Abstract
Lithium iron phosphate (LFP) battery is widely used in electric vehicles (EVs) due to their high energy density, long cycle life, and environmental friendliness. However, their performance can be significantly influenced by temperature. This study investigates the effect of temperature on the charging and discharging cycle performance of LFP battery. Through experiments conducted under various temperature conditions, the study analyzes the impact of temperature on battery capacity, internal resistance, energy density, power density, cycle life, and electrolyte performance. The results indicate that the optimal working temperature range for LFP battery is 0-40°C, within which the batteries exhibit the best performance.
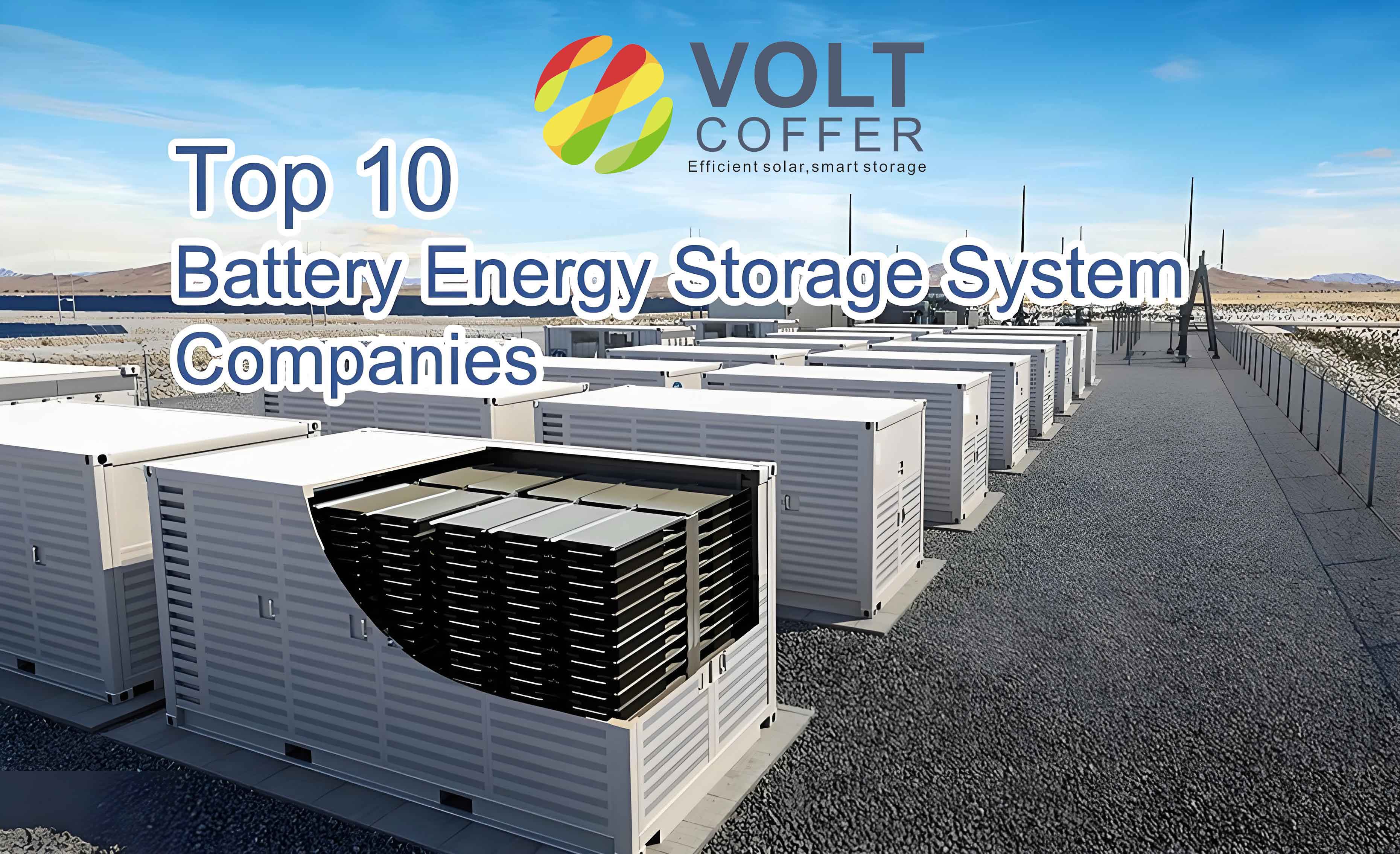
Introduction
With the increasing global demand for environmentally friendly and sustainable energy sources, electric vehicles (EVs) have become an attractive alternative to traditional gasoline-powered vehicles. As a core component of EVs, batteries play a crucial role in determining the performance, range, and overall user experience. Among various battery technologies, lithium iron phosphate (LFP) battery is widely used due to their advantages such as high energy density, long cycle life, and environmental friendliness .
