Abstract:
With the rapid growth of energy storage demand, large-capacity batteries have become the mainstream in electrochemical energy storage systems. However, the existing research on battery pack cooling systems primarily focuses on small-capacity battery systems. This paper investigates the submerged liquid cooling system for 280 Ah large-capacity battery packs. The effects of battery spacing, coolant inlet and outlet configurations, inlet flow rates, and coolant types on cooling performance are examined. Furthermore, the weights of coolant thermophysical parameters on the cooling effect are analyzed. The findings indicate that optimizing these parameters significantly enhances the cooling efficiency, providing valuable insights for the design of large-capacity battery pack immersion liquid cooling systems.
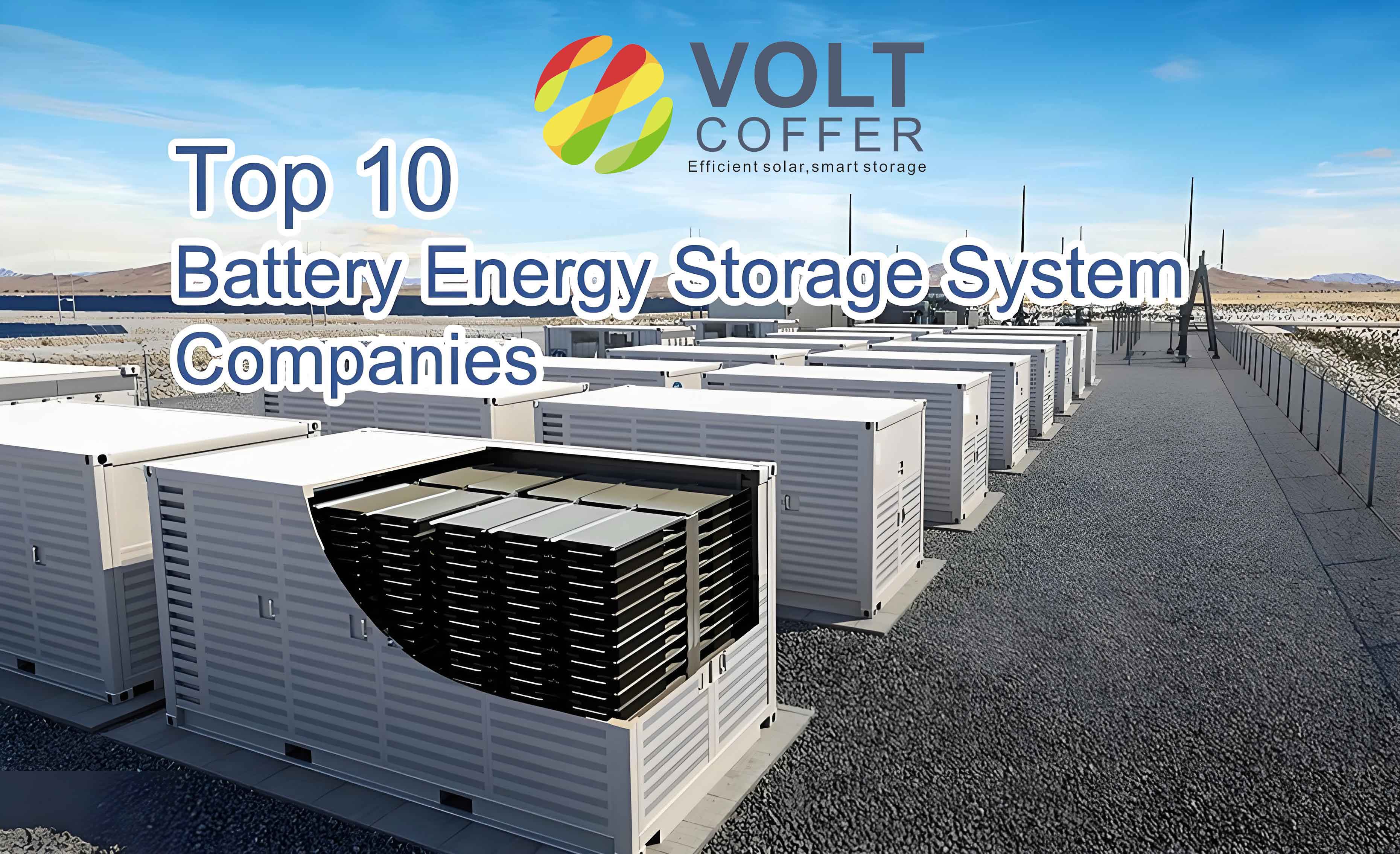
1. Introduction
The transition from fossil fuels to renewable energy sources is imperative to address global energy crises and environmental concerns. However, renewable sources like wind and solar power suffer from intermittency and unpredictability, posing challenges for grid stability and energy dispatch. Energy storage systems, especially electrochemical energy storage, play a crucial role in ensuring power grid reliability, flexibility, and low-carbon transformation [1]. Among various energy storage technologies, lithium-ion batteries are widely used due to their high energy density, long cycle life, and environmental friendliness [2].
