Abstract This article focuses on the life cycle assessment of lithium-iron batteries (LiFePO4 batteries). It begins with an introduction to the background and importance of battery life cycle assessment in the context of the growing demand for clean energy and sustainable development. The research methods, including the selection of evaluation tools and the determination of system boundaries, are described. The article then presents a detailed analysis of the life cycle stages of LiFePO4 batteries, such as raw material acquisition, manufacturing, use, and recycling, with a focus on energy consumption and environmental impact. Through a comprehensive evaluation of multiple environmental impact indicators, strategies for reducing environmental impact and promoting sustainable development are proposed.
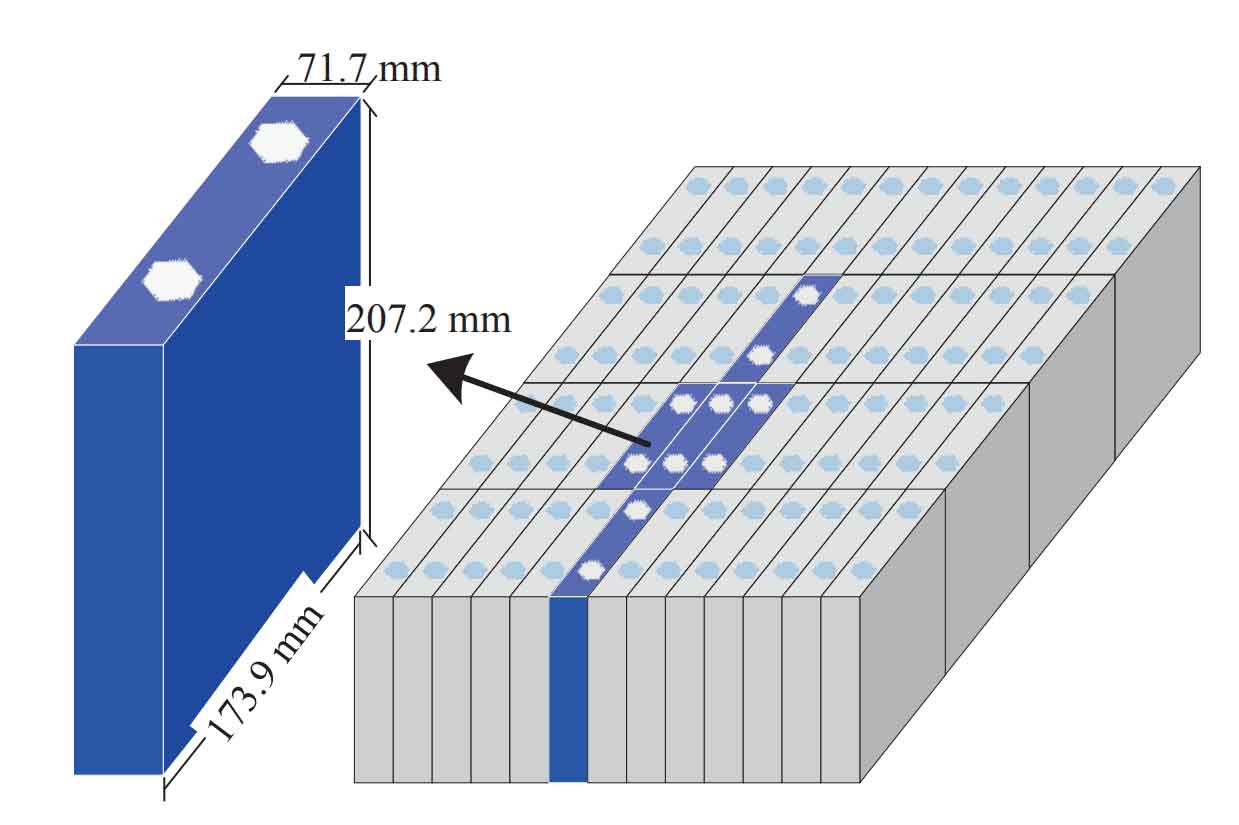
1. Introduction
In recent years, with the increasing concern about environmental protection and the pursuit of sustainable development, the development and application of clean energy technologies have become crucial. Electric vehicles, as an important means of reducing greenhouse gas emissions in the transportation sector, have received extensive attention. As the core component of electric vehicles, the performance and environmental impact of batteries have become key research topics. Among various battery types, lithium-iron batteries (LiFePO4 batteries) have shown many advantages, such as high safety, long cycle life, and good thermal stability. However, to comprehensively understand the environmental impact of LiFePO4 batteries, a life cycle assessment (LCA) is necessary.
The life cycle assessment can quantitatively analyze the environmental impact and energy consumption of a product from raw material acquisition, production and processing of components, product use, to end-of-life recycling. This method provides a scientific basis for evaluating the sustainability of products and formulating corresponding improvement strategies. In this article, we will conduct a detailed life cycle assessment of LiFePO4 batteries to explore ways to reduce their environmental impact and promote their sustainable development.
2. Research Methods
2.1 Evaluation Tools
The eFootprint online software system developed by Ecosystem Technologies Co., Ltd. is selected as the evaluation tool. This software is an online LCA data reporting and analysis platform that can complete a series of tasks such as supply chain data investigation, database integration, LCA modeling, calculation analysis, data quality assessment, and LCA result analysis based on the network.