However, the performance of LFP battery can be significantly influenced by various factors, one of which is temperature. Temperature affects the chemical reaction rates within the battery, thereby altering its key performance parameters such as capacity, internal resistance, energy density, and power density. High temperatures can accelerate the degradation of battery materials, while low temperatures can limit the ion mobility and reduce battery performance. Therefore, understanding the effect of temperature on the charging and discharging cycle performance of LFP battery is essential for optimizing battery design and improving EV performance.
This study aims to investigate the impact of temperature on the charging and discharging cycle performance of LFP battery for EVs. Experiments were conducted under various temperature conditions to analyze the effect of temperature on battery capacity, internal resistance, energy density, power density, cycle life, and electrolyte performance. The findings of this study provide valuable insights into the temperature-dependent performance of LFP battery and can inform the development of more efficient and reliable EV battery systems.
Experimental Design
Materials and Equipment
Materials
The materials used in this study are listed in Table 1.
Material | Specification | Manufacturer |
---|---|---|
PVDF | 1700 | Shanghai Wu Yu Chemical Co., Ltd. |
Lithium Iron Phosphate | M121 | Taiwan Lika Electric Energy Technology Co., Ltd. |
Separator | 40 μm | Nippon Kodoshi Corporation |
Conductive Agent | KS-6 | Zhuji Temaogao New Material Technology Co., Ltd. |
Graphite | Super-p | Zhuji Temaogao New Material Technology Co., Ltd. |
NMP | Electronic Grade | Henan Xingrun Chemical Co., Ltd. |
Equipment
The equipment used in this study is listed in Table 2.
Equipment | Manufacturer | Model |
---|---|---|
Slitting Machine | Xi’an Jieyun Technology Co., Ltd. | A191A |
Mixer | Guangzhou Hongyun Machinery Factory | DLH60L |
V-Type Blender | Guangzhou Hongyun Machinery Factory | HY-150L |
Filling Machine | Wuhan Chuyuan Digital Intelligence Technology Co., Ltd. | CY-JH300DP |
Roller Press | Shaoyang Dali Power Source Industry Co., Ltd. | DYG-703B |
Drying Oven | Ningbo Beite Measurement and Control Technology Co., Ltd. | BTS40050C1 |
Internal Resistance Tester | Chengdu Anbai Technology Co., Ltd. | AT520 |
Battery Charge/Discharge Tester | Beijing Tekcell International Trade Co., Ltd. | BT2000 |
Temperature-Controlled Chamber | Shanghai Jianheng Instrument Co., Ltd. | SDJ1006 |
Temperature Sensor | Jiumao Instrument (Tianchang) Co., Ltd. | JVMO-K |
Heating Element | Kunshan Reward Automation Co., Ltd. | IAHSF |
Cooling Fan | Suzhou Yefeng Electrical Appliance Co., Ltd. | 200FZY |
Microprocessor | Shenzhen Runbaixin Technology Co., Ltd. | MK10DN512VMC10 |
Scanning Electron Microscope | Beijing Chuangcheng Zhijia Technology Co., Ltd. | MultiSEM |
Battery Preparation
The LFP battery were prepared using the following steps:
- Preparation of Positive Electrode Material:
- Mix PVDF powder with NMP at 50°C until a uniform solution is formed.
- Weigh the required amounts of LFP powder, conductive agent, and PVDF solution according to the ratio 85:12.5:2.5.
- Mix these materials thoroughly using a V-type blender to ensure homogeneity.
- Preparation of Negative Electrode Material:
- Mix graphite with PVDF and coat the mixture onto a copper foil.
- Roll and slit the coated foil to obtain the negative electrode.
- Coating:
- Apply the positive electrode material onto a copper foil using a coater.
- Ensure even coating thickness and distribution.
- Drying and Sintering:
- Dry the coated electrodes in a drying oven to remove moisture and solvents.
- Sinter the electrodes to activate the LFP material and enhance adhesion.
- Cutting and Winding:
- Cut the dried and sintered electrodes to the desired dimensions.
- Wind the positive and negative electrodes together to form the battery cell.
- Electrolyte Injection and Sealing:
- Inject the appropriate amount of electrolyte into the battery cell.
- Seal the cell to prevent electrolyte leakage.
- Formation and Sorting:
- Activate the battery cell through formation charging.
- Sort and select cells based on performance criteria.
- Quality Inspection and Packaging:
- Perform comprehensive quality inspections, including capacity, internal resistance, and cycle life.
- Package the qualified batteries for final use.
Temperature Control Program
A temperature-controlled chamber was used to simulate various environmental temperatures during battery testing. The chamber consisted of a heating element, a cooling fan, a temperature sensor, and a microprocessor control unit. The microprocessor received temperature readings from the sensor and adjusted the heating and cooling elements to maintain the desired temperature within the chamber.
Microscopy Analysis
The morphology of the electrode materials was analyzed using a scanning electron microscope (SEM). Samples were prepared by cutting thin sections from the electrodes and mounting them on SEM stubs. The samples were then coated with a thin layer of gold to enhance conductivity and reduce charging effects during imaging. SEM images were captured at various magnifications to assess particle size, shape, and distribution.