Nevertheless, lithium-ion batteries generate significant heat during charging and discharging, requiring effective thermal management systems (TMS) to maintain optimal operating temperatures and temperature uniformity. Excessive temperatures or temperature gradients can lead to capacity fade, thermal runaway, and safety hazards [3]. This study focuses on the cooling performance of an immersion liquid cooling system designed specifically for large-capacity energy storage battery packs.
2. Literature Review
2.1 Overview of Battery Thermal Management Systems
Battery TMS can be broadly classified into three categories based on the heat transfer medium: air cooling, phase change material (PCM) cooling, and liquid cooling [4]. Air cooling, despite its simplicity and low cost, suffers from low thermal conductivity and specific heat capacity, limiting its effectiveness for high-power applications [5]. PCM cooling offers excellent temperature control and high heat dissipation capacity but is hindered by complex structures, poor mechanical properties, and high costs [6].
Liquid cooling, on the other hand, can be further divided into indirect (cold plate) and direct (immersion) cooling methods. Indirect liquid cooling employs a coolant circulating through a cold plate that removes heat from the battery pack. In contrast, direct liquid cooling, or immersion cooling, involves submerging the batteries in a dielectric fluid, offering superior heat transfer due to larger contact area and lower thermal resistance [7].
2.2 Immersion Liquid Cooling for Battery Packs
Immersion cooling has garnered significant interest due to its high efficiency and ability to suppress thermal runaway [8]. Previous studies have examined various aspects of immersion cooling, including cooling performance [9], battery pack configuration [10], and coolant flow characteristics [11]. However, most research focuses on small-capacity batteries used in electric vehicles, while limited attention has been paid to large-capacity batteries employed in energy storage systems [12].
3. Mathematical Modeling
3.1 Physical Model
The physical model of the immersion liquid cooling system for the 280 Ah lithium-ion battery pack. The battery pack consists of square prismatic LiFePO4 cells arranged in a 4×13 configuration. The coolant circulates through the battery enclosure driven by a pump, removing heat generated during battery operation and transferring it to a secondary cooling system.
3.2 Governing Equations
The battery heat generation is modeled using the Bernardi equation [13], which relates the volumetric heat generation rate (q_v) to battery current (I), internal resistance (R_t), and temperature-dependent open-circuit voltage (U_0). The heat transfer in the battery and coolant is governed by the following equations:
- Battery Energy Conservation Equation:rhobcb∂t∂Tb=∇⋅(λb∇Tb)+qvwhere ρb, cb, Tb, and λb are the battery density, specific heat capacity, temperature, and thermal conductivity, respectively.
- Coolant Continuity and Momentum Equations:frac∂ρ∂t+∇⋅(ρu)=0rho(∂t∂u+(u⋅∇)u)=−∇p+μ∇2u+ρgwhere ρ, u, p, μ, and g are the coolant density, velocity vector, pressure, dynamic viscosity, and gravitational acceleration vector, respectively.
- Coolant Energy Equation:rhocp∂t∂T+∇⋅(ρcpuT)=∇⋅(λ∇T)where cp and λ are the coolant specific heat capacity and thermal conductivity, respectively.
3.3 Boundary Conditions and Numerical Methods
The initial temperature of the battery and coolant is set to 25°C. The battery operates at a 1C discharge rate, and the coolant inlet is prescribed as a velocity inlet with a temperature of 25°C. The coolant outlet is modeled as a pressure outlet with an operating pressure of 101,325 Pa. A no-slip boundary condition is applied at all solid walls, and radiation heat transfer is neglected. The numerical simulations are performed using Fluent software, employing a pressure-based solver with a second-order upwind discretization scheme.
