Abstract
The growing demand for lithium-ion batteries (LIBs) has led to a significant increase in waste LIBs, particularly lithium iron phosphate (LFP) batteries. The recovery of valuable materials, such as iron and lithium, from LFP battery waste is crucial for sustainable development. This study proposes a novel process for the preparation of battery-grade iron phosphate from lithium extraction residue (LER) generated during LFP battery recycling. The process involves nitric acid leaching, methanol electrolysis reduction, hydrofluoric acid precipitation, and hydrogen peroxide oxidation. Under optimized conditions, the iron leaching rate reaches 93.4%, and the resulting iron phosphate product meets the requirements of the HG/T 4701-2021 standard for battery-grade iron phosphate. This study provides an effective solution for the utilization of LFP battery waste and promotes the circular economy of LIBs.
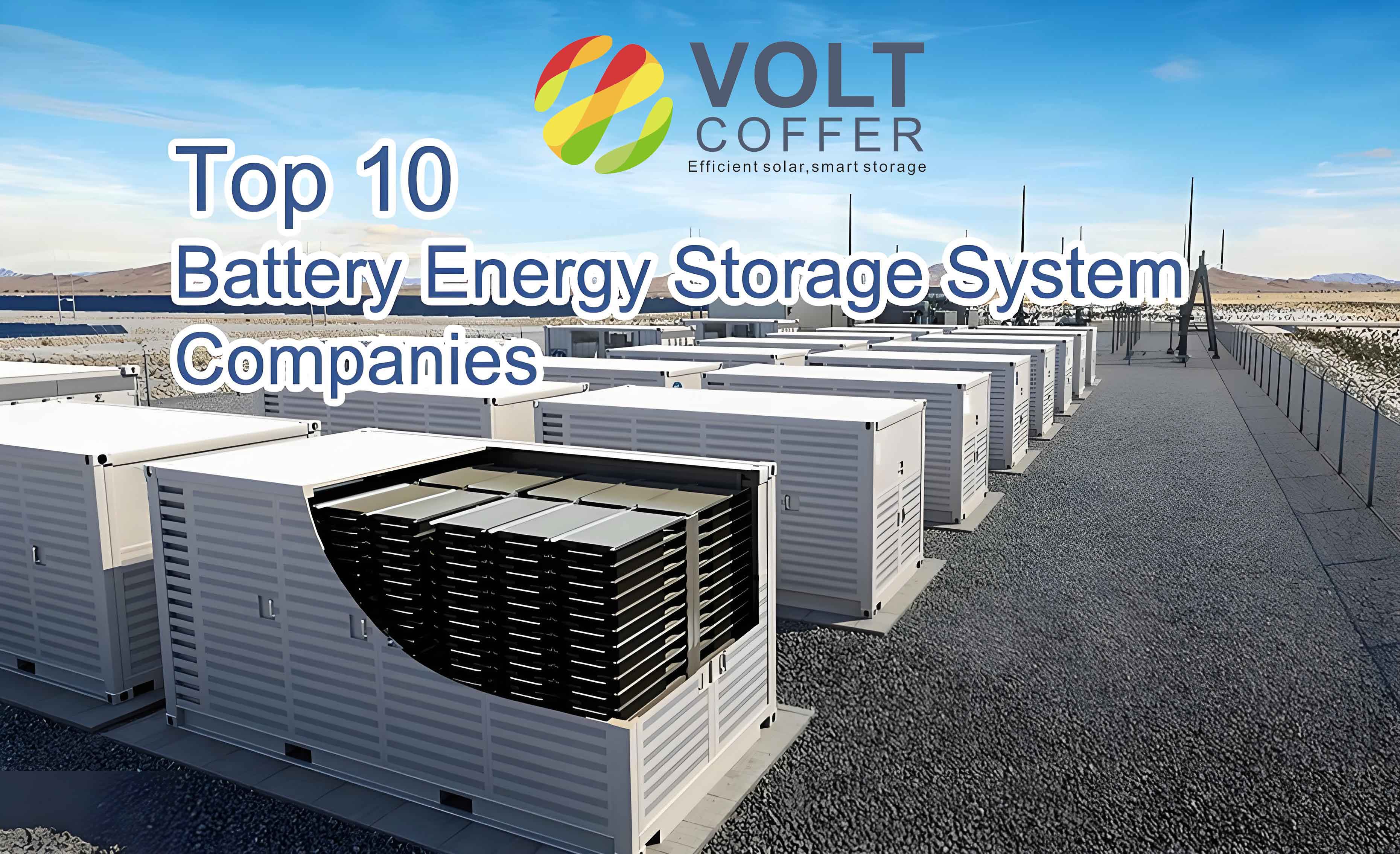
1. Introduction
The widespread adoption of electric vehicles (EVs) and portable electronic devices has driven a surge in demand for lithium-ion batteries (LIBs). Among various LIB chemistries, lithium iron phosphate (LFP) batteries have gained popularity due to their high safety, long cycle life, and environmental friendliness [1]. However, the disposal of end-of-life LFP batteries poses a significant challenge, especially considering the abundance of valuable materials within them, such as iron, lithium, and phosphorous.
Recycling LFP batteries involves various steps, including mechanical shredding, sieving, and chemical treatments. During the recycling process, lithium is typically extracted, leaving behind a waste stream known as lithium extraction residue (LER). This residue contains significant amounts of iron phosphate, which, due to the presence of impurities like aluminum, has traditionally been difficult to reuse [2]. This study aims to develop an innovative process for converting LER into battery-grade iron phosphate, thereby enhancing the circular economy of LIBs.