Charging and Discharging Cycle Test
The charging and discharging cycle performance of the LFP battery was evaluated using a battery charge/discharge tester. The tester applied a constant current and constant voltage (CC-CV) charging profile followed by a constant current discharging profile. The charging current was set to 1C (2000 mA for a 2000 mAh battery), and the discharge current was also set to 1C. The charging voltage limit was set to 4.2 V.
The test procedure included the following steps:
- Initial Inspection: Visually inspect the batteries for any damage or defects.
- Initial Measurement: Measure the initial capacity and internal resistance of the batteries using the internal resistance tester and charge/discharge tester.
- Charging Cycle: Place the batteries in the temperature-controlled chamber and apply the CC-CV charging profile. Record voltage, current, and temperature data during charging.
- Discharging Cycle: Remove the batteries from the chamber and apply the constant current discharging profile. Record voltage, current, and temperature data during discharging.
- Data Analysis: Analyze the recorded data to calculate battery capacity, internal resistance, energy density, power density, and cycle life.
Results and Discussion
Microscopy Analysis
SEM images of the electrode materials under different temperature conditions. The images reveal distinct morphological differences between electrodes tested at low, optimal, and high temperatures.
At low temperatures, the electrode material exhibits cracks and roughness due to reduced ion diffusion rates and thermal contraction effects. At optimal temperatures, the material appears more uniform and dense, indicating improved ion mobility and reaction kinetics. At high temperatures, particle agglomeration becomes evident, potentially affecting material toughness and overall battery performance.
Effect of Temperature on Battery Capacity
The effect of temperature on battery capacity. The capacity initially increases with temperature, reaches a plateau within the optimal temperature range, and then decreases at higher temperatures.
At low temperatures (-20°C to 0°C), the capacity decreases significantly due to reduced ion mobility and increased polarization effects. At optimal temperatures (0°C to 40°C), the capacity remains relatively stable and close to the rated capacity. At high temperatures (40°C to 80°C), the capacity initially increases slightly due to enhanced ion mobility but then decreases due to accelerated material degradation.
Effect of Temperature on Internal Resistance
The effect of temperature on battery internal resistance. The internal resistance initially increases slightly at low temperatures and then decreases as the temperature increases.
At low temperatures, the internal resistance increases due to reduced electrolyte mobility and possible electrolyte solidification. As the temperature rises, the electrolyte becomes more mobile, reducing the internal resistance. At high temperatures, the internal resistance decreases further due to enhanced chemical reaction rates and electrolyte flow.
Effect of Temperature on Energy Density
The effect of temperature on battery energy density. The energy density decreases significantly at low temperatures and remains relatively stable within the optimal temperature range.
At low temperatures, reduced chemical reaction rates limit the utilization of active materials, leading to decreased energy density. Within the optimal temperature range, reaction rates increase, improving material utilization and energy density. At high temperatures, energy density decreases slightly due to potential material degradation and electrolyte evaporation.
Effect of Temperature on Power Density
The effect of temperature on battery power density. The power density decreases at low temperatures and increases within the optimal temperature range before declining at high temperatures.
At low temperatures, reduced ion mobility limits the rate of charge and discharge, reducing power density. Within the optimal temperature range, improved ion mobility enhances charge and discharge rates, increasing power density. At high temperatures, excessive chemical reaction rates may lead to material degradation and reduced power density.
Effect of Temperature on Cycle Life
The effect of temperature on battery cycle life. The cycle life initially increases with temperature and then decreases at higher temperatures.
At low temperatures, reduced charge and discharge efficiency accelerate battery aging and shorten cycle life. Within the optimal temperature range, batteries exhibit the longest cycle life due to improved performance and stability. At high temperatures, material degradation and electrolyte evaporation shorten cycle life.
Effect of Temperature on Electrolyte
The effect of temperature on battery electrolyte. The electrolyte viscosity increases at low temperatures, reducing ion mobility and conductivity.
At low temperatures, the electrolyte becomes viscous or partially solidified, limiting ion transport and battery performance. Within the optimal temperature range, the electrolyte remains fluid and conductive, supporting efficient battery operation. At high temperatures, the electrolyte may undergo thermal decomposition or evaporation, reducing battery performance and lifespan.
Conclusion
This study investigated the effect of temperature on the charging and discharging cycle performance of lithium iron phosphate (LFP) batteries for electric vehicles. Experiments were conducted under various temperature conditions to analyze the impact of temperature on battery capacity, internal resistance, energy density, power density, cycle life, and electrolyte performance.
The results indicate that LFP batteries exhibit optimal performance within the temperature range of 0-40°C. At lower temperatures, battery capacity, energy density, power density, and cycle life decrease due to reduced ion mobility and increased internal resistance. At higher temperatures, material degradation and electrolyte evaporation lead to performance degradation.
The findings of this study provide valuable insights into the temperature-dependent performance of LFP batteries and can inform the development of more efficient and reliable EV battery systems. Future work could focus on optimizing battery design and management strategies to mitigate the effects of temperature variation and enhance battery performance over a wider operating range.