4. Results and Discussion
4.1 Effect of Battery Spacing
The influence of battery spacing (d_i) on cooling performance is evaluated by varying d_i from 0 to 10 mm. the maximum temperature difference (ΔT_max) and maximum temperature (T_max) initially decrease with increasing spacing up to 5 mm and then increase. At 0 mm spacing, the minimum coolant-battery contact area results in poor heat transfer. As spacing increases to 5 mm, the contact area improves, enhancing heat transfer. Beyond 5 mm, increased spacing reduces coolant velocity, offsetting the benefits of larger contact area.
4.2 Effect of Coolant Inlet and Outlet Configurations
Nine different inlet and outlet configurations are analyzed, as summarized in Table 1. The inlet position significantly affects ΔT_max and T_max compared to the outlet position. that the optimal cooling performance is achieved when the inlet is located at a medium height (102 mm). Lower inlets lead to coolant stagnation near the bottom, while higher inlets increase flow resistance.
Table 1: Coolant Inlet and Outlet Heights Relative to the Battery Case Bottom (mm)
Configuration | Inlet Height (mm) | Outlet Height (mm) |
---|---|---|
Case 1 | 182 | 182 |
Case 2 | 182 | 102 |
Case 3 | 182 | 20 |
… | … | … |
Case 9 | 20 | 20 |
4.3 Effect of Coolant Inlet Velocity
The coolant inlet velocity is varied from 0.2 to 1.6 m/s to assess its impact on cooling performance. both ΔT_max and T_max decrease with increasing velocity, although the rate of decrease diminishes at higher velocities. At low velocities (≤0.6 m/s), ΔT_max and T_max continue to rise during discharge, whereas they stabilize at higher velocities (≥0.8 m/s).
4.4 Effect of Coolant Type
Five different coolant types are evaluated: synthetic oil, MIVOLT-DF7, FC-72, deionized water, and silicone oil. As shown in Table 2, deionized water exhibits the best cooling performance due to its low viscosity and high thermal conductivity and specific heat capacity. In contrast, silicone oil performs the worst.
Table 2: Thermophysical Properties of Selected Coolants
Coolant | Viscosity (Pa·s) | Density (kg/m³) | Thermal Conductivity (W/(m·K)) | Specific Heat Capacity (J/(kg·K)) |
---|---|---|---|---|
Synthetic Oil | 0.0070 | 807 | 0.159 | 2523 |
MIVOLT-DF7 | 0.0150 | 916 | 0.129 | 1907 |
FC-72 | 0.0006 | 1680 | 0.057 | 1100 |
Deionized Water | 0.0010 | 998 | 0.598 | 4182 |
Silicone Oil | 0.0965 | 965 | 0.160 | 1460 |
4.5 Sensitivity Analysis of Coolant Thermophysical Properties
To quantify the influence of coolant thermophysical properties, sensitivity analyses are conducted by varying the density, specific heat capacity, thermal conductivity, and viscosity individually while keeping other properties constant. the density has the most significant impact on cooling performance, followed by specific heat capacity, thermal conductivity, and viscosity.
5. Conclusion
This study comprehensively investigates the cooling performance of an immersion liquid cooling system for a 280 Ah large-capacity energy storage battery pack. The effects of battery spacing, coolant inlet and outlet configurations, inlet velocity, and coolant type on cooling performance are analyzed. The key findings are summarized below:
- Battery Spacing: An optimal spacing of 5 mm maximizes cooling performance by balancing coolant-battery contact area and coolant velocity.
- Inlet and Outlet Configurations: The coolant inlet position significantly affects cooling performance, with a medium inlet height yielding the best results.
- Coolant Inlet Velocity: Increasing the inlet velocity improves cooling efficiency, but the marginal benefit diminishes at higher velocities.
- Coolant Type: Deionized water emerges as the most effective coolant due to its superior thermophysical properties.
- Sensitivity Analysis: The density of the coolant has the greatest influence on cooling performance, followed by specific heat capacity, thermal conductivity, and viscosity.
These insights provide valuable guidelines for the design and optimization of immersion liquid cooling systems for large-capacity energy storage battery packs, enhancing their safety, reliability, and operational life.