As the demand for high-performance energy storage solutions grows, Lithium-Ion cells have become the preferred choice for a wide range of applications, from consumer electronics to electric vehicles and renewable energy systems. However, one of the critical challenges in optimizing Lithium-Ion cells for high-performance applications is effective thermal management. This article explores various thermal management solutions for Lithium-Ion cells, highlighting the importance of maintaining optimal temperature conditions to ensure safety, efficiency, and longevity.
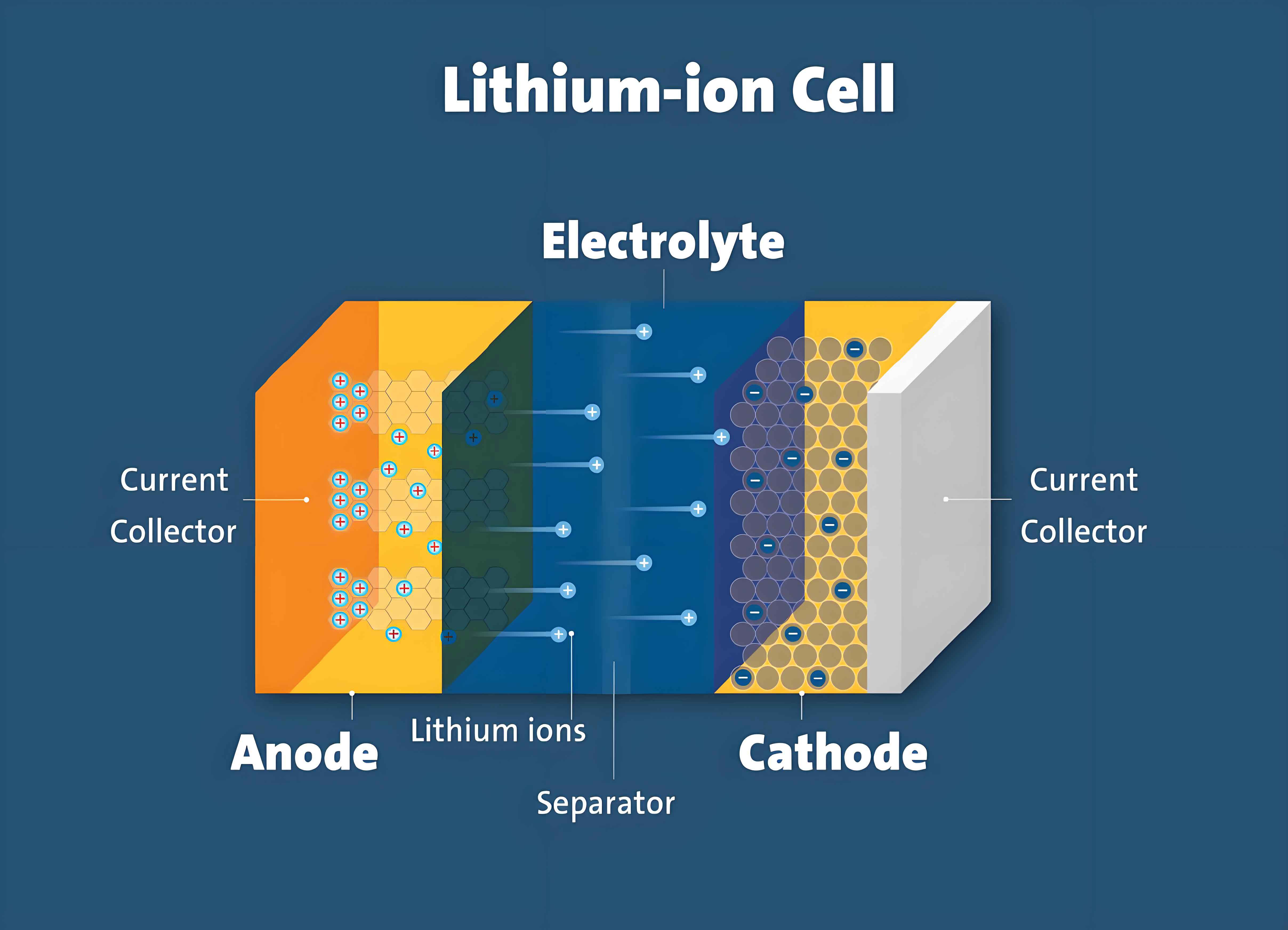
Importance of Thermal Management in Lithium-Ion Cells
Thermal management is crucial for the performance and safety of Lithium-Ion cells. Effective thermal management ensures that the cells operate within a safe temperature range, preventing overheating and thermal runaway, which can lead to cell damage, reduced efficiency, and safety hazards.
Key Objectives of Thermal Management:
- Maintain Optimal Operating Temperature: Ensuring that Lithium-Ion cells operate within the recommended temperature range to maximize efficiency and lifespan.
- Prevent Thermal Runaway: Avoiding the chain reaction that leads to rapid temperature increase and potential cell failure or fire.
- Enhance Performance: Improving the charge and discharge rates, energy density, and overall performance of Lithium-Ion cells through effective heat dissipation.
- Ensure Safety: Minimizing the risk of overheating, leakage, and other safety issues associated with high temperatures.