2.2 System Boundaries
The research object is the LiFePO4 battery used in BYD pure electric vehicles. The system boundary includes four stages: raw material acquisition, manufacturing and assembly, use, and recycling. During the modeling process, some small components with little impact on the evaluation results are optimized to ensure the operability of the model.
3. Life Cycle Stages of LiFePO4 Batteries
3.1 Raw Material Acquisition
The raw materials for LiFePO4 batteries mainly include lithium carbonate, ferrous oxalate, graphite, etc. The acquisition of these raw materials involves various processes and energy consumption. For example, the production of lithium carbonate may require mining and refining processes, which consume a certain amount of energy and may have environmental impacts such as water pollution and land occupation. The acquisition of graphite may also involve mining and processing steps, with potential environmental issues such as dust emissions.
The consumption of raw materials and their upstream sources for a LiFePO4 battery are shown in Table 1.
Battery Component | Material | Consumption/kg | Consumption Type | Upstream Source Data |
---|---|---|---|---|
Negative | Graphite | 75.316 | Raw Material/Material | CLCD – China – ECER 0.8 |
Aluminum | 60.451 | Raw Material/Material | Ecoinvent 3.1.0 | |
Lithium Hexafluorophosphate | 4.856 | Raw Material/Material | CLCD – China – ECER 0.8 | |
Water | 1.338 | Raw Material/Material | CLCD – China – ECER 0.8 | |
Positive | LiFePO4 (Ferrous Oxalate) | 114.956 | Raw Material/Material | CLCD – China – ECER 0.8 |
Lithium Carbonate | 3.221 | Raw Material/Material | CLCD – China – ECER 0.8 | |
Bicarbonate Dihydrogen | 2.131 | Raw Material/Material | CLCD – China – ECER 0.8 | |
Electric Energy | Raw Material/Material | Ecoinvent 3.1.0 | ||
Carbon Black | Raw Material/Material | CLCD – China – ECER 0.8 | ||
Aluminum Foil | 98.109 | Raw Material/Material | CLCD – China – ECER 0.8 | |
PVDH | 5.054 | Raw Material/Material | Ecoinvent 3.1.0 | |
Lithium Carbonate | 3.221 | Raw Material/Material | CLCD – China – ECER 0.8 | |
Ferrous Oxalate | 2.131 | Raw Material/Material | CLCD – China – ECER 0.8 | |
Water | 1.635 | Raw Material/Material | CLCD – China – ECER 0.8 | |
Electrolyte | Lithium Hexafluorophosphate | 13.379 | Raw Material/Material | CLCD – China – ECER 0.8 |
Ethylene Carbonate | 38.649 | Raw Material/Material | Ecoinvent 3.1.0 | |
Dimethyl Ester | 38.649 | Raw Material/Material | Ecoinvent 3.1.0 | |
Separator | Polypropylene | 9.415 | Raw Material/Material | Ecoinvent 3.1.0 |
Polyethylene | 1.487 | Raw Material/Material | CLCD – China – ECER 0.8 | |
Shell | Polypropylene | 6.442 | Raw Material/Material | CLCD – China – ECER 0.8 |
Steel | 7.433 | Raw Material/Material | Ecoinvent 3.1.0 | |
Glass Fiber | 1.487 | Raw Material/Material | CLCD – China – ECER 0.8 | |
Coolant | Ethylene Glycol | 4.955 | Raw Material/Material | CLCD – China – ECER 0.8 |
3.2 Manufacturing and Assembly
The energy consumption in this stage has a significant impact on the overall life cycle assessment of the LiFePO4 battery. The manufacturing and assembly processes involve complex chemical reactions and mechanical operations. For example, in electrode preparation, precise control of the mixing ratio of materials and the coating process is required to ensure the performance of the electrodes. This requires a certain amount of energy input for heating, mixing, and drying.
Cell assembly involves the combination of electrodes, separators, and electrolytes. The precision of this process affects the safety and performance of the battery. The battery formation process is crucial for activating the battery and optimizing its electrochemical performance. This process typically requires a specific charging and discharging protocol, which consumes energy.
To further analyze the energy consumption in manufacturing and assembly, we can break it down by different components. The positive electrode, negative electrode, electrolyte, and separator all contribute to the overall energy consumption. The consumption of each component can be calculated based on its mass and the energy consumption per unit mass. This detailed analysis can help identify areas for potential energy savings and process improvements.
In addition to energy consumption, the manufacturing and assembly stage also has environmental impacts. The production of raw materials for the battery components may involve emissions of pollutants such as greenhouse gases, particulate matter, and toxic chemicals. The manufacturing processes may also generate waste materials, such as scraps of electrodes and packaging materials. These waste materials need to be properly managed to minimize their environmental impact.
Overall, the manufacturing and assembly stage of LiFePO4 batteries is a complex process with significant energy consumption and environmental impacts. Understanding these aspects is crucial for improving the sustainability of the battery life cycle. Future research and development efforts should focus on optimizing the manufacturing processes to reduce energy consumption and emissions, while maintaining or improving the performance of the batteries.