2. Materials and Methods
2.1 Materials
The following materials were used in this study:
- Lithium extraction residue (LER): Obtained from a commercial LFP battery recycling facility.
- Chemicals: Nitric acid (HNO₃), methanol (CH₃OH), hydrogen fluoride (HF), hydrogen peroxide (H₂O₂), formaldehyde (HCHO), deionized water.
2.2 Equipment
- ICP-OES (Inductively Coupled Plasma Optical Emission Spectrometry)
- SEM (Scanning Electron Microscope)
- X-ray diffraction (XRD)
- Electrochemical workstation
- Particle size analyzer
- Thermostat water bath
- Constant voltage/constant current power supply
- Magnetic stirrer
- High-temperature furnace
- Vacuum drying oven
- Rotary evaporator
- pH meter
- Analytical balance
2.3 Experimental Methodology
The process for preparing battery-grade iron phosphate from LER involves the following steps:
2.3.1 Pretreatment of LER
- Grind LER into a fine powder and sieve to obtain uniform particles.
- Ensure that each 100 g of pretreated LER contains approximately 0.3 mol of iron.
2.3.2 Nitric Acid Leaching
- Weigh 100 g of pretreated LER and mix with 75 g of nitric acid and 100 mL of deionized water.
- Heat the mixture to a predetermined temperature and maintain for a specified duration.
- Filter the solution to obtain the leachate, which contains dissolved iron ions.
2.3.3 Methanol Electrolysis Reduction
- Add 10 g of methanol to the leachate and heat to 50°C.
- Connect a direct current power supply and perform electrolysis at a current density of 5 A/cm² for 30 minutes.
- Electrolysis reduces iron (III) ions to iron (II) ions. Stop electrolysis when hydrogen evolution begins at the cathode.
2.3.4 Aluminum Removal
- Add 2 g of hydrofluoric acid to the leachate to precipitate aluminum as aluminum fluoride (AlF₃).
- Filter the solution to remove the AlF₃ precipitate.
2.3.5 Iron Phosphate Precipitation
- Oxidize iron (II) ions in the leachate to iron (III) ions by adding 12 g of H₂O₂.
- Add 8 g of formaldehyde to the solution and heat to 80°C while stirring until no more red-brown gas is released.