Thermal Management Solutions for Lithium-Ion Cells
Several thermal management solutions have been developed to address the challenges associated with heat generation and dissipation in Lithium-Ion cells. These solutions can be categorized into passive and active thermal management systems.
1. Passive Thermal Management
Passive thermal management solutions rely on materials and design strategies to dissipate heat without the need for external energy input.
Phase Change Materials (PCMs): PCMs absorb and release thermal energy during phase transitions (e.g., solid to liquid), helping to regulate temperature. They are often integrated into the cell packaging or placed between cells to absorb excess heat.
Thermal Interface Materials (TIMs): TIMs, such as thermal pastes and pads, enhance heat transfer between the cell and heat sinks or other cooling components. They fill air gaps and improve thermal conductivity.
Heat Sinks: Heat sinks are designed to increase the surface area for heat dissipation. They are often made of materials with high thermal conductivity, such as aluminum or copper, and are attached to the cell casing.
Cell Design Optimization: Optimizing the design of Lithium-Ion cells, such as electrode thickness, separator material, and cell geometry, can improve heat dissipation and thermal stability.
2. Active Thermal Management
Active thermal management solutions use external energy sources to actively control the temperature of Lithium-Ion cells.
Liquid Cooling Systems: Liquid cooling systems circulate a coolant fluid through channels or jackets around the cells. The fluid absorbs heat and carries it away from the cells, providing efficient and uniform cooling.
Air Cooling Systems: Air cooling systems use fans or blowers to force air over the surface of the cells, enhancing heat dissipation. This method is less efficient than liquid cooling but is simpler and cheaper to implement.
Thermoelectric Coolers (TECs): TECs use the Peltier effect to create a temperature difference by applying an electric current. They can be used to cool specific areas of a cell or battery pack, providing precise thermal management.
Active Heat Pipes: Active heat pipes use a working fluid that evaporates and condenses to transfer heat away from the cells. They provide efficient heat transfer and can be integrated into battery packs or modules.
Integrated Thermal Management Systems: Combining multiple thermal management techniques into an integrated system can provide comprehensive temperature control. For example, a combination of liquid cooling and PCM can enhance overall thermal performance.
Comparative Table of Thermal Management Solutions
Thermal Management Solution | Type | Benefits | Challenges |
---|---|---|---|
Phase Change Materials (PCMs) | Passive | Effective temperature regulation, no external energy needed | Limited thermal conductivity, cost |
Thermal Interface Materials (TIMs) | Passive | Improved heat transfer, easy to apply | Material degradation over time |
Heat Sinks | Passive | Increased surface area for heat dissipation | Added weight and space requirements |
Cell Design Optimization | Passive | Enhanced thermal stability, no additional components | Complex design and manufacturing |
Liquid Cooling Systems | Active | Efficient, uniform cooling, high heat capacity | Requires pumps, complex installation |
Air Cooling Systems | Active | Simple, cost-effective | Less efficient, noise from fans |
Thermoelectric Coolers (TECs) | Active | Precise cooling control, compact design | High energy consumption, limited capacity |
Active Heat Pipes | Active | Efficient heat transfer, compact | Integration complexity |
Integrated Thermal Management Systems | Both | Comprehensive temperature control | High cost, complex design and implementation |
List of Factors Influencing Thermal Management Selection
- Application Requirements: The specific needs of the application, such as energy density, charge-discharge rates, and safety, influence the choice of thermal management solution.
- Space Constraints: The available space within the device or system can limit the type of thermal management solution that can be implemented.
- Cost Considerations: The cost of materials, installation, and maintenance must be weighed against the benefits of the thermal management solution.
- Efficiency: The effectiveness of the thermal management solution in maintaining optimal temperature and preventing overheating.
- Reliability and Durability: The long-term reliability and durability of the thermal management solution, especially in demanding applications.
- Environmental Impact: The environmental impact of the thermal management solution, including energy consumption and material sustainability.
Future Trends in Thermal Management for Lithium-Ion Cells
The future of thermal management for Lithium-Ion cells is expected to see several advancements and trends aimed at improving efficiency, safety, and sustainability.
1. Advanced Materials
Research into advanced materials, such as nanocomposites and high-thermal-conductivity polymers, is expected to yield new solutions for passive thermal management. These materials can enhance heat dissipation and thermal stability without adding significant weight or cost.
2. Smart Thermal Management Systems
The integration of smart sensors and control systems can provide real-time monitoring and adaptive thermal management. These systems can adjust cooling strategies based on the cell’s operating conditions, improving efficiency and safety.
3. Hybrid Thermal Management Systems
Combining multiple thermal management techniques into hybrid systems can offer superior performance. For example, integrating PCMs with liquid cooling systems can provide both high heat capacity and efficient heat transfer.
4. Sustainable Cooling Solutions
Developing sustainable cooling solutions, such as using eco-friendly coolants and recyclable materials, will be crucial for reducing the environmental impact of Lithium-Ion cell thermal management.
Conclusion
Effective thermal management is essential for the performance, safety, and longevity of high-performance Lithium-Ion cells. By exploring and implementing advanced passive and active thermal management solutions, manufacturers can address the challenges associated with heat generation and dissipation. As technology continues to evolve, innovations in materials, smart systems, and sustainable practices will play a pivotal role in optimizing the thermal management of Lithium-Ion cells, ensuring their reliability and efficiency in a wide range of applications.