Abstract
Lithium iron phosphate (LiFePO4) batteries are prone to thermal runaway when they fail, producing a large amount of combustible gas and potentially causing fire and explosion. The use of sensors to monitor the thermal runaway of batteries is an effective means to avoid the spread of energy storage battery accidents. In this study, we conducted experiments on thermal runaway monitoring of LiFePO4 batteries at different locations and evaluated the effectiveness of various sensors. Based on our findings, we propose detection thresholds and sensor spacing recommendations for thermal runaway and fire detection in LiFePO4 battery storage compartments.
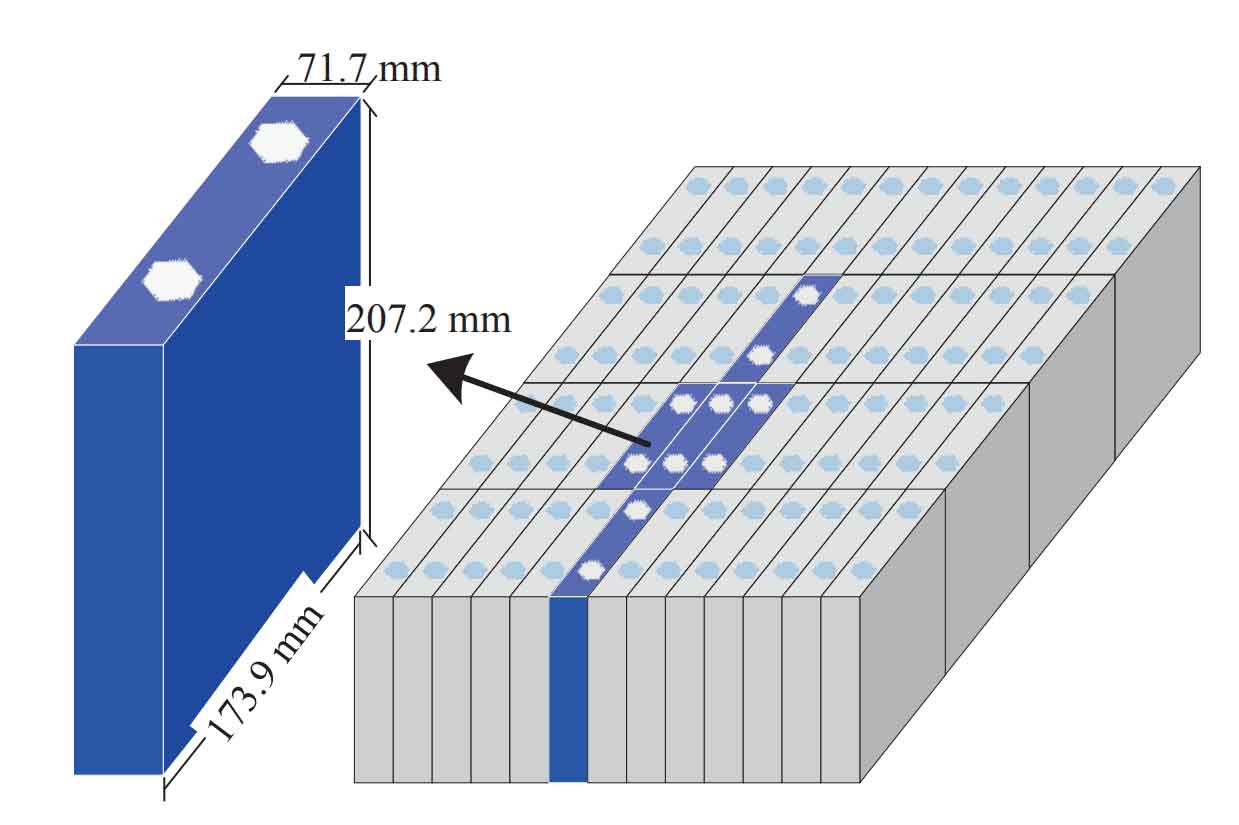
1. Introduction
The safety of LiFePO4 batteries in the field of energy storage is an urgent problem that needs to be solved both domestically and internationally. When a battery experiences thermal runaway, the battery casing deforms and ruptures due to increased internal pressure, causing the electrolyte to vaporize and leak. Simultaneously, the thermal runaway reaction inside the battery generates a significant amount of heat, gas, and smoke. The combustible substances in the gas and smoke can easily ignite and explode under high temperatures or electrical sparks. Timely monitoring of key parameters such as the volume fraction of characteristic gases, smoke mass fraction, temperature, and pressure using sensors, and issuing early warnings, is an effective means to prevent the spread of energy storage battery accidents.