- Allow the solution to age for 30 minutes before filtering to obtain dihydrate iron phosphate (FePO₄·2H₂O) solids.
- Wash the solids thoroughly and dry in a vacuum oven at a constant temperature for 24 hours.
3. Results and Discussion
3.1 Effect of Reaction Time on Iron Leaching Rate
To optimize the nitric acid leaching process, experiments were conducted at various reaction times (20, 30, 40, 50, 60, 70, and 80 minutes) while keeping other conditions constant. The results are summarized in Table 1.
Table 1: Effect of Reaction Time on Iron Leaching Rate
Reaction Time (min) | Iron Leaching Rate (%) |
---|---|
20 | 75.7 |
30 | 88.1 |
40 | 93.5 |
50 | 93.8 |
60 | 94.1 |
70 | 94.1 |
80 | 94.1 |
The data indicate that the iron leaching rate increases significantly with reaction time up to 60 minutes, beyond which it plateaus. Therefore, 60 minutes was chosen as the optimal reaction time.
3.2 Effect of Reaction Temperature on Iron Leaching Rate
To further optimize the leaching process, experiments were conducted at various temperatures (20°C to 90°C) while maintaining a reaction time of 60 minutes. The results are shown in Table 2.
Table 2: Effect of Reaction Temperature on Iron Leaching Rate
Reaction Temperature (°C) | Iron Leaching Rate (%) |
---|---|
20 | 48.8 |
30 | 58.4 |
40 | 72.0 |
50 | 86.5 |
60 | 90.9 |
70 | 93.4 |
80 | 93.9 |
90 | 91.4 |
The iron leaching rate increases with temperature up to 70°C, beyond which it slightly decreases due to nitric acid volatilization. Therefore, 70°C was determined to be the optimal reaction temperature.
3.3 Characterization of the Prepared Iron Phosphate
3.3.1 Particle Size Analysis
The particle size distribution of the prepared iron phosphate was analyzed using a particle size analyzer. The results show that most particles have diameters ranging from 1 to 10 µm, indicating a narrow size distribution essential for consistent battery performance.
3.3.2 Scanning Electron Microscopy (SEM)
SEM images reveal the morphology of the prepared iron phosphate particles. The particles are well-defined and exhibit a smooth surface, indicating good crystallinity.
3.3.3 X-ray Diffraction (XRD)
XRD analysis confirms the phase purity of the prepared iron phosphate. The diffraction patterns match well with the standard pattern for monoclinic FePO₄·2H₂O (PDF#72-0471) and hexagonal FePO₄ (PDF#29-0715) after dehydration at 600°C.
3.3.4 Impurity Analysis
ICP-OES analysis was performed to determine the impurity levels in the prepared iron phosphate. The results (Table 3) show that aluminum content is significantly reduced to 72 mg/kg, meeting the requirements of HG/T 4701-2021 for battery-grade iron phosphate.
Table 3: Impurity Levels in Prepared Iron Phosphate
Element | Concentration (mg/kg) |
---|---|
Al | 72 |
Cu | 12 |
Ca | 22 |
Zn | 18 |
Mn | 125 |
Ti | 378 |
3.4 Electrochemical Performance
Although the primary focus of this study is on material preparation, preliminary electrochemical tests can provide insights into the potential performance of the prepared iron phosphate in batteries. Further research is needed to fully evaluate its suitability for LIB applications.
4. Conclusion
This study presents a novel process for converting LFP battery recycling waste (LER) into battery-grade iron phosphate. Through optimized nitric acid leaching, methanol electrolysis reduction, and hydrofluoric acid precipitation, high-purity iron phosphate was successfully prepared. The iron leaching rate reached 93.4% under optimal conditions (60 minutes at 70°C), and the resulting iron phosphate met the requirements of HG/T 4701-2021 for battery-grade material. This process not only contributes to the circular economy of LIBs but also promotes sustainable waste management practices.