethanol (EtOH) and ethylenediamine (EDA) dissolve Li₃PS₄ or LiX (X = Cl, Br), facilitating reactions like:Li3PS4+LiCl→EtOHLi6PS5ClLi3PS4+LiClEtOHLi6PS5Cl
This method achieves high purity but struggles with solvent removal, often leaving carbon residues.
3. Mixed-Type Synthesis
Partial dissolution of precursors balances reactivity and scalability. For example, Li₂S and LiCl dissolve in ethyl acetate (EA), while P₂S₅ remains suspended:Li2S+P2S5+LiCl→EALi6PS5ClLi2S+P2S5+LiClEALi6PS5Cl
Mechanical agitation or ultrasonic treatment accelerates reaction kinetics.
Table 2: Solvent Effects on Electrolyte Properties
Solvent | Boiling Point (°C) | Polarity (δₚ) | Ionic Conductivity (S·cm⁻¹) |
---|---|---|---|
THF | 66 | 4.0 | 1.6 × 10⁻⁴ |
ACN | 82 | 5.8 | 1.0 × 10⁻³ |
EtOH | 78 | 4.3 | 2.0 × 10⁻⁴ |
EA | 77 | 4.4 | 1.1 × 10⁻³ |
Solvent Influence on Electrolyte Performance
1. Purity and Carbon Residues
High-boiling solvents like EDA leave carbonaceous residues (~2.5 wt%) after thermal treatment, degrading ionic conductivity. Low-polarity solvents (e.g., ACN) minimize side reactions but require stringent drying.
2. Morphology Control
Solvent polarity dictates nucleation rates and particle morphology. Polar solvents (ACN, EtOH) favor nanoscale particles (<100 nm), while nonpolar solvents yield irregular aggregates.
3. Crystallinity
Crystallinity correlates with solvent polarity:Crystallinity∝δpCrystallinity∝δp
For instance, ACN (δₚ = 5.8) produces highly crystalline Li₃PS₄, whereas THF (δₚ = 4.0) results in amorphous phases.
Applications in Solid-State Batteries
Liquid-phase synthesis enables innovative electrode-electrolyte architectures critical for solid-state battery performance.
1. Electrolyte-Coated Active Materials
Li₆PS₅Cl dissolved in ethanol forms conformal coatings on LiCoO₂, reducing interfacial resistance. Coated cathodes achieve 160 mAh·g⁻¹ at 0.1C, outperforming dry-mixed counterparts.
2. Composite Electrodes
In-situ growth of Li₇P₃S₁₁ on Co₉S₈ nanosheets creates a percolating ion-conducting network. The composite delivers 421 mAh·g⁻¹ after 1,000 cycles at 1.27 mA·cm⁻².
3. Porous Electrode Infiltration
Infusing Li₆PS₅Cl into mesoporous sulfur-carbon matrices enhances sulfur utilization, achieving >1,500 mAh·g⁻¹ in Li-S solid-state batteries.
4. Interfacial Engineering
Liquid-phase-derived Li₃PS₄-Li₂S-C composites homogenize ionic/electronic pathways, enabling 830 mAh·g⁻¹ at 50 mA·g⁻¹ in Li-S cells.
Table 3: Performance of Liquid-Phase Synthesized Electrolytes in Solid-State Batteries
Application | Electrolyte | Capacity (mAh·g⁻¹) | Cycle Stability |
---|---|---|---|
LiCoO₂ Coating | Li₆PS₅Cl | 160 (0.1C) | 80% after 100 cycles |
Co₉S₈ Nanocomposite | Li₇P₃S₁₁ | 421 (1.27 mA·cm⁻²) | 90% after 1,000 cycles |
Sulfur-Carbon Composite | Li₁₀GeP₂S₁₂ | 1,500 | 100% Coulombic efficiency |
Li₂S-OMC Composite | Li₆PS₅Cl | 1,083 (0.2C) | 70% after 200 cycles |
Challenges and Future Directions
Despite progress, liquid-phase synthesis faces hurdles:
- Reaction Mechanisms: Incomplete understanding of intermediate phases (e.g., Li₃PS₄·solvent complexes) limits process optimization.
- Scalability: Batch-to-batch variability arises from solvent purity and drying conditions.
- Environmental Impact: Toxic solvents (ACN, EDA) necessitate greener alternatives.
Future efforts should prioritize:
- Mechanistic Studies: In-situ XRD/Raman to track phase transformations.
- Solvent Design: Low-toxicity, high-volatility solvents (e.g., propylene carbonate).
- Advanced Characterization: Solid-state NMR and XPS to quantify interfacial reactions.
Conclusion
Liquid-phase synthesis has emerged as a cornerstone for producing high-performance sulfide solid electrolytes, enabling scalable fabrication of solid-state batteries with superior energy density and safety. By tailoring solvent properties and reaction conditions, researchers can overcome existing limitations and unlock the full potential of this transformative technology. As the demand for safer and more efficient energy storage grows, liquid-phase methods will play a pivotal role in advancing solid-state batteries toward commercialization.