2. Experimental Setup and Methods
We used a full-scale LiFePO4 battery storage compartment similar to real-world application conditions and designed five multi-function composite sensors covering different detection principles. These sensors included H2 sensors based on electrochemical, semiconductor, and catalytic combustion principles, as well as VOC sensors based on photoionization and solid-state polymer electrochemical principles. We evaluated the impact of different detection principles on H2 and VOC sensors, the influence of thermal runaway battery location, and the effect of ignition on battery thermal runaway gas characteristics.
3. Experimental Results and Analysis
3.1. Comparison of Sensor Response Times
Our experimental results showed that the catalytic combustion principle H2 sensor could detect H2 faster than the electrochemical principle sensor. Additionally, the photoionization VOC sensor had a similar detection time to the electrochemical H2 sensor, CO sensor, and electrochemical VOC sensor, all concentrating around the time of battery thermal runaway. These gas sensors are thus suitable for thermal runaway monitoring.
Table 1. Comparison of Sensor Response Times
Sensor Type | Detection Principle | Response Time (relative to thermal runaway) |
---|---|---|
H2 Sensor (Catalytic Combustion) | Catalytic Combustion | Faster than electrochemical |
H2 Sensor (Electrochemical) | Electrochemical | Later than catalytic combustion |
VOC Sensor (Photoionization) | Photoionization | Similar to electrochemical H2 sensor |
CO Sensor | Electrochemical | Similar to photoionization VOC sensor |
VOC Sensor (Electrochemical) | Solid-state Polymer | Similar to other sensors listed |
3.2. Influence of Ignition on Thermal Runaway Parameters
The peak concentrations of CO, smoke, CO2, and the rate of change in smoke temperature were significantly higher under ignition conditions compared to non-ignition conditions. Specifically, the peaks for CO, smoke, CO2 concentration, and the rate of change in smoke temperature were 2, 2, 4, and 8 times higher, respectively, under ignition conditions. This indicates that ignition significantly promotes the generation of these parameters.
Table 2. Comparison of Thermal Runaway Parameters Under Non-ignition and Ignition Conditions
Parameter | Non-ignition Peak Value | Ignition Peak Value | Ratio (Ignition/Non-ignition) |
---|---|---|---|
CO Concentration | Lower value | Higher value | 2x |
Smoke Concentration | Lower value | Higher value | 2x |
CO2 Concentration | Lower value | Higher value | 4x |
Rate of Temperature Change | Lower value | Higher value | 8x |
3.3. Propagation Velocity of Thermal Runaway Parameters
The propagation velocities of different thermal runaway parameters were higher under edge heating compared to central heating. Based on VOC gas propagation velocity, the suitable spacing for edge detectors in the storage compartment is 0.639-1.278 m, and for central detectors, it is 0.924-1.846 m. Compared to non-ignition conditions, under ignition conditions, the smoke temperature increase rate increased by 8 times, and thermal diffusion significantly increased the propagation rate of thermal runaway parameters, which is beneficial for thermal runaway monitoring and early warning.
Table 3. Propagation Rates of Thermal Runaway Parameters Under Different Conditions
Heating Location | Parameter | Propagation Velocity |
---|---|---|
Edge Heating | VOC Gas | Faster |
Central Heating | VOC Gas | Slower |
Edge Heating | Other Parameters (e.g., CO, Smoke) | Faster than Central Heating |
4. Discussion
Based on our experimental results, we propose the following strategies for LiFePO4 battery storage compartment thermal runaway monitoring and early warning:
- Sensor Selection: Catalytic combustion principle H2 sensors and photoionization VOC sensors have faster response times and are suitable for thermal runaway monitoring. CO2 sensors, although having a longer response time, have a longer lifespan and can be considered for long-term monitoring.
- Sensor Spacing: The suitable spacing for edge detectors is 0.639-1.278 m, and for central detectors, it is 0.924-1.846 m. This spacing ensures effective detection of thermal runaway parameters.
- Monitoring Parameters: In addition to H2 and VOC, parameters such as CO, smoke, and CO2 should also be monitored, as ignition significantly promotes their generation and can provide important information for early warning.
5. Conclusion
In this study, we evaluated the effectiveness of different sensors for LiFePO4 battery storage compartment thermal runaway monitoring and proposed detection thresholds and sensor spacing recommendations. Our findings have practical implications for sensor selection and placement in such compartments. Future research will explore sensor selection and placement in different environments and conduct iterative studies on composite sensor parameters.